What is nesting software?
When manufacturers and fabricators cut parts out of sheet metal, plate metal, or other materials using a CNC cutting machine, a “nest” is used to maximize the material utilization in the cutting process.
Nesting is defined as the efficient placement of multiple parts or shapes onto a given surface area. In the industrial cutting industry, plate metal and other raw materials are expensive and it’s best to “nest” as many parts together as possible. This maximizes the plate utilization, reduces material waste, and lowers material costs.
Nesting software is a type of CAM (computer aided manufacturing) software used to prepare part geometry for cutting and creating nests. First, the part geometry is imported – typically in a CAD file format such as DWG or DXF. Next, the part files are prepared for cutting by applying various parameters such as lead-ins and lead-outs, cut direction, and more. Once the individual parts are prepared, the nests are created.
This can be done manually by the software user dragging and dropping parts toarrange the nest, or it can be done automatically by the software application. This approach uses one or more mathematical nesting algorithms to automatically add shapes to the nest while rotating and moving parts for the best overall fit and tightest material usage. In many cases the software can account for different jobs, with multiple combinations of parts, plates, and nesting strategies to deliver the best overall results. Nesting results can vary greatly based on the size and shape of the parts, but a typical industry nest may result in 70% material utilization with 30% scrap
Benefits of nesting software
- Material Optimization:
Nesting software arranges parts on material sheets in the most efficient way possible, significantly reducing waste. This optimization can lead to substantial cost savings by maximizing material usage. - Increased Efficiency:
By automating the nesting process, the software speeds up production. Efficient nesting tools and features, including fully automated nesting, eliminate the need for manual programming, which is time-consuming and prone to errors. This leads to faster turnaround times and improved overall productivity and material efficiency. - Cost Reduction:
With better material utilization and increased efficiency, overall production costs are lowered. This includes savings on raw materials and reduced labor costs due to less manual intervention.
Nesting software typical features
-
Ability to import various file types including DXF, DWG, and ability to convert 3D CAD to flat patterns
-
Manual nesting tools that make it easy to drag, drop, bump, and rotate parts on the nest and have the ability to “snap” parts into place against other parts or along the plate edge while maintaining the appropriate nest part spacing
-
Automatic nesting system to reduce programming time from minutes to seconds.
-
True shape nesting strategies, which recognize the actual part geometry and interlock parts together (as opposed to rectangular nesting which places an imaginary rectangular border around each part before nesting and may leave valuable material on the table).
-
Prohibit/permit nesting inside of a part
-
Automatic part interference detection
-
Ability to color code parts according to various part properties for easy identification while nesting or viewing reports
-
Edit lead-in/out position and properties within the nest
-
Control tool path including cut direction and cut sequencing on part-by-part basis
-
Animated cutting sequence simulation
-
Ideally, jobs may also contain parts with different material types, thicknesses, and sheet sizes, and the software will automatically create separate jobs
-
In addition, some applications can account for not only the available parts, but also look at the different plate sizes to determine which combination of parts and plates yields the highest utilization. In ProNest this feature is known as “Nesting System Optimization”.
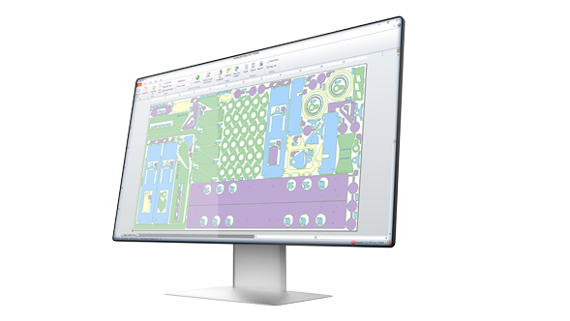
About ProNest nesting software
Brought to you by the cutting experts at Hypertherm Associates, ProNest is one of the world's leading CAD/CAM nesting software solutions having served ens of thousands of customers since 1984.
The ProNest product family supports plasma, waterjet, laser, and oxyfuel cutting machines, as well as other machine applications including bevel cutting, tube and pipe cutting, combination punch, plate machine, and more.
How to get the best nesting results
We’ve already touched on the main benefits of nesting software, but what are some tips and tricks that nesting programmers can use to get the most out of their nesting process?
-
Choose professional grade nesting software
Some CNC machines for cutting automation come equipped with basic nesting functionality and if you have a small cutting operation, doing one off parts, or very small runs, then perhaps you haven’t had a need for a dedicated nesting software thus far in your business. But as your business grows, this entry level software could be holding you back. If your software lacks automatic nesting, true shape nesting, and other advanced features, you could be wasting time and material. Consider pairing your CNC with a professional grade, after-market nesting software. -
Use common line cutting if possible
There are other ways besides nesting, to help drive plate utilization. Common line cutting refers to any time that you have two parts sharing the same edge. Often, nesting programmers use common line cutting to reduce the number of pierces and the overall cutting distance, which maximizes cutting machine consumable life, but this also eliminates the separation between parts, so it becomes another way to reduce scrap. -
Keep track of plate inventory
Many CAD/CAM nesting software applications provide you with a database to store and track your available plate inventory, including remnants and skeletons. Tracking inventory helps drive material utilization by making sure that all plate options are known to the nesting programmer up front, allowing them to choose the best plate for a job. Many shops run into the problem of remnants piling up on the rack, and programmers not really knowing what’s out there, or having to take time to run down to the shop floor and take measurements. The plate inventory database provides this information up front, allowing you to create your best nest. Often, this means the shop is using up plate remnants more quickly and reducing their holding costs. -
Try to nest multiple jobs at the same time
One way to get better results out of your nesting software is to provide it with more parts to choose from. That's because the nesting engine is running your parts through different strategies and scenarios, and it’s constantly looking for the best overall arrangement of parts, so it’s only natural that by adding a greater variety of part geometries to a single job, you’re generally going to end up with better nests and higher utilization compared to doing those jobs separately. Try combining orders from different customers into a single job. For example, if you take all of your quarter inch material, mild steel, that is due in the next 10 days, and combine it together, you will likely end up with a larger pool of parts, and a greater average utilization across your nests than if you had done the jobs separately. In addition, you’re creating a longer more continuous run which can reduce load and unload time. This is a win-win situation as the time savings from the continuous run might be even more valuable than the utilization rate. -
Use filler parts
After the primary job(s) have been nested, you may still have extra space left on the nest. One way to utilize the remaining plate is by adding commonly cut filler parts, or stock parts that could be cut now and placed into inventory for later use. These are common manufacturing processes in the industry, but there are different ways to go about it, some fabricators stock up on parts that they know they’re going to get frequent orders for, others have received huge orders for small parts, which they then try to fit on other jobs, knocking out one batch at a time.