La nueva definición del corte por Plasma
La nueva generación de corte plasma de Hypertherm
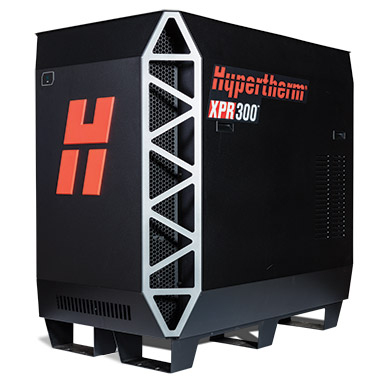
Actualmente, la industria metalmecánica cuenta con diversas soluciones para el corte de metales como el Plasma, Laser, Chorro de Agua, Oxicorte, además de una variedad inmensa de modalidades de corte mecánico. Aunque todos los procesos mencionados ya estén bien establecidos y con un buen historial en nuestro mercado, cada uno posee sus beneficios y deficiencias que deben ser considerados al decidir qué método de corte utilizar para una determinada aplicación.
En Brasil y en toda América del Sur, el Plasma viene rápidamente convirtiéndose en una de las elecciones más populares entre los fabricantes modernos, especialmente cuando hablamos de la fabricación de productos metálicos que pueden no obtener los mejores resultados cuando se utilizan otros métodos de corte tradicionales. No sólo el plasma proporciona un buen equilibrio en términos de costos de inversión y operacional, sino también es una combinación ideal de calidad de corte, además de ofrecer altas velocidades de corte y ser un proceso extremamente versátil.
Entonces, ¿qué es el plasma? Definido de una manera más simple, el corte por plasma es una tecnología que usa un gas ionizado de alta temperatura para producir un arco eléctrico muy caliente, con alta densidad de energía que puede cortar cualquier material eléctricamente conductivo. La corriente del plasma es típicamente formada forzando los gases como el Nitrógeno y el Oxígeno, o inclusive aire comprimido, a través de una boquilla con un orificio estrecho, mientras una corriente eléctrica producida por una fuente de alimentación externa adiciona energía suficiente para ionizar el flujo de gas, transformándolo en un arco de plasma con temperaturas que pueden llegar fácilmente a los 25000° C. El arco de plasma derrite y corta el metal. Este es el principal proceso para sistemas de corte manual y mecanizado.
La Ventaja del Plasma
Sistema de Corte Plasma por aire comprimido Hypertherm Powermax85
En lo que respecta al corte de metales, diversos factores pueden afectar la eficiencia, siendo un factor crítico la velocidad del corte. En los procesos de fabricación, este factor es extremamente importante, considerando que la velocidad de corte es directamente proporcional a la productividad, o sea, cuanto mayor sea la velocidad de corte, mayor será la productividad. Comparado a otros procesos de corte, el plasma corta con mayor velocidad y es el proceso de corte más rápido para chapas de 6 a 76mm, debido a la capacidad del arco plasma de derretir el metal casi instantáneamente después del contacto. Las velocidades de corte también aumentan a medida que la espesura del material disminuye y, ese aumento de velocidad quiere decir que el operador puede cortar más piezas en menos tiempo.
La calidad de corte es otro factor crítico en la elección de las empresas cuando precisan seleccionar un equipo para cortar metales. El corte por plasma, particularmente el Plasma de Alta Performance, es capaz de producir bordes relativamente lisos con poca rigidez del borde, lo que permite una excelente soldabilidad después del corte. Además, produce una escoria mínima, lo que reduce la necesidad de procesos secundarios de limpieza y preparación como esmerilado. En general, el plasma produce cortes de alta calidad más limpios y más precisos se comparados al oxicorte.
En los últimos años, la facilidad de operación de los procesos técnicos también viene ganando importancia como un factor decisivo en lo que atañe a la inversión tecnológica, principalmente por minimizar la necesidad de entrenamientos, mejorar la seguridad y, principalmente, aumentar los lucros. En conjunto con la última palabra en CNC y Software, el plasma se vuelve un proceso extremamente fácil de aprender y usar con los parámetros predefinidos que son incorporados por el Software de Aprovechamiento (CAM), minimizando la necesidad de experiencia previa del operador. Además, los sistemas de corte por plasma manuales son altamente portátiles gracias a su tamaño y peso relativamente compactos.
