Why plasma cutting remains a metal industry powerhouse
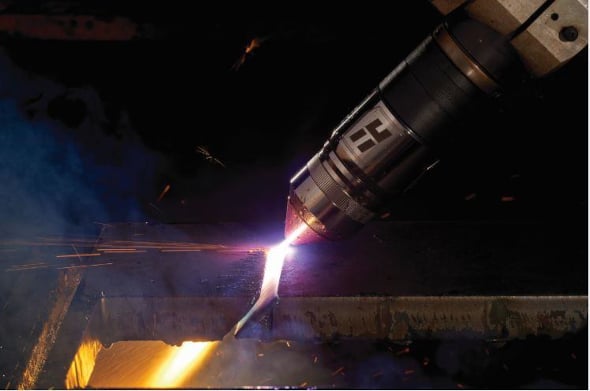
In the ever-evolving realm of metal fabrication and metal-cutting systems, rumors about the end of plasma cutting due to the emergence of laser-cutting technology are becoming increasingly common. While lasers offer some advantages in specific circumstances, plasma cutting technology remains vital for countless applications. This blog post debunks the plasma obsolescence myth and explores where it reigns supreme. We’ll delve into the unique benefits of plasma cutting, compare it to laser cutting, and show its continued relevance across various metalworking industries.
- Cutting thickness: While laser can do wonders on sheet metal, plasma is excellent at cutting thicker metals. Depending on system capability, some industrial plasma cutters can handle materials greater than 50 mm (2 inches) thick, significantly exceeding the capabilities of most commercial lasers. This expanded capacity allows the plasma to handle demanding tasks in heavy industries like shipbuilding. For example, plasma cutting is ideal in bridge construction projects that involve cutting thick steel beams for support structures because it can efficiently handle thicker materials with a high-quality cut.
- Cutting speed: A plasma torch can achieve faster cutting speeds for thicker metals than lasers. This translates into greater productivity and faster project delivery times. The speed advantage of plasma becomes particularly pronounced when dealing with substantial material thicknesses. Imagine a large-scale steel fabrication shop producing heavy equipment components. Here, plasma cutting allows you to cut thick mild steel, stainless steel, or aluminum sheets with strong cut quality faster, leading to quicker completion of projects and increased overall production. In many cases, the cut-edge is smoother with plasma than with laser; this is particularly true with thick metals.
- Material versatility: Although mainly used for conductive metals like steel, aluminum, and stainless steel, plasma cutters can also deal with some metals with the help of water injection techniques. This versatility makes plasma a more adaptable tool in various manufacturing environments. For example, a shop might use a plasma cutter to repair steel car parts and cut complex shapes from stainless steel countertops or aluminum panels used in custom vehicle construction.
- Portability: Many plasma cutters are compact and portable, ideal for on-site manufacturing and repair work. This portability is a significant advantage for tasks such as metalworking on construction sites or emergency repairs in various industries. Imagine a team carrying out pipe repairs in a remote location. Here, a portable plasma cutter can be easily transported and used on-site to cut and repair damaged piping sections precisely.
The enduring allure of plasma cutting
Plasma cutting uses a stream of superheated ionized gas (plasma) to melt and expel the cutting material (cutting path) on the workpiece. This versatile technology has several significant advantages:
Economical: Plasma cutters generally have a lower initial investment and operating cost than lasers. Maintenance is also typically more straightforward and less expensive. Let’s break it down further:
-
Initial investment: A plasma cutter can cost significantly less than a fiber laser cutting machine for comparable cutting capabilities. This lower initial cost makes plasma cutting an attractive option for fabrication shops and companies on tighter budgets. A plasma cutter can provide the necessary metal-cutting capabilities at a price that fits your financial constraints, allowing you to compete effectively without a substantial upfront investment.
-
Operating costs: Consumable parts such as electrodes, nozzles, and cartridges are generally cheaper for plasma cutters than the specialized components required for laser systems. Additionally, plasma cutting typically uses less energy, lowering electricity bills. Over the life of the equipment, these ongoing operating cost savings can add up significantly for companies that rely heavily on metal cutting.
Maintenance costs:
Less expensive: Plasma-cutting machinery generally requires lower maintenance costs than laser-cutting equipment.
Simpler components: Plasma cutters have fewer intricate components, making maintenance straightforward.
Laser cutting: Equipment tends to be more expensive to operate.
Regular maintenance is crucial to ensure precision and longevity.
Different types of lasers (CO2, neodymium, fiber) have varying maintenance requirements.
Training and safety:
Plasma
Operator knowledge:
-
Essential training: Operators must receive comprehensive training to operate plasma cutting machines effectively.
