En Olympic Steel, el software de anidamiento para láser ProNest ha sido todo un éxito
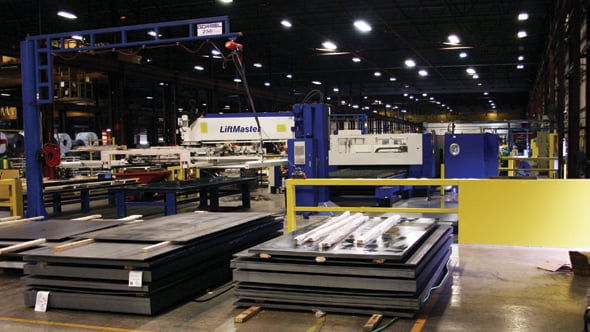
La compañía y sus productos
Con sede en Cleveland, Ohio y con 15 instalaciones operando en todo Estados Unidos, Olympic Steel es un proveedor de valor agregado de acero laminado. Una gran parte del negocio de la compañía es el procesamiento de corte a la medida, que se realiza en más de 30 máquinas de corte por plasma, láser y gas de distintos fabricantes.
El problema
Mientras que el procesamiento de corte láser a la medida ha contribuido considerablemente al crecimiento y rentabilidad de Olympic en los últimos años, el costo relativamente alto del capital de los equipos con tecnología láser CO2 requiere niveles de productividad igual de altos para poder alcanzar el rendimiento de inversión (ROI) necesario. Y la programación CAM desempeña un papel importante en lograr ese ROI. A medida que se fueron agregando capacidades láser, Olympic se encontró usando numerosos programas de software CAM de terceros y fabricantes de equipos originales.
Como resultado, los programadores CAM tenían que capacitarse para operar varios productos de software de anidamiento para láser y la compañía afrontaba costos anuales de actualización y mantenimiento de software cada vez mayores. Se tomó una decisión estratégica para buscar e implementar un método corporativo más global de programación CAM que ayudara a Olympic Steel a lograr sus objetivos de productividad.
La solución
Después de un meticuloso periodo de evaluación, la compañía optó por ProNest® para la mayoría de sus operaciones de corte de láminas y placas con CNC a nivel nacional. Cory DeWitte, especialista en planificación con CNC, afirma: “ProNest tiene tantas funciones que encuentro realmente fantásticas y que nosotros usamos en particular en los láseres.” Agrega: “La opción deevasión de colisiones de ProNest ha sido colosal para nosotros, especialmente para usarla con algunos láseres más antiguos en los que subir y bajar los cabezales es más lento. Ahora podemos hacer el recorrido con el cabezal de corte abajo frente a una retracción total al terminar cada perforación, lo que significa un ahorro de más de una hora de tiempo de producción al día por cada láser, ¡impresionante! Ahora vemos una reducción considerable del desgaste de las máquinas láser, lo que nos reduce el costo”.
Beneficios
Las mejoras de velocidad y mayor utilización de material han sido considerables, algo que se agradece en el balance final. DeWitte sigue: “Ahora ProNest me deja programar ocho máquinas al día, de modo que ha más que duplicado nuestra productividad de programación. Además, prácticamente siempre logramos un mínimo de setenta por ciento de utilización del nido, aun en las geometrías de piezas más difíciles”. “La opción de corte de línea común de ProNest disminuyó nuestro tiempo de producción del doce al cuarenta por ciento”.