Otra grande ventaja del corte por plasma es la versatilidad. A medida que el corte por plasma usa un arco eléctrico de gas ionizado de alta temperatura para cortar todo material eléctricamente conductivo, puede ser usado para el corte de materiales ferrosos y no-ferrosos y para metales que estén en cualquier condición, incluso pintado u oxidado. Esto le confiere un mayor grado de flexibilidad al trabajo de corte, pues el plasma permite cortar una amplia gama de tipos y espesuras de materiales. La versatilidad de los sistemas de corte por plasma puede además ser aumentada cuando se la combina con antorchas y consumibles específicos. Hay disponibles diversas opciones de antorcha variando en ancho y ángulo para atender las diferentes necesidades de aplicaciones industriales. El plasma puede ser utilizado por arrastre (boquilla de contacto tocando la chapa para guiar al operador), distanciado (sin tocar la pieza para el acceso a lugares más difíciles) y hasta para obtener cortes más delicados con alta calidad en materiales más finos, simplemente sustituyendo algunos consumibles de la antorcha. Esta es una característica muy atractiva, pues un único sistema de corte por plasma puede emplearse en una variedad de aplicaciones con cambios simples para adecuarse a los procesos industriales, sin tener que alternar entre varias herramientas para completar el trabajo.
Además del corte, los Sistemas de plasma pueden también realizar otras tareas alternativas al mismo tiempo. Un ejemplo muy común es el ranurado y aplicaciones típicas que incluyen la retirada de una soldadura preexistente durante un servicio de reparación, desmontaje con retirada de soldaduras o incluso limpieza de raíz o pases de soldadura para procesos de múltiples camadas de soldadura. El corte por plasma es, por lo tanto, capaz de satisfacer las necesidades de corte y ranurado en una amplia gama de aplicaciones industriales, sea para metales más finos o más espesos, ferrosos o no-ferrosos.
El plasma puede ser utilizado también para marcar materiales, sea con letras y números para identificación de piezas cortadas o simplemente para marcar líneas de soldadura o doblez en la continuación del proceso de fabricación. Los sistemas automáticos modernos permiten que se corte y se marque utilizando los mismos consumibles, aumentando considerablemente la productividad.
En conformidad a lo que ilustramos más arriba, el plasma ofrece una combinación ideal entre calidad y productividad, conveniencia y versatilidad sea para aceros al carbono, inoxidables o aluminio en una amplia gama de espesuras. Los sistemas de plasma existentes son extremamente competentes y eficientes, pero los fabricantes vienen buscado en los últimos años mayor eficiencia y mejores resultados. Junto con el advenimiento de la tecnología, tenemos ahora una creciente demanda por sistemas de corte más desarrollados y sofisticados que atiendan las necesidades de la fabricación moderna.
Con esto en mente, Hypertherm recientemente lanzó su más avanzado sistema de corte mecanizado, el XPR300™.
Conozca el nuevo plasma
Equipo único en su segmento, el XPR300 representa el avance más significativo en la tecnología de corte por plasma mecanizado. Comparado al sistema antecesor, líder del sector - la línea HPRXD® - el nuevo sistema presenta un salto en el desempeño de corte y en la relación costo-beneficio. Ofrece una calidad de corte inigualable en varios metales (acero carbono, inoxidable y aluminio), aumentando la velocidad de corte, mejorando la productividad y reduciendo hasta en un 50% los costos operacionales. Además, los nuevos recursos de facilidad de uso y optimización del sistema de ingeniería hacen que el XPR300 sea más fácil de utilizar con la mínima intervención del operador, al mismo tiempo que garantiza un desempeño optimizado y confiabilidad.
Estos avances se atribuyen a una serie de nuevas tecnologías de proceso que Hypertherm denominó como corte “X-Definition” (vea la tabla 1).
