Construction machinery manufacturer decreases robotic plasma beveling costs by 400% with the MAXPRO200®
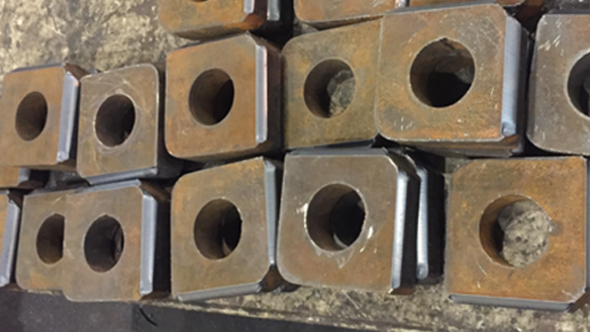
— Business impact —
-
Gained return on investment within one year
-
More than tripled cutting efficiency compared to robotic oxyfuel beveling
-
Superior cutting quality reduced subsequent grinding — improving workers’ productivity and safety conditions
- Realized substantial reduction in overall beveling costs, up to 4 times lower than oxyfuel
Company overview
A well-known private construction machinery manufacturer in Shanghai specializes in designing, developing, and producing fully hydraulic crawler excavators and their spare parts. Their excavator products have high configuration, stable performance, excellent reliability, and high cost-effectiveness. The manufacturer competes with products from renowned global excavator manufacturers and meets the needs of various segmented markets.
Challenge: Inefficient oxyfuel beveling could not meet production requirements
Due to high demand and increasing orders, the company’s robotic oxyfuel beveling process could no longer meet production requirements. Additionally, oxyfuel beveling required a significant amount of subsequent parts processing, leading to high operating costs. The company was also concerned about safety issues related to using oxyfuel cutting.
Plasma cutting vs. oxyfuel for robotic cutting and gouging
Oxyfuel cutting is a chemical reaction between pure oxygen and steel to form iron oxide. Cutting with oxyfuel requires the use of a highly flammable fuel gas and an open flame to raise the steel’s surface temperature to approximately 962° C (1,800° F). Excessive slag is common due to the high temperature required to reach the chemical reaction. This slag must be grinded off to make parts usable, a time-consuming manual process. Oxyfuel can only cut ferrous metal.
Plasma can cut or gouge any ferrous or non-ferrous metal, including stainless steel, cast iron, aluminum, copper, brass, etc. It is a thermal process that uses heat to cut, so plasma torches begin to cut as soon as they are turned on. Cutting with plasma is cleaner than cutting with oxyfuel, requiring little, if any, post-cutting grinding.
Plasma has many benefits over oxyfuel:
-
Plasma is faster and more efficient. Oxyfuel cutting requires preheating the material. Plasma can complete entire projects by the time oxyfuel mixtures are set and the material is preheated. Overall, cutting with plasma is three to eight times faster than cutting with oxyfuel. It is 12 times faster on thinner materials and twice as fast as an oxyfuel torch when cutting metals up to 25 mm (one inch) in thickness.
-
Plasma produces higher quality cuts, generating less scrap and requiring very little additional rework. Parts cut with oxyfuel can be distorted out of tolerances by the heat, requiring substantial corrections to part geometry. Cutting with oxyfuel also creates slag that must be removed before parts can be used. Long and costly secondary processes such as manual grinding and use of filler materials decrease efficiency and part quality.
-
Plasma is less expensive to use because it is faster and the quality is better. Fuel, labor, electricity, consumables, and other costs are lower simply because cutting with plasma is so much faster.
-
Plasma is safer. Oxyfuel requires a highly flammable fuel – most often acetylene – and oxygen canisters. These flammable materials must be secured and transported following legal guidelines for safe handling. Plasma uses air and electricity, nothing that requires special handling. It also has a much smaller heat zone, exposes operators to less heat, and does not use an open flame.
-
Oxyfuel also requires high insurance premiums due to the risks of storing, handling, and using the fuel. Plasma uses air and electricity, so it does not have the same insurance requirements.
Solution: MAXPRO200 increases production efficiency
An application engineer from Hypertherm Associates conducted an in-depth assessment of the customer’s production workshop to understand the challenges and production requirements they were facing. Considering their specific circumstances, the engineer recommended upgrading the robotic oxyfuel beveling process to robotic plasma beveling and integrating Hypertherm Associate’s long-lasting MAXPRO200® plasma system.
The MAXPRO200 offers cutting and piercing speeds that are seven times faster than oxyfuel cutting, significantly improving production efficiency. Plasma cutting provides higher flexibility, allowing for the cutting of almost all metals, including low-carbon steel, stainless steel, and aluminum.
Compared to the highly flammable acetylene gas used in oxyfuel cutting, MAXPRO200 enhances the safety of low-carbon steel cutting.
The MAXPRO200
The MAXPRO200 plasma cutter is engineered for heavy-duty, high-capacity automated and handheld cutting and gouging applications. The system is easy to use and operates with either air, oxygen, or nitrogen plasma gas, combining fast cutting speeds and quick process changes to maximize productivity.
Optimized cutting parameters are automatically set and controlled in one step to deliver consistent results without operator intervention. Advanced diagnostics simplify troubleshooting, enabling faster resolution of any system issues. The MAXPRO200 also offers optional serial communications for full control of the system from the CNC.
Advanced Hypertherm consumable designs improve cut consistency and significantly increase consumable life, decreasing cost-per-part. Patented consumable designs enable best-in-class cut speeds and robust production piercing using lower amperage levels.
The MAXPRO200 has the fastest cut speeds in its class. Its automatic settings, tool free leads, and optional quick disconnect torches let you quickly transition between cutting, gouging, mechanized, and handheld processes. Superior cut quality and consistency minimize the need for costly secondary operations.
Business Impact: MAXPRO200 tripled cutting efficiency, delivered ROI in months
The construction machinery manufacturer fulfilled its objectives for the project, more than tripling bevel cutting efficiency using robotic plasma beveling in place of robotic oxyfuel beveling. The project achieved ROI within a year due to the MAXPRO200’s increased efficiency and better cut quality. The company decreased overall beveling costs up to 400% by switching from oxyfuel beveling to plasma beveling.
At the same time, the MAXPRO200’s superior cutting quality reduced subsequent grinding, improving workers’ productivity. Worker safety conditions also improved.
Learn how your business can strike the perfect balance between cut quality, cut speed, and cost. Review the benefits of the MAXPRO200, or click the button below, fill out the form, and a Hypertherm product expert will contact you.