El software ProNest ayuda a que Craig Manufacturing se anime a tomar casi cualquier desafío
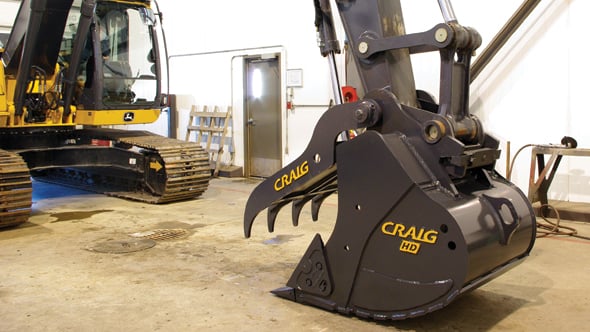
La compañía y sus productos
Craig Manufacturing de Hartland, New Brunswick, Canadá es el mayor fabricante de accesorios para equipos de trabajo pesado de propiedad privada en América del Norte. La compañía trabaja desde unas instalaciones modernas de 71 000 pies cuadrados en Hartland y ha agregado otras instalaciones de 15 000 pies cuadrados en Cambridge, Ontario, para la distribución y fabricación de productos especiales.
El problema
A medida que el negocio en Craig Manufacturing crecía, surgió la necesidad de tener mayor capacidad de corte. “Nuestro software de anidamiento existente tenía sus limitaciones; crear nidos a menudo era una tarea que demoraba mucho. Cada hora que pasábamos con el anidamiento, solo produciría una hora de corte. El software no contaba con demasiadas funciones automatizadas, entonces terminábamos con un embrollo al inicio del proceso”, comentó Colden Wetmore, gerente de operaciones.
La solución
El equipo encargado de las decisiones evaluó exhaustivamente las soluciones de Hypertherm más recientes, incluyendo el software ProNest® CAD/CAM. Tenían particular interés en cómo ProNest interactuaría con su SOLIDWORKS® CAD 3D, y cómo se adaptaría a su flujo de trabajo en particular. También deseaban mejorar la calidad de los orificios y como ProNest es compatible con la tecnología True Hole® de Hypertherm, eso representaba un beneficio adicional.
No pasó mucho tiempo para que llegara la nueva mesa de plasma EBF de Craig Manufacturing. Vino equipada con un HPR400XD, CNC EDGE® Pro, THC ArcGlide® y programada por ProNest.
“Con nuestro software anterior pasamos seis años modificando los parámetros de corte y nunca eran los correctos”, comentó Wetmore; “luego llegó ProNest, con todos los parámetros incorporados”.
Beneficios
Ahora en vez de una hora de corte por cada hora de anidamiento, la compañía logra 19 horas, ¡eso es un aumento de la productividad multiplicado por 19! Además, el mejoramiento de la calidad y de la precisión de los orificios gracias a la tecnología True Hole ha permitido disminuir en gran medida las operaciones secundarias de rectificación.
Wetmore añade: “Desde que instalamos la mesa nueva, que incluye tecnología Rapid Part™, hasta nuestro operador más experimentado no podía seguir el ritmo de los requisitos de mayor carga y descarga de placas; tuvimos que cambiar nuestro flujo para estar a la altura.” También están notando una utilización de material optimizada. “Redujimos a la mitad nuestro inventario de materia prima. Hoy en día, gracias a ProNest, nuestra gerencia está más feliz porque hemos reducido el dinero inmovilizado en placas sin afectar las entregas”.