Mayor Productividad y Rentabilidad
Para la mayoría de los fabricantes en la industria, existen dos beneficios más buscados en un equipo de corte por plasma: mejor desempeño y mejor costo-beneficio. Estas son las principales áreas que Hypertherm procuró alcanzar con la introducción del XPR300.
Cuando se trata o no, de corte industrial, productividad y rentabilidad, se hace mención a Velocidad de Corte, Calidad de Corte, Vida Útil de los Consumibles y Tiempo de Actividad del Sistema. El XPR300 aborda esos cuatro aspectos con un sistema que permite cortar más rápido, mejor y de forma más eficiente, con la utilización de una tecnología “inteligente” y algunos pasos que buscan economizar tiempo.
Velocidad de Corte - con 300 amperes y 63Kw de potencia, en comparación con los 260 amperes y 45.4 Kw ofrecidos por su antecesora (HPR260XD), la XPR300 puede cortar más rápido. El aumento específico en la velocidad depende de la espesura del material, sin embargo los usuarios pueden esperar un aumento de entre un 10 y un 20% en materiales entre 15 y 40mm de espesura, un 39% en materiales de 50mm y casi un 50% en 60mm de espesura. Esas mejorías en la velocidad de corte se traducen en mayor productividad y rentabilidad, una vez que se pueden completar más trabajos en la misma fracción de tiempo.
Espesura | Vel. de corte (mm/min) | |||
XPR300 | HPR260XD |
XPR300 |
||
15 mm | 3440 | 3130 | 10% | |
20 mm | 2550 | 2170 | 18% | |
25 mm | 1950 | 1685 | 16% | |
30 mm | 1530 | 1290 | 19% | |
40 mm | 940 | 790 | 19% | |
50 mm | 560 | 405 | 38% | |
60 mm | 385 | 258 | 49% |
La XPR300 corta de un 10 a un 20% más rápido que su antecesora en metales hasta 40mm de espesura, y aproximadamente un 50% más rápido en materiales con espesuras superiores a los 50 mm.
Además de las mayores velocidades de corte, la XPR300 es más eficiente que la HPR260XD® . Por ejemplo, la XPR300 requiere sólo 170 amperes para alcanzar la misma velocidad de corte que una HPR260XD a 200 amperes. No sólo permite un corte más rápido, sino que la XPR300 también consume menos energía en el proceso de corte.
La velocidad de corte de una XPR300 a 170 amp es comparable a la de una HPR usando 200 amp de corriente de corte.
Calidad de Corte - El factor de diferenciación está en el exclusivo corte “X-Definition” de Hypertherm que mejora la capacidad del plasma en aplicaciones de alta precisión. Esta clase de corte mejora la calidad cuando se utiliza como patrón de calidad la norma ISO9013, estándar internacional que define la calidad de corte para los procesos de corte térmico. Esta norma usa una escala de 1 a 5, siendo 1 considerado el mejor. La Nueva XPR300 entrega calidad de corte en la escala 3 (ISO Rango 3) durante toda la vida del consumible y el corte en acero carbono fino (inferior a 6mm) queda consistentemente dentro de la escala 2 (ISO Rango 2). En comparación, los sistemas HPRXD de Hypertherm tienden a entregar los cortes en la escala 4 (ISO Rango 4).
El proceso de corte de acero carbono con 300 Amp de la XPR300 se mantiene en la ISO Rango 3 por prácticamente toda la vida del consumible - 1368 cortes de 20s en chapa de 20 mm, comparado al ISO Rango 4 de su antecesora (HPRXD).
El proceso de corte de acero carbono con 80 Amp de la XPR300 se mantiene en la ISO Rango 2 por aproximadamente 1300 cortes de 20s en chapa de 6 mm antes de cambiar a la ISO Rango 3.
ISO Rango 2 em Aço Carbono
Muestra de corte presentando la calidad de corte y el borde afilado en el corte de acero inoxidable, usando la capacidad de la XPR300 de mezclar gases de plasma (H2-Ar-N2) con la consola OptiMix.