-
Machine setup: Understanding machine setup, calibration, and maintenance is crucial.
-
Consumables handling: Proper handling and replacement of consumables (nozzles, electrodes) are essential for consistent cut quality.
Laser cutting:
-
Understanding laser cutter types and proper system calibration for effective machine operation.
-
Machine operation - laser cutter types: Understanding the differences between CO2, neodymium, and fiber laser systems.
-
System calibration: Properly setting up and operating laser cutting equipment.
Safety measures:
-
Plasma cutting: Focuses on preventing exposure to hazardous gases and intense light.
-
Laser cutting: Emphasizes eye safety due to laser intensity.
When plasma takes center stage: applications where it shines
While both plasma and laser cutting processes have their merits, plasma is the superior choice in many industrial applications.
-
Heavy manufacturing and construction: Plasma is the right choice for thick metal plates, structural steel, and heavy machine components. Its ability to cut substantial materials benefits shipbuilding, bridge construction, and offshore platforms.
-
Automotive and transportation: Plasma's robust nature makes it ideal for cutting automotive structures, chassis, and exhaust components. Whether you're creating a sleek sports car or a rugged truck, plasma ensures precise cuts without breaking a sweat.
-
Aerospace and aviation: Aircraft manufacturers rely on plasma to carve complex shapes from aluminum, titanium, and stainless steel. From wing components to engine parts, the speed and precision of plasma keep the aerospace industry on the rise.
-
Metal art and sculpture: Artists use plasma cutting machines to create stunning sculptures, intricate designs, and decorative pieces. Working with various metals—be it carbon steel, copper, or bronze—allows for limitless creativity.
-
Shipbuilding and marine Industry: Shipyards use plasma to cut hulls, bulkheads, and other critical ship components. Its ability to handle thick materials and maintain precision even in challenging environments makes it a reliable companion for shipbuilders.
-
Industrial machinery and equipment: Plasma performs heavy-duty tasks from factories to mining operations. Think conveyor belts, hydraulic systems, and industrial machines – all shaped by the fiery torrent of plasma.
-
Repair and maintenance: Plasma steps in when existing structures need modification or repair. It's like a metal surgeon, removing damaged sections and replacing them perfectly. Boiler repairs, piping maintenance, and equipment refurbishment are all under its purview.
These two thermal processes, harnessed by CNC machines, slice through materials with surgical precision. Let’s dissect their differences and uncover the sparks that fly in this high-stakes showdown.
Quick facts: plasma and laser technology
Plasma cutting:
-
Electric arc: Plasma cutters generate a directed flow of superheated plasma.
-
Conductive materials: Plasma’s forte lies in cutting conductive materials.
-
Dross and edge quality: Expect some dross (residue) and a rougher edge finish.
-
CNC machines: Plasma cutters play well with CNC machines.
-
Compressed air: Plasma cutters leverage the power of compressed air to make precision cuts through various metals.
-
Cutting head: A plasma torch is a high-temperature cutting tool that uses ionized gas (plasma) to swiftly slice through metal, making it a versatile choice for industrial applications and metal fabrication.
-
Heat-affected zone: A tad wider than laser cuts but manageable.
-
Automation: Plasma cutting automation streamlines production, enhances precision, and ensures safety in metal fabrication processes.
-
High speed: Thrives in the 30-50mm thickness range.
Laser cutting:
-
Laser beam: A focused, intense ray of light dances across the material, melting and vaporizing it.
-
CO2 lasers: These kilowatt-level lasers are workhorses, cutting through various materials like a hot knife through butter.
-
Edge quality: Laser cuts boast impeccable precision and surface finish.
-
Heat-affected zone: Minimal heat impact on surrounding material.
-
Automation: Laser systems integrate seamlessly into automated production lines.
-
Types of lasers: CO2, neodymium, and fiber lasers have their niche.
-
Solid state lasers: Neodymium and fiber lasers rule the roost.
-
High speed: Rapid cuts, intricate shapes, and minimal kerf (material loss).
-
Materials: Laser handles everything, from metals to non-metals, including ceramics. However, they can struggle with reflective materials.
-
Waterjet cutting: Laser’s aquatic cousin, waterjet, uses water and abrasives for precision cuts.
The verdict?
Plasma is not obsolete; it’s just warming up. While laser cutters dazzle with high precision on thin metals, plasma roars with brute force, cost-effectiveness, and efficiency. If you’re considering switching from plasma, remember that plasma cutting is the unsung hero of thick metal cuts.
In the end, both cutting methods have their place. Whether you're creating delicate jewelry using thin materials or erecting steel skyscrapers, choose wisely.