Coal mining machinery manufacturer gains efficiency and lowers costs with robotic plasma beveling
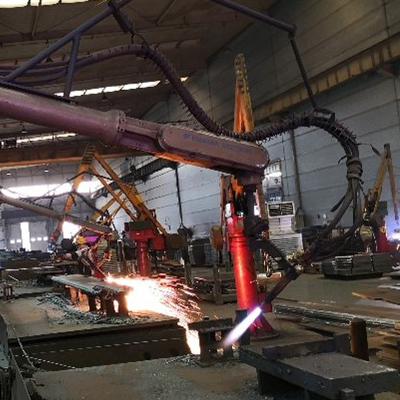
— Business impact —
-
Faster cutting speed, no slagging issues, and minimal post-grinding operations
-
Significantly improved production capacity and reduced cost-per-part
-
Operating 2, 10-hour shifts per day, with an average consumables' usage (electrodes and nozzles) of 5 shifts per set
-The XPR system's intuitive operation and automatic system monitoring redefine what simple and user-friendly plasma cutting means, and it's easily integrated with robots.
Company Overview
A leading manufacturer of coal mining machinery provides a wide range of products to major coal industry groups throughout China. Based in Henan, the company has performed extensive research and development of key projects, leading the direction of China's coal mining equipment.
Challenge: Robot flame beveling process was inefficient
This machine manufacturer set an industry benchmark by replacing manual labor with machines. In their steel plate cutting and profiling workshop, they introduced a fully automated production line from Europe in 2013. At the time, this was the most advanced production line in the world.
Today, the production line remains the main force for material cutting in their factory. Cost reductions and efficiency enhancements are industry trends, and the company was looking for opportunities to upgrade their production system and transform operations.
Their robot flame beveling process was slow, resulting in excessive slag and requiring time-consuming and labor-intensive post-grinding operations. Their production capacity was severely insufficient, and costs were high, leaving significant room for improvement. Thanks to innovations in bevel cutting technology, robotic plasma beveling now provides significant advantages over flame, or oxyfuel, beveling.
Oxyfuel vs. plasma for robotic cutting and gouging
Oxyfuel cutting is a chemical reaction between pure oxygen and steel to form iron oxide. Cutting with oxyfuel requires the use of a highly flammable fuel gas and an open flame to raise the steel’s surface temperature to approximately 962° C (1,800° F). Excessive slag is common due to the high temperature required to reach the chemical reaction. This slag must be grinded off to make parts usable, a time-consuming manual process. Oxyfuel can only cut ferrous metal.
Plasma can cut or gouge any ferrous or non-ferrous metal, including stainless steel, cast iron, aluminum, copper, brass, etc. It is a thermal process that uses heat to cut, so plasma torches begin to cut as soon as they are turned on. Cutting with plasma is cleaner than cutting with oxyfuel, requiring little, if any, post-cutting grinding.
Plasma has many benefits over oxyfuel:
-
Plasma is faster and more efficient. Oxyfuel cutting requires preheating the material. Plasma can complete entire projects by the time oxyfuel mixtures are set and the material is preheated. Overall, cutting with plasma is three to eight times faster than cutting with oxyfuel. It is 12 times faster on thinner materials and twice as fast as an oxyfuel torch when cutting metals up to 25 mm (one inch) in thickness.
-
Plasma produces higher quality cuts, generating less scrap and requiring very little additional rework. Parts cut with oxyfuel can be distorted out of tolerances by the heat, requiring substantial corrections to part geometry. Cutting with oxyfuel also creates slag that must be removed before parts can be used. Long and costly secondary processes such as manual grinding and use of filler materials decrease efficiency and part quality.
-
Plasma is less expensive to use because it is faster and the quality is better. Fuel, labor, electricity, consumables, and other costs are lower simply because cutting with plasma is so much faster.
-
Plasma is safer. Oxyfuel requires a highly flammable fuel – most often acetylene – and oxygen canisters. These flammable materials must be secured and transported following legal guidelines for safe handling. Plasma uses air and electricity, nothing that requires special handling. It also has a much smaller heat zone, exposes operators to less heat, and does not use an open flame.
-
Oxyfuel also requires high insurance premiums due to the risks of storing, handling, and using the fuel. Plasma uses air and electricity, so it does not have the same insurance requirements.
Solution: XPR300 plasma system increases beveling speed
After understanding the customer's needs, a key account manager and application engineer from Hypertherm Associates proposed a solution to transform the robot flame beveling process into robotic plasma beveling and recommended integrating the Hypertherm XPR300® plasma system.
Hypertherm's XPR300
The XPR300 represents a significant advancement in mechanized plasma cutting technology, redefining what plasma can do by expanding its capabilities and opportunities in ways never before possible. With unmatched cut quality on mild steel, stainless steel, and aluminum, the XPR300 increases cut speed, dramatically improves productivity, and slashes operating costs.
Ease-of-use features and system optimizations make the XPR300 easy to run with minimal operator intervention, lowering labor requirements while ensuring optimal performance and unmatched reliability. The system is designed with fewer consoles and easy connections, so operators spend less time setting up and more time cutting. The XPR system’s intuitive operation and automatic system monitoring redefine what simple and user-friendly plasma cutting means.
Ease-of-use features include:
-
EasyConnect™ torch lead and one hand torch-to-receptacle connection enable fast and easy change-outs.
-
QuickLock™ electrode delivers easy consumable replacement.
-
Full control of all functions and settings is available via the CNC.
-
Wi-Fi in the power supply enables multiple system monitoring and service from mobile devices.
-
Arc response technology™ provides automatic torch and ramp-down error protection, eliminating the impact of ramp down errors and reducing the impact of catastrophic electrode blowouts which can damage the torch – significantly extending the life of consumables.
-
Sensors in the power supply deliver refined diagnostic codes and significantly enhanced system monitoring information, reducing troubleshooting time and delivering proactive data to improve overall system optimization and uptime.
Business impact: Faster cutting speeds with minimal post-grinding operations
The coal company successfully transformed beveling operations by switching to plasma bevel cutting and integrating Hypertherm’s XPR300. Using the XPR300, the company has faster cutting speeds, no slagging issues, and minimal post-grinding operations. They have significantly improved production capacity and reduced cost-per-part.
At the same time, the company has increased the life of their consumables. While operating two, 10-hour shifts per day, they are experiencing an average consumable usage – electrodes and nozzles – of five shifts per consumable set.
To learn how your business can strike the perfect balance between cut quality, cut speed, and cost, review the benefits of the XPR plasma cutting systems, or click the button below, fill out the form, and a Hypertherm product expert will contact you.