Además del aumento en la calidad de corte, otro aspecto notable es la consistencia del corte. La XPR puede producir piezas con calidad uniforme de corte, resultado obtenido a través de diversas nuevas tecnologías patentadas por Hypertherm. Entre ellas, citamos la inyección ventilada de agua (VWI), que combina el Nitrógeno como gas plasma con una protección de un espray de agua para mejor alinear y focalizar el arco plasma. Una segunda tecnología, llamada “Vent-to-Shield”, recupera el hidrógeno del gas plasma y lo mezcla al gas de protección. En conjunto, estas dos tecnologías son capaces de producir bordes más afilados con menor angularidad y una superficie de corte con acabamiento optimizado cuando se lo compara a los sistemas HPRXD. La XPR también utiliza un proceso llamado “Advanced Arc Stability”, proyectado para estabilizar el arco plasma desde el momento de la perforación de la chapa, además de nuevos protocolos para segmentación para orificios que sobrepasan el proceso de True Hole® de Hypertherm ya existente en los sistemas HPRXD. Eso permite que la XPR300 produzca orificios listos para pasar tornillos hasta una proporción de diámetro/espesura de 1:1. A medida que la calidad de corte es mejorada, los cortes que eran tercerizados para empresas que cortan con láser u otros procesos de corte especializados pueden ser realizados dentro de su propia fábrica, reduciendo el tiempo de fabricación y los costos adicionales con corte y logística. Con una antorcha proyectada para alcanzar la mejor performance, también se mejoró el desempeño en cortes especiales con aplicaciones de corte 3D, Robótico y Biselado. Con un mayor ángulo de ataque, las operaciones que exigen mayor movimiento y angularidad de la antorcha se hicieron aún más fáciles, reduciendo costos operacionales.
Durabilidad de los consumibles –
La XPR300 viene equipada con un recurso de patente pendiente llamado Cool Nozzle, que lleva refrigeración líquida directamente al cuerpo de la boquilla de corte, aumentando la vida útil de los consumibles. Durante los test de laboratorio, llegamos al número de 1400 cortes de 20s en chapa de acero carbono de 19mm lo que representa un 50% de mejoría. El aumento de la vida útil de los consumibles es aún mejorado a través de la nueva Tecnología de Respuesta del Arco, que consiste en dos recursos específicos: Protección Automática de la Antorcha y Protección Automática contra Errores de Rampa.
En el corte, los errores de rampa son considerados los villanos cuando se trata de vida útil de los consumibles. Esos errores ocurren cuando el arco se cierra de manera descontrolada al salir de la chapa o en el corte de orificios apagando el arco por la falta de material. Cuando esto acontece, la inserción de Hafnio, localizado en la punta de los electrodos no consigue volver a solidificarse cuando el arco se apaga. Como resultado, cada vez que ocurre un error de rampa, un poco de ese Hafnio es eyectado del electrodo, acelerando el desgaste del consumible.
La fuente de energía XPR300 controla este problema utilizando la Protección Automática contra Errores de Rampa, en la que el sistema detecta automáticamente cuando va a acontecer un error de rampa y cierra el arco de forma controlada, permitiendo que el Hafnio vuelva a solidificarse, prolongando la vida útil del electrodo y boquilla de corte. Aunque la mayoría de los sistemas de plasma presentan una reducción de aproximadamente un 50% en la vida de los consumibles por errores de rampa, con la XPR300 esa tasa se reduce a menos del 10%. Eso equivale a una ganancia real en la vida de los consumibles de casi tres veces, traducido en reducción de costos para el cliente final.
Tiempo de Actividad del Sistema - las mejorías en la vida útil de los consumibles, mencionadas anteriormente también contribuyen al tiempo de actividad del sistema. La tecnología patentada “Power Pierce” lleva refrigeración líquida hasta el escudo protector, lo que ayuda a repeler el metal derretido que retorna en el momento de la perforación de chapas más espesas, evitando así que el escudo sea prematuramente dañado. Con menos tiempo utilizado en el cambio de consumibles, los operadores ganan más tiempo para cortar y realizar otras actividades.
El XPR300 es uno de los sistemas de corte por plasma mecanizados más inteligentes ya lanzados hasta el momento. Los sensores instalados en diversos puntos del equipo monitorean continuamente la corriente, presión y flujo de gases, temperatura y las comparan con las especificaciones durante la operación para garantizar el mejor tiempo de actividad del sistema.
