Daeyoung Sus Tech finds improved work speed and product quality
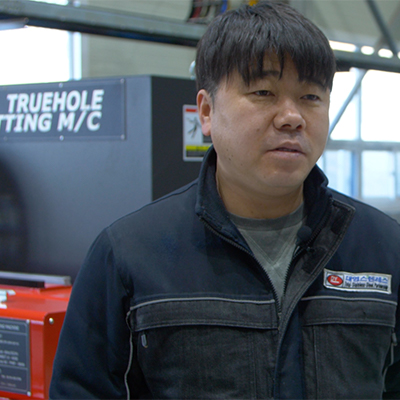
— Business impact —
-
Significant increase in cut speed, quality, and thickness capability
-
Cutting system was easy to use and led to fast implementation
-
Reliable cut performance led to minimal down time
Company: Daeyoung Sus Tech
Daeyoung Sus Tech (formerly known as Cheolwon Stainless) is a metal fabrication company based in Gyeonggi-do, South Korea. Since beginning operations in 2001, Daeyoung Sus Tech has focused mainly on stainless steel cutting. The company cuts stainless steel flanges and frames and supplies them to semiconductor manufacturers and construction companies. Daeyoung Sus Tech’s cutting capacity for stainless steel materials ranges from 6 mm to 100 mm.
Challenge: Company needs new cutting solution to enhance production capabilities
In 2018, Daeyoung Sus Tech began the process of setting up a new factory building to consolidate facilities and expand operations. The new factory was almost four times larger than its previous facilities. The Daeyoung Sus Tech management team wanted to update their equipment and find a solution to enhance their production capabilities. For Daeyoung Sus Tech, both cutting quality and speed were important.
At the time, the company was using a local plasma system for its cutting needs, but this system took over 12 hours to fulfill an order, proving to be inefficient. The Daeyoung Sus Tech team embarked on a hunt for a cutting system that would reduce cutting time and empower them to meet future production needs.
Solution: Hypertherm XPR300 improves work speed and quality
After an extensive search, the team at Daeyoung Sus Tech decided that Hypertherm’s XPR300® plasma cutting system with X-Definition® technology would fulfill their rigorous requirements for improved work speed and cut quality.
“We were focused on finding a solution that would help us improve work speed and cut quality. After meeting with the Hypertherm customer service team, we were very impressed by both the X-Definition technology and their service, so we made the XPR300 our preferred choice.” – Mr. Cho Woo Je, General Manager, Daeyoung Sus Tech
The XPR300
The XPR300 represents a significant advancement in mechanized plasma cutting technology, redefining what plasma can do by expanding its capabilities and opportunities in ways never before possible. With unmatched cut quality on mild steel, stainless steel, and aluminum, the XPR300 increases cut speed, dramatically improves productivity, and reduces operating costs.
Ease-of-use features and system optimizations make the XPR300 easy to run with minimal operator intervention, lowering labor requirements while ensuring optimal performance and unmatched reliability. The system is designed with fewer consoles and easy connections, so operators spend less time setting up and more time cutting. The XPR system’s intuitive operation and automatic system monitoring redefine what simple and user-friendly plasma cutting means.
Ease-of-use features include:
-
EasyConnect™ torch lead and one hand torch-to-receptacle connection enable fast and easy change-outs.
-
QuickLock™ electrode delivers easy consumable replacement.
-
Full control of all functions and settings is available via the CNC.
-
Wi-Fi in the power supply enables multiple system monitoring and service from mobile devices.
-
Arc response technology™ provides automatic torch and ramp-down error protection, eliminating the impact of ramp down errors and reducing the impact of catastrophic electrode blowouts which can damage the torch – significantly extending the life of consumables.
-
Sensors in the power supply deliver refined diagnostic codes and significantly enhanced system monitoring information, reducing troubleshooting time and delivering proactive data to improve overall system optimization and uptime.
X-Definition plasma cutting
Hypertherm’s X-Definition™ plasma introduces a wide range of new process technologies to optimize results on different thicknesses of stainless steel and aluminum. X-Definition plasma produces plasma cut stainless steel parts with smooth, sharp edges that require minimal or no rework at all, a neutral and shiny surface finish, and very little to no dross. From thinner to thicker mild steel cuts, X-Definition plasma delivers a buttery smooth surface finish and a sharp top edge with excellent perpendicularity and hole quality. Fine feature capability is very good, particularly on thinner mild steel.
ISO measures a cut edge’s deviation from perpendicular and encompasses 5 ranges, with 1 having the smallest deviation and 5 having the greatest deviation from perpendicular. On mild steel, conventional plasma is primarily an ISO range 4 and 5 cutting technology and high-definition plasma is primarily a range 3 and 4 cutting technology. However, X-Definition plasma is primarily an ISO range 2 and 3 cutting technology, and it holds onto those ranges for much of its enhanced consumable life.
Business Impact: Significant increase in cut speed, quality, and thickness capability
For Daeyoung Sus Tech, a company that works with stainless steel materials that range from 6 mm to 100 mm (.25 to 4 inches) in thickness, finding a solution that addresses its varied cutting needs while enjoying excellent cut quality was a dream fulfilled.
New features on the XPR300 system also made things easier for operators. Users have full control of functions and settings via the CNC, which provides automatic monitoring. This made it easy for the team to get accustomed to the XPR300 system quickly and launch their production processes.
“It was very convenient for our workers, that after an initial setup, they can automatically start the cutting process by simply pressing the start button.” – Mr. Shin Hui Seong, Senior Manager for Operations, Daeyoung Sus Tech
The company’s work speed and product quality have improved significantly compared to using the old plasma system. With the XPR300, the order that used to take Daeyoung Sus Tech’s previous plasma system 12 hours to complete is finished within 7 – 8 hours, reducing production time by more than 30 percent.
Our efficiency and product quality have improved significantly.
Mr. Cho Woo Je, General Manager
Daeyoung Sus Tech
Just a few months after the investment was made, Daeyoung Sus Tech clearly noticed the benefits of the new addition to the production floor and was enjoying the many improvements the XPR300 brought it compared to its earlier system. The XPR300 delivered a significant increase in cut speed, cut quality, and thickness capabilities.
“I am satisfied that we've not had any problems using the XPR300, which I'd highly recommend. We're also looking at additional purchases in the future to move forward with our expansion plans.” – Mr. Cho Woo Je, General Manager, Daeyoung Sus Tech
Learn how the XPR300 can help your business strike the perfect balance between cut quality, cut speed, and cost. Click the button below, fill out the form, and a Hypertherm product expert will contact you.
Contact an expert