Le logiciel ProNest soutient la volonté de Craig Manufacturing de relever des défis
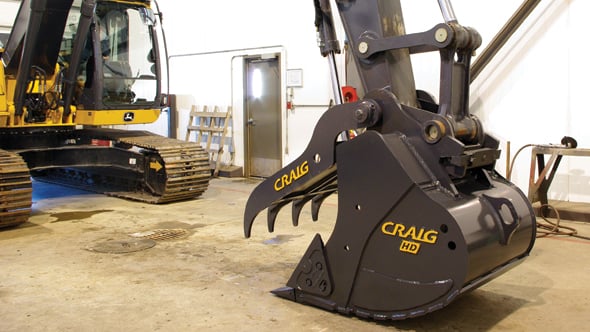
L’entreprise et ses produits
Craig Manufacturing de Hartland, au Nouveau-Brunswick, Canada, est le plus important fabricant privé de fixations ultrarésistantes en Amérique du Nord. Aujourd’hui, la société mène ses activités dans une usine de pointe de 71 000 pieds carrés à Hartland, et elle possède également une usine de 15 000 pieds carrés à Cambridge, en Ontario, pour la distribution et la fabrication spécialisée.
Le problème
Avec l’augmentation de la demande pour les produits de Craig Manufacturing, une plus grande capacité de coupe est devenue nécessaire. « Notre logiciel d’imbrication actuel est limité. La création d’imbrications est souvent un processus chronophage. » Chaque heure passée sur une imbrication ne produit environ qu’une heure de coupe. Le logiciel possède peu de caractéristiques automatisées, c’est pourquoi nous avons un engorgement au début de chaque procédé », déclare Colden Wetmore, responsable de l’exploitation.
La solution
L’équipe décisionnelle a regardé de près les dernières solutions proposées par Hypertherm, dont le logiciel CAO/FAO ProNest® . Elle était particulièrement intéressée par la façon dont ProNest interagirait avec son programme SOLIDWORKS® 3D CAO et s’intègrerait dans son flux de production précis. Elle souhaitait également améliorer la qualité des trous, et comme ProNest prend en charge la technologie True Hole® c’était un atout supplémentaire.
La nouvelle table plasma EBF est bien vite arrivée chez Craig Manufacturing. Équipée d’un HPR400XD, d’une EDGE® Pro CNC et d’ArcGlide® THC, et programmée par ProNest.
« Avec notre précédent logiciel, nous avons passé six ans à régler les paramètres de coupe sans trouver les bons, déclare Wetmore, puis arrive ProNest avec tous ces paramètres intégrés. »
Les avantages
Maintenant, au lieu d’une heure de coupe pour chaque heure d’imbrication, l’entreprise obtient 19 heures de coupe, soit 19 fois la productivité! Et la technologie True Hole, améliorant la précision et la qualité des trous a permis une réduction considérable des opérations secondaires de meulage.
Wetmore ajoute, « Depuis l’installation de la nouvelle table avec la technologie Rapid Part™, même notre opérateur le plus expérimenté ne pouvait plus suivre les exigences grandissantes de chargement et déchargement des plaques. Nous avons donc dû modifier notre débit pour suivre.« L’entreprise constate également une meilleure utilisation des matériaux. Nous avons réduit de moitié notre stock de matériaux bruts. Aujourd’hui, grâce à ProNest, notre équipe de direction est ravie, car l’argent consacré aux plaques a été réduit sans sacrifier les délais de fabrication. »