Wind energy manufacturing
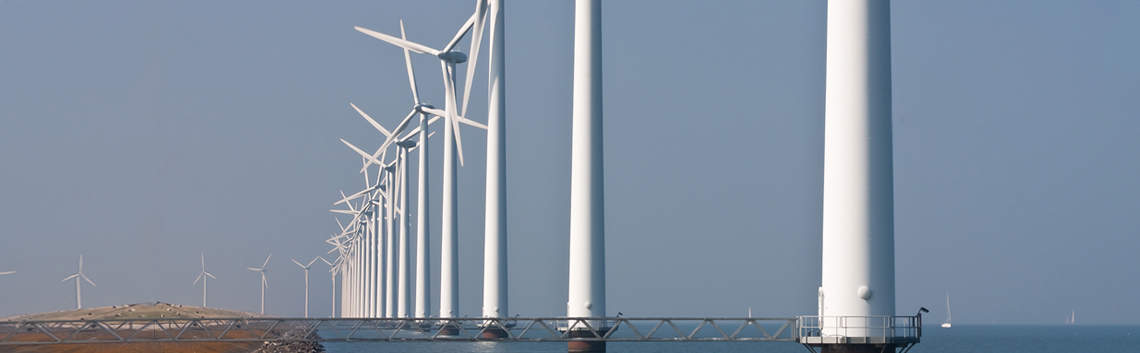
The race to lower carbon emissions has led to enormous demand for wind energy, putting manufacturers in a tough spot as they work to secure raw materials, find skilled workers, and maintain profitability while contending with supply chain challenges and rising costs for both material and labor. This work is made even more difficult by developers who desire ever taller, thicker, and robust towers. The manufacture of a wind tower base alone is complex with many steps including cutting, bending, welding, and finishing.
Smarter solutions to solve common pain points
Hypertherm solutions address the major pain points wind tower and base manufacturers are facing today—rising costs, skilled labor, and demand for thicker, taller structures—by tackling the challenges manufacturers face during cutting and weld preparation.
Challenges include:
-
Poor cut quality with dross and excessive angularity.
-
Inaccurate and inconsistent beveled edges.
-
Material distortion from too much heat input.
The time needed to correct the above issues presents its own problems by:
-
Disrupting the process flow, slowing down production and creating downstream bottlenecks. Instead of welding parts, valuable manpower is spent fixing cut parts.
-
Creating safety and environmental risks in the form of noise, dust, vibration, and injury caused by grinding and the use of highly flammable gasses.
Hypertherm plasma products like our XPR® plasma systems with X-Definition® technology deliver improved cut quality with little dross or angularity. This eliminates time-consuming rework and the need for secondary operations. In addition, the systems provide faster cut speeds so manufacturers can complete their work more quickly. This also results in a smaller heat affected zone so less time is spent fixing distorted material.
Software like ProNest® and Rotary Tube Pro™ with embedded technologies helps wind energy manufacturers cut accurate and consistent beveled edges during the initial cutting process. It reduces the need for operator expertise and intervention, eliminates a manufacturing process step and frees up valuable labor. Exclusive Hypertherm technology can also maximize the number of parts wind energy manufacturers can fit on a plate though the use of shorter leads and moving pierces.
Explore wind energy solutions
Bevel cutting
Bevel cutting is cutting a part with an edge not perpendicular to the top of the piece. It is typically used to prepare plates or pipes for welding. Bevels can be cut at different angles and configurations, resulting in varying edge profiles.
Flush cutting
FlushCut® consumables for Powermax® systems allow easy removal of protrusions, welded attachments, bolts, and fixtures from metal surfaces without cutting into the base material.
Gouging
Plasma gouging – removing metal using a plasma arc – is similar to plasma cutting. A plasma arc between the torch and the workpiece melts the metal, and a gas jet blows away the molten material.
Skeleton cutting
Cutting up and removing the remnants of a metal plate ("skeleton") after mechanized cutting is typically slow and labor-intensive, with many safety risks. Skeleton cutting with plasma is faster, safer, and can be easily integrated into automated cutting operations.
CAM programming
CAM software helps drive the manufacturing process. CAD/CAM nesting software is typically used for programming mechanized flat plate cutting, offering fabricators and manufacturers a single software solution for all of their profile cutting needs. This combination solution provides all of the necessary functionality to complete the job, from CAD concept, to part preparation, to nesting, to numeric code output.
CNC programming
With built in cutting expertise, Hypertherm’s Computer Numeric Control solutions provide consistent product performance with our easy to learn and use Phoenix® software so operators make the optimal cut, every time.
Robot programming
Offline programming solutions to maximize robot productivity on high-mix, low-volume production runs. Reduce programming time, easily program parts of varying complexities, and eliminate the robot downtime associated with manual or teach pendant programming.