Behlen Industries aumentata i profitti e investe sul futuro con la tecnologia al plasma
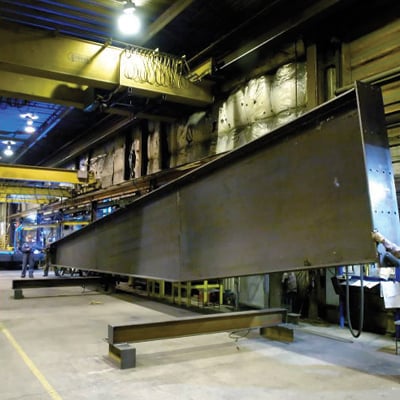
L’azienda e i prodotti
Behlen Industries è il maggiore produttore di sistemi di costruzione in acciaio del Canada. Con sede a Brandon, nella provincia del Manitoba, e un mercato internazionale in crescita, i sistemi di Behlen vengono venduti e installati in tutto il Nord America e in parte dell’Europa attraverso una rete di costruttori-distributori autorizzati.
Il problema
La macchina di taglio plasma di Behlen aveva 10 anni e aveva raggiunto la fine della sua durata utile e il team di produzione cercava un servizio di sostituzione attivo 24 ore su 24 e 7 giorni su 7. Il direttore di produzione Doug Riddoch, spiega, “Il sistema al plasma è un componente fondamentale per il flusso di lavoro all’interno dell’azienda. Se questo non funziona, ciò si ripercuote sul funzionamento dell’officina. Da questo dipende il flusso di lavoro, con 40 saldatori in attesa dei pezzi tagliati.”
La soluzione
L’azienda ha sostituito il vecchio sistema al plasma con una nuova® unità Versagraph Koike dotata della tecnologia SureCut™ di Hypertherm –® un sistema di taglio plasma HyPerformance HPR260XD con Autogas, un® CNC EDGE Pro, Sensor™ THC e ® software di nesting ProNest.
La nuova macchina di taglio ha già dato risultati straordinari e ha cambiato il modo di operare di Behlen. Riddoch ha commentato, “Da quando tre mesi fa è stato installato il plasma, abbiamo notato grandi miglioramenti nel modo di gestire i lavori e nei risultati ottenuti.”
Vantaggi
Solo per cominciare, la nuova macchina ha offerto a Behlen la flessibilità per alleviare i colli di bottiglia della produzione. Hanno potuto trasferire il lavoro da un’altra macchina lamiera, riportare il lavoro in azienda da fornitori esterni e consolidare alcuni progetti da altre sedi aziendali.
La programmazione presso Behlen comprende l’utilizzo del nesting automatico ProNest per raggiungere alti livelli di utilizzo del materiale senza necessitare dell’intervento di un programmatore. L’Evitamento delle collisioni viene applicato automaticamente a ciascuno schema di taglio, consentendo percorsi di strumenti, stili dell’attacco e posizionamento ottimizzati. I percorsi degli strumenti che ne derivano si traducono in migliore produttività del tempo di ciclo da taglio a taglio.
Sintetizzando i risultati dell’investimento sulla macchina, Riddoch afferma “Dal momento in cui riceviamo la documentazione per un lavoro, ora possiamo essere pronti a spedirlo in soli due giorni. Solamente portando in azienda alcuni dei lavori di tramoggia-bidone, abbiamo riscontrato un risparmio del 40 percento sui costi di quel determinato prodotto, oltre a risparmi significativi dei tempi di produzione del fascio di cavi. Tutti questi cambiamenti apportati al processo di lavorazione utilizzando la nuova macchina ci hanno aiutato a migliorare la nostra redditività.”