Manufacturer gains productivity and quality with SureCut
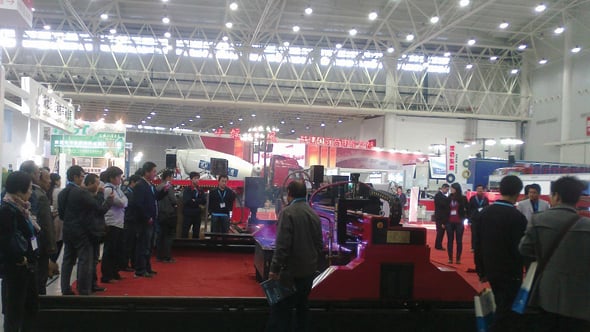
Company overview
Shandong ENxin Special Vehicle Manufacturing Co., Ltd. is a special-purpose vehicle manufacturer located in Jining City, Northern China. The company’s products include concrete mixers, dump trucks, semi-trailers, bulk powder goods tankers, and other special-purpose vehicles. These vehicles are sold in over 20 provinces, cities, and autonomous regions across China, and some vehicle components are exported to other countries.
Challenge: The company needed to boost productivity to become more competitive
Shandong ENxin was looking for ways to increase productivity to be more competitive and grow its specialty vehicle manufacturing business. This included an in-depth review of their current automated cutting machine capabilities, as well as a review of secondary operations, such as the preparation of bolt holes and slots.
Solution: SureCut technology increases productivity and part quality
To learn about the latest industry developments, ENxin contacted a local automated machinery manufacturing company, Shandong Shuipo, that specializes in special-purpose welding and cutting equipment used by the vehicle, engineering machinery, and structural steel industries.
The ENxin team learned how SureCut™ systems with CAM software, CNC, THC, and power supply deliver superior performance, including optimized productivity and part quality. They were especially interested in Rapid Part™ and True Hole® technologies from Hypertherm. These technologies can deliver up to twice the number of parts per hour from the machine, including bolt-ready holes and slots using Hypertherm HyPerformance® plasma technology.
After viewing a cutting demonstration of the ShuiPo plasma cutting machine with SureCut technology, and seeing the impressive capabilities of ProNest® CAM nesting software with the new machine, ENxin decided to make the investment.
HyPerformance plasma technology
HyPerformance plasma systems deliver superior productivity in X-Y, bevel, and robotic cutting and marking applications on metal ranging up to 160 mm (6 ¼ inches) thick. The combination of faster cutting speeds, rapid process cycling, quick changeovers, and high reliability boosts throughput while dramatically lowering operating costs.
Designed and built for maximum performance and productivity in mechanized cutting operations, the versatile HyPerformance plasma systems deliver the ultimate in HyPerformance mild steel cutting, plus aluminum capability and unmatched stainless steel cut quality. They are the best-suited plasma systems for cutting thick materials, including mild steel, stainless steel, and aluminum.
SureCut technology
SureCut technology uses software to automatically embed advanced cutting capabilities into the plasma cutting process, delivering improved outcomes, simplifying cutting operations, and reducing operator intervention. SureCut technologies are designed to maximize cutting performance by applying optimized cutting process parameters, increasing efficiency and positively impacting the bottom line.
SureCut technologies include:
-
Rapid Part technology increases the number of parts produced per hour by automatically reducing cut-to-cut cycle time between parts.
-
True Hole technology applies process expertise to automatically deliver bolt-ready holes.
-
True Bevel™ technology automatically applies the correct bevel angle and reduces operator trial and error.
-
PlateSaver™ technology combines XPR® arc stability and specialized software parameters to dramatically increase material utilization.
Rapid Part technology
More than half of production time is often spent moving between cuts — time that could be used to cut faster and increase productivity. Rapid Part uses hardware and software features to reduce cycle time, enabling up to a 100% increase in parts cut per hour. It also provides more efficient motion during the cutting process, skipping unnecessary steps and reducing production time by up to 50%.
Rapid Part optimizes three critical aspects of the cutting process and executes them automatically through the CNC.
-
The CAM software optimizes the cut path, minimizing the distance traveled from one cut to the next. It also avoids potential collisions, such as part tip-ups that would otherwise require a time-consuming full head raise (Z-axis) motion to traverse safely.
-
In cases where the torch head must be raised fully, the torch height control features rapid Z-axis/vertical motion capability, including automatic fast-to-slow speed crossover calibration.
-
At the beginning of the initial height sensing or machine motion, Hypertherm HPRXD plasma system gas consoles have gas pre-flow functionality, saving valuable time on each pierce.
True Hole technology
True Hole technology produces significantly better hole quality than what has been previously possible using plasma. True Hole is automatically applied by the nesting software or CNC software to thicknesses up to 25 mm (one inch). Diameter and hole coverage range from hole diameter to thickness ratios from 2:1 to as low as 1:1.
True Hole virtually eliminates hole taper, delivering true bolt-hole quality automatically, without operator intervention. Ding is reduced and biased to the outside of the hole. True Hole reduces the need for secondary processes and completes jobs in fewer steps, narrowing the gap with laser hole quality and making the plasma process suitable for many jobs previously cut with laser.
ProNest nesting software
ProNest is an industry-leading CAD/CAM part nesting software designed for advanced mechanized cutting. It offers the highest level of cutting expertise and provides a single solution for all profile cutting needs – including plasma, laser, waterjet, and oxyfuel. ProNest’s powerful, high-yield nesting is designed to supercharge cutting operations, enabling fabricators and manufacturers to increase material utilization, boost productivity, lower operating costs, and improve part quality.
ProNest’s intuitive screens and a wide variety of helpful features make it easy to learn and use. Its faster, fully automated interface can reduce programming time from hours to minutes, while specialized cutting techniques can reduce total cut time by up to 50%.
Business impact: SureCut delivers a significant increase in productivity
Since the installation, ENxin has come to appreciate the ease of use, power, and flexibility of its new cutting system – and its ability to impact part quality and productivity.
They have significantly increased productivity due to the plasma cutting system’s faster cut speed and its ability to cut bolt holes and slots on the plasma machine instead of as a secondary operation. Additionally, the operating cost of the integrated plasma cutting system has proven to be very efficient due to optimized gas, power, and consumable life management.
Learn how SureCut technology can help your business increase productivity, improve cut quality, and decrease costs. Click the button below, fill out the form, and a Hypertherm product expert will contact you.