Boost your steel fabrication efficiency with ProNest nesting software and Tekla PowerFab ERP solutions
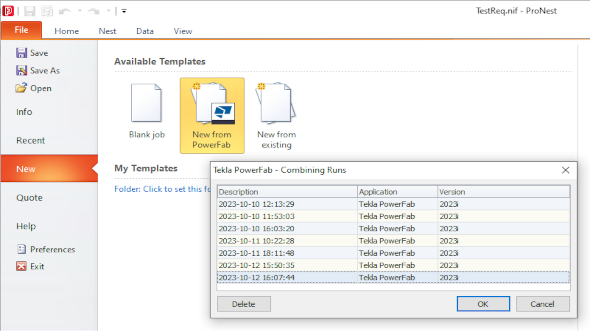
In a competitive world of steel fabrication, achieving operational efficiency and precision is crucial to success. Integrating Tekla® PowerFab® Enterprise Resource Planning (ERP) systems with advanced nesting software like ProNest®, can transform your workflows and elevate your business.
The Tekla PowerFab Connector ensures smooth information flows between Tekla PowerFab API and ProNest software. This synchronization eliminates data duplication and rework, enhances data quality, and promotes information sharing across the organization. In today’s fast-paced manufacturing industry, data connectivity is essential for maximizing profitability and scalability.
Here’s how this ERP integration can benefit your business operations and streamline your manufacturing processes.
Understanding ProNest nesting software
ProNest nesting software is an industry-leading CAD/CAM part nesting software. It’s designed for advanced mechanized cutting processes, including plasma, laser, waterjet, and oxyfuel. ProNest provides powerful, high-yield nesting functionality that helps reduce raw material costs and increase profitability. It supports Hypertherm’s SureCut™ technologies, such as True Hole®, True Bevel™, Rapid Part™, and Plate Saver™, which enhance product quality and cutting efficiency automatically without operator intervention. ProNest can significantly reduce programming time, total cut time, and human errors in your manufacturing operations.
Understanding Tekla PowerFab ERP system
Tekla PowerFab is a comprehensive software suite designed specifically for steel fabricators. It provides a systematic and collaborative approach to managing the entire fabrication process, from estimating jobs to material procurement to inventory management, and shipping finished products. The intuitive dashboards provide real-time visibility into all aspects of the business operation.
Benefits of ProNest and Tekla PowerFab integration
By linking ProNest directly to the Tekla PowerFab API, seamless communication occurs between the two systems. This integration ensures that real-time data flows continuously in both directions, alerting operators to potential workflow disruptions. Business leaders can also make informed decisions on forecasting, inventory management, and production schedules.
Other benefits include:
1. Material cost savings:
-
ProNest: Provides powerful, high-yield nesting that optimizes material usage, reducing waste and lowering material costs.
-
Tekla PowerFab: Tracks material usage and manages remnants efficiently, ensuring accurate inventory levels.
2. Increased productivity:
-
ProNest: Automates the nesting process, reducing programming time from hours to minutes and cutting total cut time by up to 50%.
-
Tekla PowerFab: Schedules and controls production processes, aligning cutting operations with overall production plans.
3. Enhanced integration:
-
ProNest: Imports design files and generates optimized nesting layouts.
-
Tekla PowerFab: Imports nesting data, updates inventory, and provides feedback on actual material usage, creating a seamless workflow from design to production.
4. Ease of use:
-
ProNest: Provides a user-friendly interface with intuitive screens and a variety of helpful features.
-
Tekla PowerFab: Delivers comprehensive ERP functionalities that are easy to navigate and integrate with other systems.
5. Technical support:
-
ProNest: Offers unlimited access to technical support, training, and software updates.
-
Tekla PowerFab: Provides robust support and resources to ensure smooth operation and integration.
How the ERP integration works
Setting up the Tekla PowerFab Connector is straightforward and user-friendly. The direct integration provides real-time data flow between the Tekla PowerFab API and the ProNest server. This means you can easily nest combining runs of parts and plates from PowerFab in ProNest, ensuring optimal material utilization. As nests are created and processed, the results are immediately available in PowerFab, keeping your production data synchronized.
