Robotic plasma beveling boosts the productivity of a construction machinery manufacturer with the HPR260HD
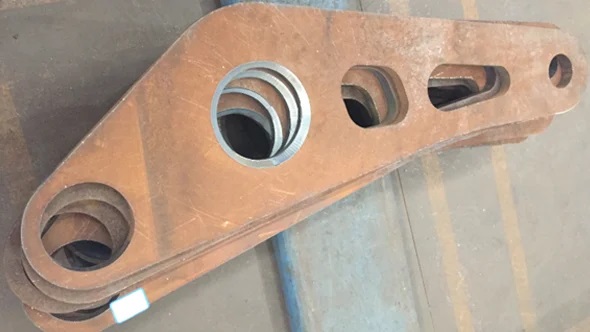
— Business impact —
-
Significantly improved bevel quality
-
More than tripled cutting efficiency compared to robotic oxyfuel beveling
-
Superior cutting quality reduced subsequent grinding — improving workers’ productivity and safety conditions
- Gained substantial reduction in overall beveling costs, up to 4 times lower than oxyfuel
Company overview
A well-known machinery company in Xuzhou, China – renowned as the "Capital of Chinese Construction Machinery” – is dedicated to the sustainable development of the concrete machinery industry. The company also has a subsidiary in Shanghai.
Challenge: Oxyfuel beveling fails production requirements
The machinery company has high-precision requirements for circular beveling and requires minimal thermal deformation (expansion with heat or contraction with cold). They were using robotic oxyfuel beveling, but that process failed to meet their production requirements for bevel quality and efficiency. The subsequent processing workload for beveled parts was substantial, leading to high costs. Safety was also a concern.
Bevel cutting
Bevel cutting is the process of cutting a part with an edge that is not perpendicular to the top of the piece. Bevels can be cut at many different angles and configurations, depending on the purpose, resulting in different edge profiles. The most common use for beveling is in welding preparation, either to increase the welding seam surface or to form an angle between two pieces that will be welded together.
Bevel cutting can increase the structural strength of a component or workpiece. The inclined angle of the cut distributes stress and tension more evenly on the surface of the material, reducing the concentration of stress in weak points. This can help prevent breakage or deformation of the material during use, resulting in cost and production time savings.
Oxyfuel vs. plasma for robotic cutting and gouging
Oxyfuel cutting is a chemical reaction between pure oxygen and steel to form iron oxide. Cutting with oxyfuel requires the use of a highly flammable fuel gas and an open flame to raise the steel’s surface temperature to approximately 962° C (1,800° F). Excessive slag is common due to the high temperature required to reach the chemical reaction. This slag must be grinded off to make parts usable, a time-consuming manual process. Oxyfuel can only cut ferrous metal.
Plasma can cut or gouge any ferrous or non-ferrous metal, including stainless steel, cast iron, aluminum, copper, brass, etc. It is a thermal process that uses heat to cut, so plasma torches begin to cut as soon as they are turned on. Cutting with plasma is cleaner than cutting with oxyfuel, requiring little, if any, post-cutting grinding.
Plasma has many benefits over oxyfuel:
-
Plasma is faster and more efficient. Oxyfuel cutting requires preheating the material. Plasma can complete entire projects by the time oxyfuel mixtures are set and the material is preheated. Overall, cutting with plasma is three to eight times faster than cutting with oxyfuel. It is 12 times faster on thinner materials and twice as fast as an oxyfuel torch when cutting metals up to 25 mm (one inch) in thickness.
-
In a side-by-side cut speed comparison cutting ½ inch steel, an oxyfuel torch cut 20 inches per minute. The plasma system cut 145 inches per minute. During similar testing cutting a 4-by-4 inch square in 3/8 inch thick steel, oxyfuel produced 50 squares per hour. The plasma system produced 700 squares per hour.
-
-
Plasma produces higher quality cuts, generating less scrap and requiring very little additional rework. Parts cut with oxyfuel can be distorted out of tolerances by the heat, requiring substantial corrections to part geometry. Cutting with oxyfuel also creates slag that must be removed before parts can be used. Long and costly secondary processes such as manual grinding and use of filler materials decrease efficiency and part quality.
-
Plasma is less expensive to use because it is faster and the quality is better. Fuel, labor, electricity, consumables, and other costs are lower simply because cutting with plasma is so much faster.
-
Plasma is safer. Oxyfuel requires a highly flammable fuel – most often acetylene – and oxygen canisters. These flammable materials must be secured and transported following legal guidelines for safe handling. Plasma uses air and electricity, nothing that requires special handling. It also has a much smaller heat zone, exposes operators to less heat, and does not use an open flame.
-
Oxyfuel also requires high insurance premiums due to the risks of storing, handling, and using the fuel. Plasma uses air and electricity, so it does not have the same insurance requirements.
Solution: HPR260XD improves bevel quality and increases beveling speed
In response to their challenge and requirements, an application engineer from Hypertherm Associates recommended upgrading to Hypertherm’s HPR260XD high-performance plasma system. The HPRXD high-performance plasma series includes a high-rigidity cutting torch and cable designed specifically for robotic applications. The cable and cutting torch are available in various lengths, so they integrate easily into different robotic applications that are especially suitable for robotic bevel cutting.
The HPRXD series offers numerous advantages: faster cutting speed, shorter process cycles, quick process switching, and reliable and durable performance. By improving cutting capacity, the HPR260XD significantly reduces operating costs.
Note: Hypertherm Associates no longer sells HyPerformance HPR260XD but continues manufacturing original cutting torch replacement parts, consumables, and repair components.
Business impact: HPR260XD improves cut quality and efficiency
The machinery company fulfilled all of their beveling objectives by implementing the HPR260XD and switching to plasma bevel cutting. They significantly improved bevel quality and more than tripled cutting efficiency compared to robotic oxyfuel beveling. The HPR260XD’s superior cutting quality reduced the need for subsequent grinding, improving worker productivity and safety conditions.
The company reduced overall beveling costs by almost 400% by switching from oxyfuel to HPR260XD.
To learn how your business can strike the perfect balance between cut quality, cut speed, and cost, review the benefits of HPR plasma cutting systems, or click the button below, fill out the form, and a Hypertherm product expert will contact you.