Konecranes increases efficiency and improves quality with XPR300
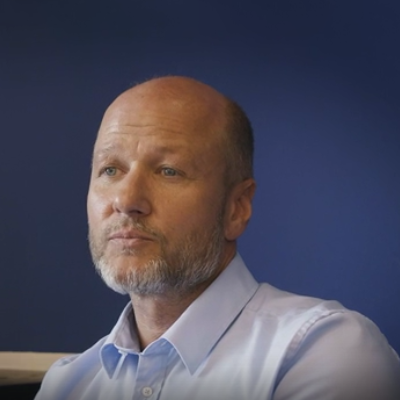
Company overview
Konecranes is a global leader in material handling solutions, serving a broad range of customers across multiple industries with over 16,000 employees worldwide. Konecranes Port Solutions provides equipment, software, and services for the container handling industry.
Konecranes’ Düsseldorf division has approximately 750 employees and manufactures a range of mobile cranes used for handling containers, bulk and general cargoes, and project loads. Customers include port operators, stevedoring ports, and applications for bulk and general cargoes, and they are located in over 100 countries worldwide.
Challenge: Old processes and technology impacted productivity and cut quality
The production area for steel construction, which includes the preparation section where cutting machines are used, had an older cutting machine with an HT2000 power supply that was getting a bit old. The cut quality was no longer up to date.
The company wanted to find a new machine that would replace the old one and increase productivity. The new machine needed to be future-proof and move towards Industry 4.0, ensuring Konecranes could take advantage of advances in technology.
When the Konecranes’ team was exploring how to increase productivity, they looked at their current processes and the distances the materials had to cover. Because their oxyfuel machine was located in a different hall, they were transporting materials over very long distances.
Solution: MicroStep with XPR300 plasma system improves quality and efficiency
In conversations with equipment manufacturers, the Konecranes team realized that a machine from MicroStep with Hypertherm’s XPR300® plasma power supply would fulfill their requirements. With the new system, they could combine many processes, reducing the time spent moving materials between machines.
The XPR300
The XPR300 represents a significant advancement in mechanized plasma cutting technology, redefining what plasma can do by expanding its capabilities and opportunities in ways never before possible. The XPR300 blends new technology with refined processes for next-generation, X-Definition® cutting that delivers unmatched cut quality on mild steel, stainless steel, and aluminum.
The XPR300 also delivers increased cut speed, dramatically improved productivity, and a significant reduction in operating costs. In addition, new ease-of-use features and engineered system optimization make the system easier to run with minimal operator intervention, while also ensuring optimal performance and reliability.
Benefits of the system include:
-
Improved cut quality on thin mild steel, with consistent ISO range 2 results
-
Extended ISO range 3 cut quality results compared with earlier plasma technology
-
Superior stainless steel cut quality across all thickness ranges
-
Superior results on aluminum using Vented Water Injection™ (VWI)
-
Increased cut speeds on thicker materials
-
Thicker piercing capability than with competitive plasma systems
-
Consumable life that is three times longer than consumable life in competitive plasma systems
-
Lower energy costs with 62% higher power-to-weight ratio and 14% faster cuts
The XPR300’s advanced power supply technology delivers highly responsive, rapid system feedback and automatically intervenes to eliminate events that negatively impact system efficiency and consumable life. Arc response technologyTM provides automatic torch and ramp-down error protection to increase the life of the torch and consumables.
Sensors in the power supply deliver refined diagnostic codes and enhanced system monitoring information to reduce troubleshooting time and provide proactive system maintenance data for improved system optimization. These enhancements eliminate the impact of ramp-down errors and increase consumable life to up to three times longer than that of competitive systems. They also reduce the impact of catastrophic electrode blowouts which can damage the torch at high current levels.
Intuitive controls and operation, together with automatic monitoring, make the system easy to use, even for new operators. Training is faster, and seasoned operators deliver better cut quality more efficiently. Full control of all functions and settings is available via the CNC, and automatic system monitoring and specific troubleshooting codes improve maintenance and service. Wi-Fi in the power supply connects to mobile devices and LAN for multiple system monitoring and service.
Both consumable and torch changes are easier as well. The XPR300’s EasyConnect™ torch lead and one hand torch-to-receptacle connection enable fast and easy change-outs, and the system’s QuickLock™ electrode makes consumable replacement easy.
Marking with plasma
Marking metal using plasma is more permanent than marking with soapstone or ink, and the marks are more legible. In addition, the precise nature of marking done during the CNC cutting process is more accurate, with the depth precisely controlled to determine whether marks remain visible or not after coatings are applied.
When fully mechanized systems, like the XPR300, are equipped with both a cutting head and marking hardware, fabricators can consolidate cutting and marking into a single-pass operation for increased productivity.
Drilling
Integrating drilling capability into an X-Y plasma processing machine increases productivity thanks to reduced material handling time and improved part quality. In addition, these integrated machines save on floor space.
Bevel cutting
Robotic plasma bevel cutting improves cut quality and consistency, enabling automated welding processes downstream without the need for secondary grinding steps or excessive fill welding by human operators. The accuracy and reliability of robotic bevel cutting results in superior quality and flexibility with faster lead times, enabling increased efficiency.
Business impact: Updated cutting system combines processes, increasing efficiency and quality
Now that the company has located all of the cutting equipment in one location, they are saving a lot of time. They no longer have to transport materials to different halls for different steps in the cutting process. The Konecranes team explains, “The machines, specifically our oxyfuel machine, were situated in the other hall, which meant we had to transport our materials over long distances. Now that we have combined the new equipment all in one place, we have saved a lot on transportation.”
In addition, the new machine combines many processes that used to require multiple machines, such as marking, drilling, and bevel cutting. With the previous cutting process, these operations were performed at different workstations, which meant the materials were moved from place to place a lot. Doing them all in one workstation provides additional efficiency gains. At the same time, the quality of the workpieces has improved with the updated system.
“The new machine combines many processes, like marking, drilling, and bevel cutting. In the old days, these operations were performed at different work stations, which meant the materials were moved a lot from place to place.”
– Konecranes
Learn how the XPR300 can help your business strike the perfect balance between cut quality, cut speed, and cost. Click the button below, fill out the form, and a Hypertherm product expert will contact you.