Features to enhance production
-
Plate Sources tab: A new tab in the ProNest Edit Plate List shows available inventory from PowerFab, making it easy to manage your materials.
-
Requisitions: Create requisitions for any orderable plate directly in ProNest, streamlining your ordering process.
-
Import parts: Import parts from a PowerFab Combining Run and add parts from other sources in ProNest as needed.
-
Send nest and remnant information: Send nest and remnant information back to PowerFab for future use, ensuring nothing goes to waste.
-
Web App integration: View and complete nests in the ProNest web app as they are processed, providing flexibility and convenience.
Plate Inventory Management
While Tekla PowerFab typically serves as the primary database for your material inventory, the ProNest Plate Inventory module is still required to save remnants in ProNest and send them to Tekla PowerFab. This adds accuracy and traceability of all raw materials.
By integrating Tekla PowerFab with ProNest, you can significantly enhance your production processes, reduce human errors, and improve overall efficiency. Embrace this powerful combination to stay ahead in the steel fabrication industry and deliver exceptional results.
Which manufacturing operations will benefit the most?
Customers who operate a large-scale steel fabrication and/or manufacturing companies with multi-location facilities will greatly benefit from using ProNest nesting software along with Tekla PowerFab ERP system. It is especially beneficial to customers with high-volume production in structural steel components, custom metal parts, and assemblies for construction, automotive, and heavy machine industries.
Many of these customers experience similar business challenges. These can include:
-
Material waste: High material costs due to inefficient nesting and cutting processes.
-
Production efficiency: Need for faster turnaround times and reduced machine downtime.
-
Inventory management: Difficulty in tracking material usage and managing remnants.
-
System integration: Lack of seamless integration between design, production, and inventory systems.
Example scenario
A large-scale steel fabricator receives a complex order for custom metal parts. Combining runs containing the parts and plates can be sent from Tekla PowerFab to ProNest for nesting. In ProNest, the parts and plates from the combining run will be loaded into our part list and plate list of the job. ProNest then uses its Automatic Nesting function to generate an optimized nesting layout, minimizing material waste. The nesting data is then seamlessly integrated back into Tekla PowerFab ERP software, which updates the inventory, schedules the cutting operations, and tracks material usage. This integration ensures efficient production, accurate inventory management, and significant cost savings.
By leveraging the combined capabilities of ProNest and Tekla PowerFab, this customer can achieve greater automation, efficiency, and profitability in their steel fabrication operations.
Steps to get started
1. Assess your needs:
-
Evaluate current processes: Identify areas where you need improvement, such as material waste, production efficiency, and inventory management.
-
Define goals: Set clear objectives for what you want to achieve with the new systems, like reducing material costs or improving production turnaround times.
2. Research and select software:
-
ProNest: Examine the features and benefits of ProNest. Consider scheduling a demo or trial to see how it fits your needs.
-
Tekla PowerFab: Explore the capabilities of Tekla PowerFab ERP. Check for integration options with your existing systems and how it can streamline your operations.
3. Plan the integration:
-
Consult with experts: Engage with software providers or consultants who can help you plan the integration. They can provide insights into best practices and potential challenges.
-
Develop a timeline: Create a detailed timeline for the implementation process, including training sessions and system testing.
4. Training and implementation:
-
Training: Ensure your team receives comprehensive training on both ProNest and Tekla PowerFab. This will help them understand how to use the software effectively.
-
Pilot testing: Start with a pilot project to test the integration and workflows. This allows you to identify any issues and make necessary adjustments before full-scale implementation.
5. Full deployment:
-
Rollout: Gradually roll out the systems across your operations. Monitor the process closely and provide ongoing support to your team.
-
Feedback loop: Establish a feedback loop to continuously gather input from users and make improvements to the system.
By following these steps, you can ensure a smooth transition to using ProNest and Tekla PowerFab, ultimately enhancing your steel fabrication operations. If you have any specific questions or need further assistance, speak to a Hypertherm expert.