レーザー切断とプラズマ切断の選択方法:比較表
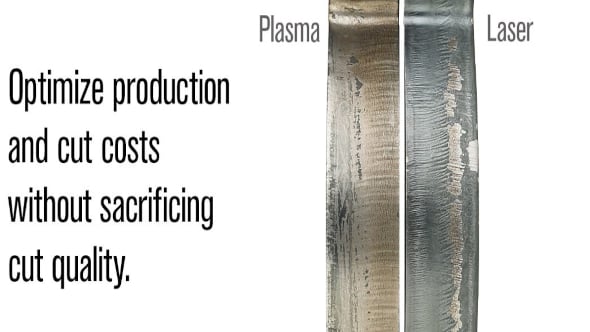
プラズマ切断システムとレーザー切断システムのどちらを選択するかを決める際には、多くの検討事項があります。別のブログでは 2 つのテクノロジーを詳しく紹介しましたが、今回は、切断品質、汎用性、コスト、安全性、時間の節約/自動化、耐久性、そして各テクノロジーが理想的な状況の 7 つの重要な違いに焦点を当てていきます。プラズマ切断とレーザー切断にはそれぞれ利点があるため、お客様のビジネスに合った適切な切断方法の選択は、切断ニーズ、特に切断する材料の種類、材料厚、切断の複雑さ、切断品質に関する顧客の要件によって異なります。
プラズマ切断とは?
プラズマ切断は、プラズマ高速ジェットを使用して、鋼鉄、アルミ、その他の金属などの導電性材料を切断する熱切断プロセスです。その速度と精度により、製造、建設、自動車産業における金属加工に一般的に使用されています。
レーザー切断とは?
ファイバーレーザー切断は、集中光線を使用して、さまざまな材料を切断、彫刻、マーキングする高精度で多用途の技術です。金属やプラスチックの切断から木材や陶器への複雑なデザインのエッチングまで、工業、商業、趣味の分野で幅広く使用されています。
切断品質
プラズマ切断とレーザー切断のどちらも切断品質に優れていますが、ファイバーレーザー切断では薄い金属でより優れた切断結果をもたらし、プラズマ切断では厚い金属でよりクリーンな切断を実現します。レーザーの切断品質は一般的にプラズマより優れていますが、プラズマの切断品質はほとんどの顧客の要求を上回るものです。したがって、より高品質切断のレーザー切断であっても、ユーザーや顧客にとって大きなメリットを提供できるとは限りません。
プラズマ
-
ISO 9013 レンジ 2 ~ 4 の切断品質
-
ファイバーレーザーの切断品質に匹敵し、ほとんどの顧客の要求を上回る
-
溶接準備に必要な二次加工は最小限
-
切断エッジが滑らかで真っ直ぐ
-
酸化層とドロスは最小限
レーザー
-
ISO 9013 レンジ 1 ~ 2 の切断品質
-
薄い切り口のサイズと低テーパー角度の利点
-
高い精度と正確性
-
薄い金属で優れた切断品質を発揮
-
厚さが 12 ~ 16 mm を超えると、表面の仕上がりが粗くなり、ドロスが増える
切断の汎用性
プラズマ切断もレーザー切断も非常に汎用性が高く、複雑な形状を切断、彫刻、マーキングすることができます。レーザーはより多くの材料を切断できますが、クリーンな材料が必要なため、クリーニングや切断前気化プロセスが必要な場合もあり、生産性が低下します。プラズマは、不完全で汚れた金属を切断できますが、プラスチックを切断することはできません。したがって、どちらを選択するかは、お客様のビジネスニーズによって異なります。
プラズマ
-
スタンドオフ距離が大きくなり切断プロセスでの干渉が少ない
-
直線、開先、穴、複雑な形状を切断
-
ステンレス、軟鋼、アルミ、銅、真鍮、その他の金属を切断
-
不完全で塗装済み、錆びのある、またはコーティングされた材料を切断
レーザー
-
切断、彫刻、およびマーキングが可能
-
複雑な形状を切断可能
-
スチール、アルミ、銅、プラスチック、複合材料を切断
-
特殊グレードの材料、手動クリーニング、または切断前気化プロセスが必要
-
生産性が低下
切断コスト
レーザー切断システムは、通常、プラズマ切断システムよりも 2 ~ 5 倍高額ですが、レーザーシステムでは使用する消耗部品が少なく、材料の無駄を最小限に抑えます。どちらのシステムが時間経過とともにより高価になるかは、システムの使用方法によって異なります。通常、プラズマは 12 mm を超える厚さの材料を切断する場合に運用コストが低く、レーザーは薄い材料を切断する場合に運用コストが低くなります。
プラズマ
-
ROI は 2 年以下であることが多い
-
消耗部品はより手頃
-
後処理は最低限
-
12 mm 以上の厚さの材料を切断する場合、通常、ファイバーレーザーよりも低コスト
レーザー
-
切断システムはプラズマのコストの 2 倍から 5 倍
-
消耗部品数が少ない
-
材料の無駄を最小化
-
12 mm より薄い材料を切断する場合、通常、プラズマよりも低コスト
-
より厚い材料を切断する場合、ガスと電気のコストが高くなる
安全性
プラズマ切断はレーザー切断より安全です。プラズマ切断では、プラズマアークの視認性を高めるために眼の保護具のみが必要です。レーザー切断には、安全性を考慮した筐体と材料の取り扱いが必要です。
時間の節約/自動化
プラズマ
-
大量生産と高速切断向けにきわめて優れた選択肢
-
CNC システムと簡単に統合でき、自動切断や、複雑な形状やパターンを正確に切断可能
-
大量生産またはカスタムコンポーネント向けに優れた選択肢
-
ロボット切断向けに優れた選択肢
レーザー
-
より厚いプレートの場合、部品はスケルトンから除去するのが難しく、叩き出す必要がある
-
自動化、反復作業、大量生産向けに CNC システムと統合可能
-
薄い材料をより高速に切断
切断機の耐久性
プラズマシステムでは、簡単な社内でのメンテナンスが必要です。レーザーシステムは汚れた環境に敏感で、定期的なクリーニングと技術的なメンテナンスが必要となり、認定サービスセンターを必要とする可能性があります。
プラズマとレーザーが最も理想的な用途
プラズマ切断システムは、12 mm ~ 16 mm 以上の厚い材料や、より速い切断速度が求められる用途に最適です。レーザー切断システムは 12 mm ~ 16 mm より薄い材料で、高精度、優れたエッジ品質、複雑な切断が求められる用途に最適です。
結論:最良の選択は、お客様の用途によって異なります
プラズマ切断とファイバーレーザー切断には両方とも利点があるため、どちらが適切な選択肢であるかは、切断システムでどのような作業をするかによって異なります。プラズマはレーザーと比べて初期投資が少なく、メンテナンスが簡単で、使用も安全です。厚い金属ではレーザーより優れた性能を発揮し、薄い金属ではレーザーに匹敵します。
最終的には、切断する金属の厚さ、切断に必要な精度、そしてその高い精度に対してどの程度支払うつもりなのか、また、顧客から要求があるのかが問われます。
以下の比較表をご覧ください。
レーザー切断とプラズマ切断のより詳しい比較は、ブログ記事「プラズマ切断とレーザー切断の比較ガイド」をご覧ください。