生産性を向上させるには?
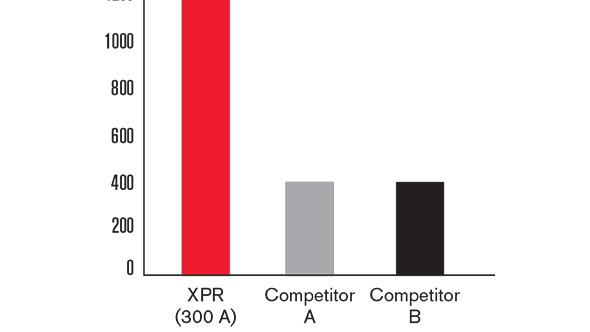
産業用切断機の生産性を左右する要素は、3 つ挙げられます。それは、切断速度、切断品質、そしてシステムランタイムです。Hypertherm の新しい XPR300 は、二次加工の必要性を減らす (あるいは完全に排除する) ため、より優れた切断品質、より早い切断速度、さらに、「スマート」テクノロジーと時間節約された手順によりシステムランタイムの向上といった、生産性に関わる 3 つの要素すべてに対応しています。
切断速度
300 アンペア、63 キロワットの XPR300 は、260 アンペアの旧モデルと比べ、切断速度が向上しました。その割合は切断する板厚にもよりますが、概して厚さ 15~40 mm の素材では 10~20%、厚さ 50 mm のものでは 38%、そして厚さ 60 mm のものは 50% 近く切断速度がアップします。
Thickness | XPR300 | HPR260XD | HPR400XD |
XPR300 |
HPR400XD versus XPR300 % |
|
15 mm | 3440 | 3130 | 3950 | 10% | 15% | |
20 mm | 2550 | 2170 | 2805 | 18% | 10% | |
25 mm | 1950 | 1685 | 2210 | 16% | 13% | |
30 mm | 1530 | 1290 | 1790 | 19% | 17% | |
40 mm | 940 | 790 | 1160 | 19% | 23% | |
50 mm | 560 | 405 | 795 | 38% | 42% | |
60 mm | 385 | 258 | 580 | 49% | 51% | |
70 mm | 250 | N/A | 380 | N/A | 52% |
切断速度 (mm/min)
さらに XPR300 は、HPR260XD と比べ切断速度だけでなく効率も向上します。以下の表のとおり、XPR300 はたった 170 アンペアで、HPR260XD が 200 アンペア必要とした切断速度を実現します。より速く切断できるだけでなく、切断工程におけるエネルギーの消費量を抑えることができるのです。
切断品質
切断品質について言えば、XPR300 は、X-Definition と呼ばれるまったく新しいクラスの切断を実現します。熱切断製品の切断品質を定義する国際規格、ISO 9013 による評価において、このクラスの切断では切断品質が高くなります。この規格は 1~5 の段階で評価を行い、レンジ 1 が最高の切断品質とされています。新しい XPR なら消耗部品の寿命期間中、ほぼ一貫して ISO レンジ 3 の切断品質を提供します。それに対し、Hypertherm の HPRXD システムは以下の通り、主にレンジ 4 の切断品質を提供していました。
上記の表は 12 mm の軟鋼を切断した際の結果であり、より低い電流でより薄い軟鋼を切断したラボのテストでは、ISO レンジ 2 の切断品質となっています。切断品質の向上に加え、一貫した品質が得られることも特筆すべき点です。表のように、ラボのテストでは 20 秒の切断が千数百回行われましたが、切断品質は著しく均一でした。最新の消耗部品で切断した部分と、1,000 回以上使用した消耗部品で切断した部分は、ほぼ同品質でした。
ステンレスとアルミだけでなく、軟鋼においても切断品質は大幅に改善されます。これは、特許出願中のいくつかの新技術によるものです。そのひとつは Vented Water Injection (ベント式ウォーターインジェクション) で、窒素プラズマガスをウォーターシールドと共に使用し、プラズマアークをより効果的に収束、集中させます。2 つ目は、Vent-to-Shieldと呼ばれる技術で、ベント式プラズマガスから水素を抽出し、それをシールドガスと混合します。これらの二つの技術により、HPR に比べ傾斜が少なく直角に近い切断端で切断することが可能となり、表面の仕上がりも改善されます。また、XPR は Advanced Arc Stability と呼ばれるプロセスを活用します。プラズマアークと新しいアークセグメンテーションプロトコルを安定させ、既に業界をリードしている Hypertherm の True Hole プロセスを凌ぐ孔を実現します。
システムランタイム
XPR には様々なテクノロジーが用いられていますが、システムはより単純です。電源装置内のセンサーが、洗練された診断コードと大きく強化されたシステム監視情報を生成します。これにより、トラブルシューティングの時間を削減し、システム全体をより最適化するためのプロアクティブなデータを提供します。
さらに、システムは以前よりコンソールやコネクター数が少ないデザインなので、オペレーターはセットアップにかける時間を減らし、切断に多くの時間を投じることができます。便利な特徴の一つは EasyConnect™ と呼ばれる接続デバイスで、オペレーターは工具を使用しなくてもトーチをトーチコンソールに素早く差し込むことが可能です。特許出願中の QuickLock™ 電極で 90° の締め付けが容易になり、作業のセットアップ時間をさらに短縮します。また、オペレーターが片手ですぐにトーチを交換できる新しいデザインを採用しました。コンソールはすべて、高度なオートガス機能を搭載し、オペレーターは CNC から直接切断ジョブを選択、実施することができます。また、電源装置は WiFi を搭載しており、単一あるいは複数のシステムを遠方から監視することが可能です。
総運用コストはもちろんのこと、システムのアップタイムを向上させるには、消耗部品の寿命を延長することが重要なポイントとなります。特許出願中の Cool Nozzle™ と呼ばれる機能は、液体で直接ノズルを冷却し、消耗部品の寿命を 40% 延長します。特許取得済みの PowerPierce® 技術は、基本的にシールドに対し同様の働きをします。冷却用の液体をシールドに送ることでピアシング中に溶融金属を寄せ付けず、シールドをダメージから守ります。また、トーチのレセプタクルにあるバルブはガスフローを素早く精密に制御し、酸素プロセスを各段に長持ちさせ、ランプダウンプロセスを大幅に加速します。以下に示す通り、多くのアプリケーションにおいてこのランプダウンエラーを排除することで、消耗部品の寿命他社のシステムの 3 倍近く長くなることがわかります。消耗部品の交換に費やす時間を減らせば、切断や他の価値ある作業により多くの時間を充てることができます。
これで、お分かりいただけたことでしょう。より優れた切断速度と切断品質に加え、各段に進化したシステムアップタイムを実現する XPR300 は、生産性を飛躍させます。
生産性を向上させるには?