Behlen Industries aumenta las ganancias y construye a futuro con la tecnología de plasma
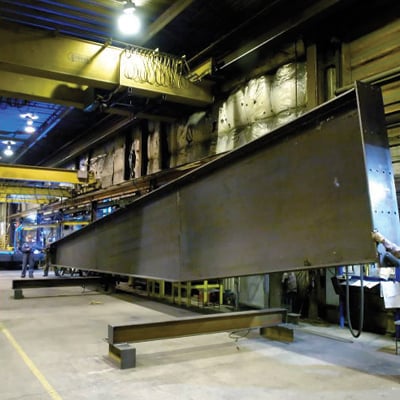
La compañía y sus productos
Behlen Industries es el mayor productor de sistemas de construcción en acero de Canadá. Con sede en Brandon, Manitoba y un mercado internacional en expansión, los sistemas de Behlen se venden e instalan en toda América del Norte y partes de Europa mediante una red de distribuidores autorizados para constructores.
El problema
Una vieja máquina de corte por plasma de 10 años de Behlen había alcanzado su fin de ciclo de servicio y el equipo de producción pretendía conseguir con su reemplazo un servicio disponible las 24 horas del día, los 7 días de la semana. Doug Riddoch, gerente de producción, explica: “Consideramos que el sistema de plasma es un componente vital en el flujo de trabajo de la compañía. Si no funciona, realmente afecta la operación en el taller. Dirige el flujo de trabajo, con 40 soldadores esperando por las piezas a cortar”.
La solución
La compañía reemplazó el viejo sistema de plasma con una nueva unidad Koike® Versagraph equipada con tecnología SureCut™ de Hypertherm, un sistema de corte por plasma HyPerformance® HPR260XD con gas automático, CNC EDGE® , Sensor™ THC y software de anidamiento® ProNest.
La nueva máquina de corte ya ha generado resultados impresionantes y cambiado la forma en que opera Behlen. Riddoch afirmó: “Desde que instalamos el plasma hace tres meses, hemos visto mejoras importantes en la manera en que procesamos los trabajos y los resultados que alcanzamos”.
Beneficios
Para empezar, la máquina nueva le ha dado a Behlen la flexibilidad de solucionar los embrollos de producción. Pudieron transferir trabajos desde otra máquina de placas, volver a traer trabajos al taller que antes les enviaban a proveedores externos y consolidar algunos proyectos desde otras ubicaciones de la compañía.
La programación en Behlen incluye el uso del anidamiento automático ProNest para alcanzar altos niveles de utilización de materiales sin la intervención de un programador. La evasión de colisiones se aplica automáticamente a cada nido, lo que produce rutas optimizadas para las herramientas, mejores estilos del conjunto de cables y mangueras y posicionamiento. La ruta resultante para las herramientas se traduce en mejoras en la productividad del tiempo de ciclo entre cortes.
Al resumir los resultados de la inversión en la máquina, Riddoch comenta: “Desde el momento en que recibimos el papeleo para un trabajo, ahora estamos en condiciones de enviarlo en solo dos días. Simplemente al traer algunos de los trabajos de los silos tipo tolva al taller, hemos visto un ahorro en los costos de un 40 por ciento, solo en ese producto, además de importantes ahorros en los plazos de entrega de la producción. Todos estos cambios a la forma en que procesamos los trabajos con la máquina nueva nos han ayudado a aumentar nuestra rentabilidad”.