In che modo posso migliorare i miei profitti?
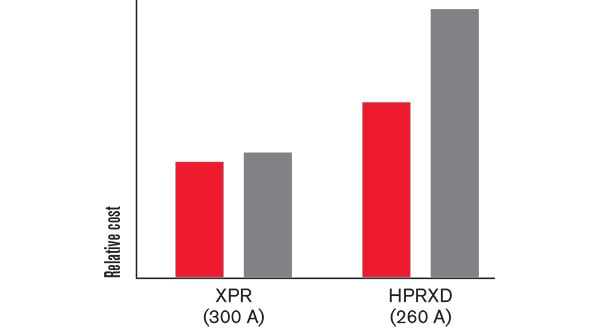
Un tema ricorrente nel progresso tecnologico del taglio plasma a partire dalla sua invenzione
è la continua riduzione dei costi di metallo tagliato al metro o al piede. Questo fenomeno, ampiamente accelerato con XPR300™, è per l’utente uno dei principali elementi trainanti della redditività. Questa drastica riduzione dei costi operativi con l’utilizzo di un XPR300 è correlata a diversi fattori tra cui velocità di taglio, durata dei consumabili e qualità di taglio.
Questo primo fattore è correlato alla velocità di taglio. XPR300 taglia dal 10 al 20 per cento più velocemente rispetto al suo predecessore su spessori cruciali e quasi il 50 per cento più velocemente per il taglio di materiali con spessore superiore a 50 mm.
Thickness | XPR300 | HPR260XD | HPR400XD | 0 |
XPR300 |
HPR400XD vs. XPR300 % |
15 mm | 3440 | 3130 | 3950 | 10% | 15% | |
20 mm | 2550 | 2170 | 2805 | 18% | 10% | |
25 mm | 1950 | 1685 | 2210 | 16% | 13% | |
30 mm | 1530 | 1290 | 1790 | 19% | 17% | |
40 mm | 940 | 790 | 1160 | 19% | 23% | |
50 mm | 560 | 405 | 795 | 38% | 42% | |
60 mm | 385 | 258 | 580 | 49% | 51% | |
70 mm | 250 | N/A | 380 | N/A | 52% |
Velocità di taglio (mm/min)
Degno di nota è anche il fatto che XPR300 è più efficiente perché richiede meno ampere per offrire le stesse prestazioni del suo predecessore. Come mostrato nella tabella che segue, un XPR impostato a 170 ampere offre una velocità di taglio pari a quella di un HPR a 200 ampere di corrente di uscita.
Un secondo fattore chiave che influisce sui costi operativi è la durata dei consumabili. Nei test di laboratorio, gli ingegneri Hypertherm sono stati in grado di realizzare il 50 per cento di tagli in più rispetto a quanto fosse possibile prima. Se prima un set di consumabili durava per un numero vicino a 1.000 tagli, ora i consumabili XPR possono eseguire un numero che si avvicina a 1.400 tagli da 20 secondi su acciaio al carbonio da ¾ di pollice. Una delle ragioni per questo aumento della durata dei consumabili ha a che fare con il design altamente sofisticato dell’XPR. Il generatore del sistema è dotato di una funzione chiamata Arc Response Technology che interviene automaticamente per prevenire eventi che possano danneggiare il sistema o ridurre la durata dei consumabili.
Per esempio, vediamo ora gli errori della chiusura graduale. Questi errori, in cui l’arco termina in maniera incontrollata spegnendo la lamiera o per la caduta di un elemento interno (come un foro o una scanalatura), sono molto dannosi per i consumabili. Questo accade perché il dispositivo di emissione dell’afnio sulla punta di tutti gli elettrodi non riesce a risolidificare quando l’arco “scatta” per spegnersi. Il risultato è l’emissione di un po’ di afnio dall’elettrodo ogni volta che si verifica una chiusura graduale che accelera l’usura dei consumabili.
Il generatore XPR300 affronta questo problema attraverso l’utilizzo di una sofisticata funzionalità di auto rilevamento. Il sistema rileva quando l’errore di chiusura graduale che sta per verificarsi e termina rapidamente l’arco in maniera incontrollata, prolungando di molto la durata dell’elettrodo e dell’ugello. Se molti sistemi al plasma vedono una riduzione della durata dei consumabili del 50 per cento a causa degli errori di chiusura graduale, per XPR300 questo tasso è inferiore al 10 per cento. Questo equivale alla realizzazione di un vantaggio nella durata dei consumabili quasi tre volte maggiore rispetto alla norma.
Un altro fattore importante da considerare è la qualità di taglio. XPR300 introduce una categoria di taglio completamente nuova chiamata X-Definition. Progressi come Cool noozle™, Advanced arc stability, taglio HyDefinition esteso al metallo non ferroso, Vented Water Injection (VWI), miscelazione discreta del gas (H2, Ar, N2), Vent-to-shield e Umidificatura del Plasma, in cui una camera nell’ugello assorbe le oscillazioni di pressione e flusso, hanno comportato un’eccezionale uniformità nella qualità di taglio per un lunghissimo periodo di tempo.
Se i sistemi HyPerformance HPR riuscivano a ottenere una qualità di taglio uniforme dei pezzi di gamma ISO 4, XPR300 riesce a ottenere una qualità di taglio uniforme di gamma ISO 3 e persino ISO 2 su materiali più sottili.
Questa qualità di taglio ampiamente migliorata sull’acciaio al carbonio, e ancora di più su acciaio inox e alluminio, può consentire ai produttori di riportare in officina i tagli che prima venivano fatti esternamente nei centri di taglio specializzati per il laser e altri tipi di taglio. Questo può portare a un considerevole risparmio sui costi, a una catena di fornitura migliorata e più efficiente (che permette di avere una produzione JIT – Just In Time), consegne dei lavori più veloci e una redditività complessiva maggiore.
Qualità del bordo sull’alluminio con
il processo VWI in attesa di brevetto disponibile sull’XPR300
Qualità del bordo sull’acciaio inox
con la capacità unica di XPR300
di miscelare H2-Ar-N2 come gas plasma nella consolle OptiMix.
Riassumendo, una combinazione di velocità di taglio più elevate, durata maggiore dei consumabili aumentata dalla protezione dagli errori di chiusura graduale, qualità di taglio migliorata e maggiore uniformità del taglio che porta direttamente a costi operativi più bassi e una redditività aumentata. In realtà, a 300 ampere di corrente in uscita, XPR300 è in grado di ridurre i costi relativi del taglio per metro o piede di oltre il 50 per cento.