Con la combinación de velocidades de corte más rápidas, calidad de corte mejorada, mayor vida útil de los consumibles y mayor tiempo de actividad del sistema, la XPR representa una mayor productividad y un menor costo operacional.
Comparativo de costos por metro de corte entre la XPR300 y su antecesora HPRXD.
Recursos focalizados en el Usuario
A pesar del gran volumen de tecnologías encontradas en la XPR300, el sistema es sorprendentemente sencillo y fácil de usar. Los sensores de la fuente de energía suministran códigos de diagnóstico refinados e informaciones de monitoreo del sistema significantemente mejorados. Estos recursos permiten reducir el tiempo para la solución de problemas y proporcionan datos proactivamente para optimizar la condición general del sistema.
Además del monitoreo automático del Sistema, la XPR posee varios otros recursos que redefinen la facilidad de uso. Por un lado, el sistema está proyectado con menos consolas y conexiones para que los operadores gasten menos tiempo de configuración y más tiempo cortando. Otros recursos importantes como el dispositivo de conexión de la antorcha “Easy Connect”, que le permite al operador conectar el cable de la antorcha en la consola sin el uso de herramientas y un electrodo “Quick Lock” con patente pendiente que le permite al operador sustituir el electrodo sin herramientas con sólo ¼ de vuelta, reduciendo aún más el tiempo de configuración del sistema.
La nueva XPR300 incluye también la capacidad de conexión Wi-Fi incorporada en la fuente de energía. Los propietarios, gerentes y operadores pueden usar este recurso para monitorear el sistema o ejecutar tareas de configuración de proceso utilizando un Smart Phone, Tablet u otros dispositivos portátiles. El Wi-Fi puede también ser conectado a una red local para rastreo y control de múltiples sistemas. Significativamente, la XPR300 soporta la Industria 4.0.
Conclusión
En conformidad con lo ilustrado arriba, la XPR300 de Hypertherm representa la próxima generación de sistemas de corte mecanizado líder de la industria. Con una combinación de innovación tecnológica y diseño inteligente, esta nueva generación de sistema de corte por plasma ofrece el más alto estándar de desempeño en acero carbono, inoxidable y aluminio, expandiendo las posibilidades y capacidades de corte de una manera anteriormente imposible.
Última Tecnología de Proceso | Detalles |
---|---|
Vortex de Alto Flujo o Tecnología de Boquilla Ventilada | Una boquilla ventilada de dos piezas con diseño exclusivo que alinea y concentra el arco de plasma para aumentar la estabilidad del arco y la densidad de energía, que proporciona una calidad de borde más afilado, nítido y consistente en todos los materiales, incluyendo acero inoxidable y aluminio. |
Inyección Ventilada de Agua (VWI) | Un proceso con patente pendiente que contempla N2 como gas de plasma y H2O como protección para menor angularidad y bordes más afilados en cortes de aceros inoxidables y principalmente aluminio. |
Vent-to-Shield | Un proceso donde el Hidrógeno del gas de plasma se recupera y se mezcla nuevamente al gas de protección, reduciendo la angularidad y proporcionando colores y bordes más consistentes en el corte de aceros inoxidables hasta 12mm. |
Plasma Dampening | Un recurso que adiciona una cámara en la boquilla para absorber las fluctuaciones de presión y flujo de los gases que crean inestabilidad de arco al cortar con bajas corrientes y arcos muy contraídos, requeridos para el corte de inoxidables de baja espesura. Esto elimina la irregularidad y ondulación de la superficie del corte. |
Cool Nozzle | Un recurso de patente pendiente en el proceso de corte de 300 Amps con O2 y aire comprimido donde el enfriamiento líquido es llevado hasta el orificio de la boquilla de corte, aumentando la calidad del corte durante la vida de los consumibles en más del 40% |
Estabilidad de Arco Avanzada | Una tecnología que reduce el impacto del gas de protección para mejorar la estabilidad de arco en la perforación o ángulos agudos. Esto puede traer como resultado la reducción de las entradas de corte. |