ProNest cuts production time by 40% for Olympic Steel
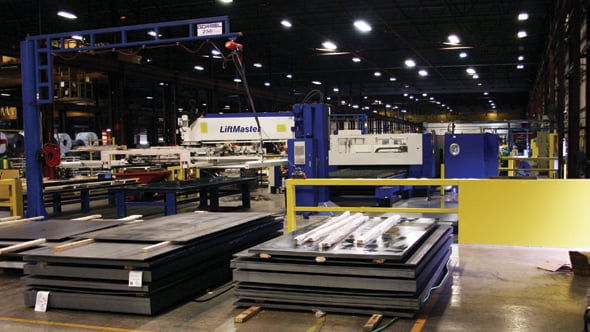
“There are so many ProNest features I really find fantastic and that we use; particularly for our lasers. ProNest’s Collision Avoidance option has been huge for us, especially for use on some of the older lasers where raising and lowering heads is slower. We can now traverse with the cutting head down versus a full retract between every pierce and that has translated to a savings of just over an hour of production time per day, per laser, which is awesome! We now see significantly reduced wear and tear on the laser machines; which reduces our costs.”
Cory DeWitte
CNC Planning Specialist, Olympic Steel
Company overview
Headquartered in Cleveland, Ohio, Olympic Steel is a value-added provider of flat-rolled steel. With over 30 strategically located facilities in North America and a manufacturing footprint of more than 3.7 million square feet, Olympic Steel offers a full portfolio of value-added processing of flat-rolled metals including cut-to-length, temper passed, stretcher leveled, burned-to-shape, formed, machined, welded, painted, and more. A big part of the company’s business is cut-to-shape processing, which is done on more than 30 laser, gas, and plasma cutting machines from a number of different manufacturers.
Challenge: CAM programming using multiple nesting programs was inhibiting productivity
While laser cut-to-shape processing has made a significant contribution to Olympic’s growth and profitability in recent years, the relatively high capital equipment cost of CO2 laser technology requires high levels of productivity to achieve the necessary return on investment. CAM programming plays a leading role in delivering that ROI.
As laser capabilities were added, Olympic soon found itself using numerous OEM and third-party CAM software programs. As a result, CAM programmers had to be trained to operate multiple laser nesting software products, and the company faced mounting software update and maintenance costs each year. A strategic decision was made to seek out and implement a more global corporate approach to CAM programming that would help Olympic Steel achieve its productivity goals.
Solution: ProNest nesting software consolidates CNC sheet and plate cutting
After an exhaustive evaluation period, the company decided on ProNest® for the majority of its CNC sheet and plate-cutting operations nationwide. ProNest enables companies like Olympic Steel to manage a diverse set of cutting machines using one software program.
ProNest nesting software
ProNest is an industry-leading CAD/CAM part nesting software designed for advanced mechanized cutting. It offers the highest level of cutting expertise and provides a single solution for all profile cutting needs – including plasma, laser, waterjet, and oxyfuel. ProNest’s powerful, high-yield nesting is designed to supercharge cutting operations, enabling fabricators and manufacturers to increase material utilization, boost productivity, lower operating costs, and improve part quality.
ProNest’s intuitive screens and a wide variety of helpful features make it easy to learn and use. Its faster, fully automated interface can reduce programming time from hours to minutes, while specialized cutting techniques can reduce total cut time by up to 50%.
ProNest is designed to work with virtually any ERP, MRP, or MES program. These integrations can extend ProNest’s efficiencies more broadly across the organization.
Collision Avoidance
Many machine operators are careful to keep away from tipped-up parts and other obstacles that might collide with the cutting head. Unfortunately, this can mean having the operator watch carefully over the whole process or cutting the entire nest with full head raises. These steps work to prevent collisions, but the process takes a long time to complete due to all the up-and-down motions.
With Collision Avoidance enabled, ProNest automatically adjusts leads, traverse paths, and the cut sequence to avoid possible head crashes right from the start. This allows for safe head-down motion and faster job completion.
-
Leads are repositioned so that the head is always moving away from the previously cut profile. This means the head is no longer in danger of colliding with previously cut parts or cut-outs that have tipped up.
-
Exterior leads are positioned closer to the next part in order to minimize traverse time.
-
The internal cut sequence within a part is optimized to best support collision avoidance and minimize traverse time.
-
Rapid traverse paths between cuts are routed around potential tip-ups, further reducing the chance of crashes.
Common Line Cutting
With Common Line Cutting, adjacent parts share the common edges for cutting. Kerf compensation is applied automatically and can be set as crossing or non-crossing, depending on the cut process used. Safety cuts can also be applied to help avoid potential tip-up situations. In addition, operators can common line dissimilar part profiles across the entire nest, and they can nest parts in common with the plate edge for even greater material utilization. Common Line Cutting also allows users to fully customize the tool path on all parts.
Common Line Cutting increases efficiency. Fewer pierces and reduced cutting distance maximize productivity and consumable life, and eliminating the separation between parts increases material savings and reduces scrap.
Business impact: ProNest saves over one hour of production per laser per day
Olypmic Steel is benefiting from ProNest’s improved nesting capabilities in addition to the substantial benefit of using one program for multiple, diverse cutting systems. The speed enhancements and increased material utilization ProNest has delivered have been significant, a welcome contribution to the bottom line.
Cory DeWitte, CNC Planning Specialist, said, “ProNest now allows me to program eight machines per day, so it has more than doubled our programming productivity. Also, we virtually always achieve a minimum of seventy percent nest utilization, even with the most challenging part geometries.”
ProNest’s Common Line Cutting feature has significantly decreased production time, providing additional productivity gains. DeWitte adds, “ProNest’s Common Line Cutting option has decreased our production time anywhere from twelve to as much as forty percent.”
Collision Avoidance has increased productivity as well, enabling the company to gain an additional hour of production time on each laser machine every day.
Learn how ProNest nesting software can help your business increase material utilization, decrease labor costs, and improve productivity. Click the button below, fill out the form, and a Hypertherm product expert will contact you.