Better weld repair using plasma gouging
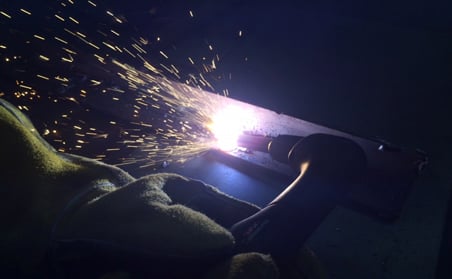
Customer overview
When cracking occurs in or adjacent to welded joints, a satisfactory repair can be made by welding. It is important that enough of the cracked material is gouged or machined away to allow a full penetration repair weld, with no traces of crack left and no new significant defects introduced.
One Hypertherm customer needs to periodically repair cracks in special materials such as high Cr-Ni steels and pure copper.
Challenge: Carbon arc and grinding deliver poor results
The company was using grinding machines and carbon arc gouging to remove cracks and ensure no traces of cracks or defects remained before welding. Unfortunately, neither of these processes was working for the company. Grinding was too slow and carbon arc gouging was contaminating the base metal.
Grinding
When a weld crack occurs, it is possible to repair the crack by grinding and excavating the area down to sound metal and laying another weld bead. However, grinding to remove the damaged area is an intensely manual operation, making it very slow and expensive.
Carbon arc gouging
Carbon arc gouging can be used to excavate cracks, but it has some challenges. Carbon arc gouging can be difficult for operators. It takes skill to create consistent gouges and requires extensive training. Because of high currents (up to 2000A) and high air pressures (80 to 100 psi), carbon arc gouging can be very noisy, requiring ear protection. The air jet causes the molten metal to be ejected over a significant distance, so extra care must be taken to keep workers safe from molten metal.
Carbon arc gouging also creates hazardous fumes. The force of the air blast tends to vaporize much of the molten metal into fine droplets, creating fumes consisting of metal vapor, carbon dust, and metallic byproducts.
Most electrodes used in carbon arc gouging are made from a mixture of graphite and pure carbon. As the electrode is consumed, it releases carbon into the base material. This carbon must be removed before welding, requiring the entire gouge to be grinded or sanded before welding. This secondary work is labor intensive, increasing both the costs and time required to finish the job.
Solution: Powermax HyAccess gouging consumables increase efficiency
The company switched from grinding and carbon arc gouging to plasma gouging using a Hypertherm Powermax® plasma system with HyAccess™ gouging consumables to enable a very delicate gouging process that does not leave any carbide formation on the base metal.
Plasma gouging
Plasma gouging is generally four times faster than carbon arc gouging and creates cleaner, more consistent gouge profiles that need little to no secondary work.
Plasma gouging is easier to learn, requiring less training, so new hires are productive faster and the company saves on training costs. The work environment is also safer. The plasma gas pushes the molten metal out of the groove less violently than carbon arc gouging air jets. Arc spatter is reduced and less molten metal vaporizes, reducing the metallic vapor and reaction with the surrounding atmosphere and generating fewer toxic fumes. Plasma gouging is also 5 to 10 decibels quieter than carbon arc gouging.
Powermax plasma systems
Powermax is the world’s most versatile family of portable plasma cutters, delivering maximum and unmatched reliability. With the industry’s most extensive handheld and automated cutting, marking, and gouging capabilities, Powermax users can confidently tackle any job with superior cut quality and minimized secondary operations.
Powermax has seven portable, professional-grade plasma systems that deliver the best combination of reliability, cut quality, and ease of use. They are designed for maximum productivity at a lower total cost of ownership and are easy to use, requiring very little training, so new operators can perform like professionals in minutes.
HyAccess consumables
Hypertherm’s HyAccess extended reach consumables give operators extra reach when plasma cutting or gouging in hard-to-access or confined spaces. HyAccess consumables extend approximately 76 mm (3 inches) longer than standard consumables and have a very narrow tip, providing better visibility and accessibility.
HyAccess consumables allow operators to cut and gouge in places where they used to have to pull out several tools, like a grinding wheel or oxyfuel torch. They are ideal for cutting interior spaces and hard-to-reach places, such as cutting corners and channels, cutting close edges, and cutting through flanges. The very narrow tip hugs tight curves of even the most complex templates, enabling operators to achieve a closer cut in more difficult-to-reach places – reducing secondary operations and increasing productivity.
Extended reach cutting and gouging is needed for cutting channels or beams with deep groves, cutting or gouging inside an engine compartment or a wheel well, and gouging welds in oddly shaped pieces.
HyAccess consumables also keep workers' hands and the torch away from the heat, increasing worker safety.
Business impact: Faster repair times without contamination
The company can now complete the weld repairs faster and with greater precision. Gouging with plasma – instead of carbon arc gouging – eliminates metal contamination as well.
Learn how Powermax plasma gouging with HyAccess consumables can help you improve gouge quality, increase worker safety, and reduce or eliminate secondary operations. Click the button below, fill out the form, and a Hypertherm product expert will contact you.