How Powermax SYNC® will change the way you work
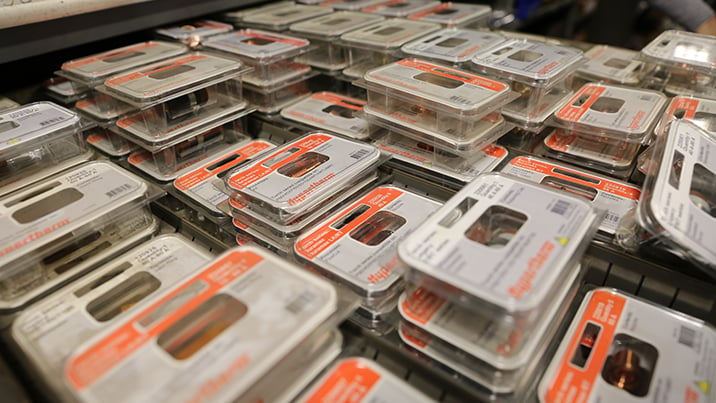
Recently, we discussed how a cartridge-based consumable has many advantages to end users, creating an easier, safer, and more manageable way to replace consumables.
But innovative consumables are only one important element of the new Powermax SYNC® series. When we started thinking about the future of Powermax plasma, we wanted to completely reimagine our systems in a way that would address common customer pain points. In speaking to our customers, three themes emerged:
-
Companies, both large and small, are having a hard time finding workers, let alone skilled workers who know how to cut with plasma.
-
Companies are under intense pressure to reduce costs and increase productivity.
-
Companies need a way to monitor the work that’s happening so they can quickly identify and address problems before they snowball and become expensive to fix.
Hypertherm’s all-new Powermax SYNC® series is designed to address all three of those pain points.
Pain point 1: Skilled workers are impossible to find.
Solution: Create a plasma cutter so easy to use, training is not required.
As we discussed in our previous blog, the Powermax SYNC® is incredibly intuitive and easy to use. Instead of five separate consumable parts, these systems only require one: a single-piece cartridge consumable that takes less than 10 seconds to install. Companies do not need to spend time teaching new employees how to identify the correct consumable parts, assemble them in the correct order, and properly install them on the torch.
Hypertherm’s new single-piece cartridge consumable is color-coded so operators can quickly grab the right cartridge for the job at hand. There are four colors in all: yellow for handheld cutting, gray for mechanized cutting, green for gouging, and black for specialty applications like flush cutting and extended reach cutting.
Another advantage of the cartridge consumable platform is the wear rate. The components of a traditional five-piece stack-up do not wear at the same rate. The electrode and nozzle wear most quickly and the retaining cap the most slowly. This adds complexity and training time since companies need to teach new operators how to inspect and replace worn consumables. Hypertherm’s new cartridge consumable is designed specifically for its components to wear at a consistent rate, further reducing training, waste, and downtime.
In addition, the cartridge is embedded with an RFID chip. This chip communicates with the torch and power supply to ensure the system settings match the cartridge. If you install a 65-amp cutting cartridge, the system will change the amperage to 65 amps, automatically set the air pressure, and go into cutting mode. This not only reduces training, but also eliminates operator errors.
If you’re an operator you don’t need to worry about grabbing the wrong part, putting consumables in the right order, or installing on the torch in the right way. If you’re a business owner, you don’t need to spend a lot of time training new employees—explaining what the consumables are, how to choose the right ones, how to put them in order, and screw them onto the torch correctly.
Pain point 2: Costs are rising faster than productivity.
Solution: Create a more efficient plasma cutter that allows operators to complete more work in less time.
Less time spent training new hires will certainly help to increase productivity, but Powermax SYNC® drives productivity in other ways as well.
For one thing, the cartridge consumable lasts up to twice as long when hand cutting and provides improved cut quality when using a mechanized torch. This means less time spent changing out consumables and reworking parts. And think about how much simpler ordering and inventory management will be now that you only have one part – rather than five – to keep track of.
Manging your conventional plasma consumables can be costly and confusing, resulting in increased inventory costs and operator error.
The automatic set-up process and color-coded cartridge also help to eliminate errors which often lead to poorly cut parts and more rework. By eliminating the possibility of operator error, productivity is already much improved. In short, Powermax SYNC® improves productivity by significantly reducing, if not eliminating, non-value-added work.
Powermax SYNC® also helps in another way – the torch features built-in controls which allow the operator to do things like adjust the amperage and turn the torch on and off without returning to the power supply. This is another example of eliminating non-value-added time. If you are up on a ladder working, for example, or have your system tucked under a workbench, you can save time by making system adjustments right where you are working.
Pain point 3: Problems quickly multiply which wastes money.
Solution: Create a plasma cutter that provides helpful data so operators can catch problems early on.
As mentioned earlier, the Powermax SYNC® cartridge is embedded with an RFID chip. This chip communicates with the torch and power supply to automatically ensure the system settings are correct. This chip has another job though: collection of utilization data.
The Powermax SYNC® system captures information—things like arc-on time, arc transfer rate, air pressure, etc.—as you use it. Cartridge utilization data can be viewed and imported into a dashboard using the special cartridge reader and app, where users can manage, compare, and find insights into any usage patterns or trends. This data can help you spot issues early on before consumable life is impacted. For example, if you know that your arc transfer rate is normally 85 percent and it drops or you notice that you are suddenly getting fewer starts, then you know something is wrong.
We saw this repeatedly during our field trials. For example, we had a customer who noticed that cartridge life was shorter at night. After analyzing the data, we discovered it was because the outside air temperature was lower at night which in turn affected airflow to the system. All this customer had to do was increase their airflow slightly and their cartridge life was back to normal.
This same customer also discovered that some operators were firing the torch without transferring the arc, more than others. It was able to coach those operators and impact consumable life. Before the Powermax SYNC®, these kinds of insights would not be possible.
To recap, Powermax SYNC® can help companies address common pain points through its ease of use, reduction of waste, and smart, data collection. That’s why we are confident that after years of development, this new series and consumable platform will add value and change the way you work.