How one manufacturer reduced processing time with robotic plasma
Lead times were cut in half
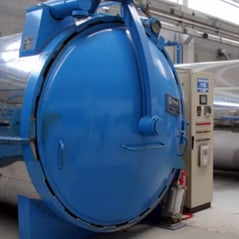
Company overview
The company is a U.S. manufacturer of pharmaceutical pressure tanks. Pharmaceutical pressure tanks are mainly designed for preparing raw materials during drug production. With the stringent sanitary and environmental requirements mandated for pharmaceutical production, pharmaceutical pressure vessels must be manufactured with extreme care. Traditional manufacturing processes for pressure vessel heads generally involve hours of manual marking and cutting followed by hours of grinding.
Challenge: Manufacturing process could not keep up with demand
The company’s manufacturing process could not keep up with high production demands, and the company could not find enough skilled workers to increase capacity. This led to long lead times for its products.
Careful examination of the manufacturing value stream revealed an inefficiency in the cutting process that was negatively impacting many other areas of the operation. The manufacturing process required skilled workers to mark, cut, and grind pressure vessel heads, and manually marking, cutting, and grinding a single vessel head in preparation for welding was taking between four and eight hours.
Creating efficiency became a top priority for the company.
Solution: Robotic plasma cutting reduces marking and cutting time
A robotic plasma cutting solution was introduced to replace manual marking and cutting with automated marking and cutting, thereby reducing the need for filling and grinding.
Robotic plasma cutting
Robotic cutting systems are designed to cut various shapes using powerful and intuitive robot programming software. Traditionally, different handheld machines were needed to saw, mark, cope, drill, punch, and shear complex shapes. However, robotic cutting technology advances have helped dramatically increase productivity by eliminating these manual operations, enabling faster cut speeds, better cut quality, and increased productivity in low-volume runs.
Many industries use robots in varying configurations to perform tasks more efficiently and profitably than by using manual labor. In the past, robots were limited to tasks with very high production quantities, because teaching a robot was a lengthy and expensive process. Recent robotic software programming developments, such as Hypertherm’s Robotmaster® offline programming software, have significantly reduced programming time. Programming that used to take days now takes hours or even minutes, making today's robotic cutting systems incredibly efficient. As a result, robots are more commonly being used for low-volume, high-mix applications.
Typical robot uses include:
-
Cutting for applications such as domes and I-beams
-
Welding in automotive and other industrial applications
-
Machining operations
-
Painting, spray coating, and thermal protection coating of molds
-
Polishing, sanding, and grinding using a variety of tools and techniques
-
Deflashing of plastic molded parts
-
Dispensing of seals and adhesives
Robotmaster offline programming software
Robotmaster CAD/CAM for robots seamlessly integrates off-line programming, simulation, and code generation, delivering quick, error-free robot programs. Robotmaster helps manufacturers use robots to produce higher quality products at a lower cost and allows the user to have full control over process-specific parameters to achieve the desired results.
Robotmaster is designed for process experts, not programming or CAD/CAM experts, so it is easy to use, with intuitive programming workflows. It has streamlined, application-specific user interfaces that allow the process expert to set and manage optimal parameters.
The integration of parameters specific to the user’s process (e.g., welding, cutting, etc.) is simplified with modifiable screens that define the interaction, terminology, and control setting unique to the application. The process parameters can be created, modified, and fully controlled by the user for the entire program, specific operations, or at select points.
Robotmaster provides accurate robot trajectories without teaching points and a click-and-drag interactive simulation and editing environment that enables even new users to correctly program robots.
Supporting a wide range of robot brands, Robotmaster software enables:
-
Higher profitability by reducing programming time while maintaining the robot in production
-
Short production runs for low-volume and high-mix applications
-
Closer conformance to CAD design through optimized travel criteria and trajectories
-
Increased productivity with less robot downtime, since programing is done completely offline and is independent from production
Business impact: Robotic plasma cutting cuts lead times in half
Using robotic plasma cutting, the company reduced marking and cutting time for a low-volume, custom dome from four to eight hours to just 30 minutes. They can now mark and cut 8 to 16 domes in the time they used to spend marking and cutting one dome, significantly increasing productivity.
The automated cutting process also produces perfect, weld-ready cuts, reducing the need for grinding and filling to prepare for welding. The faster process and higher-quality cuts enabled the manufacturer to cut lead times in half, from a full week to just two to three days.
Robotic plasma cutting eliminates common manufacturing pain points, helping companies achieve operational excellence. Replacing manual processes with robotic plasma cutting improves worker safety, since operators are placing materials on a machine and programming it to run, not marking, cutting, and grinding metal using hand tools.
Automation also improves cut quality. By delegating precision-based tasks to machines, the likelihood of mistakes caused by human error is significantly diminished, and Hypertherm’s X-Definition® robotic plasma delivers unmatched cut quality, producing weld-ready parts. This ensures better welds without requiring secondary operations – increasing productivity and avoiding the bottleneck of manual grinding and filling.
In today’s tight labor market for skilled labor, perhaps one of the biggest benefits from switching to robotic plasma cutting is reducing demand for skilled labor. Not only are labor costs high for manual marking, cutting, and clean up, but finding available skilled labor is also a challenge. With robotic plasma cutting, one operator is completing a task in 15 minutes instead of four hours, increasing productivity without requiring additional headcount.
Learn how robotic plasma cutting can help your business strike the perfect balance between cut quality, cut speed, and cost. Click the button below, fill out the form, and a Hypertherm product expert will contact you.