Plasma cutting aluminum – what you need to know
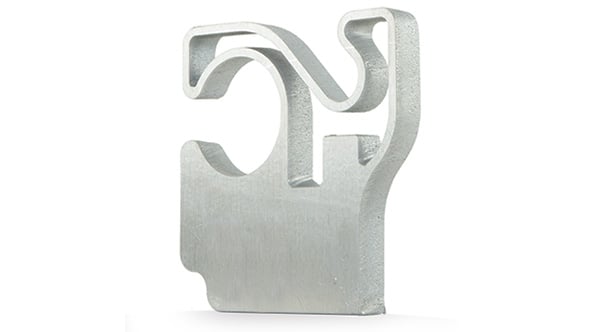
Can you cut aluminum with a plasma cutter?
There are many misconceptions when it comes to this topic, however the bottom line is yes, a plasma cutter will cut aluminum. In fact, today’s plasma systems, especially Hypertherm’s newest X-Definition™ class plasma, are one of the best ways to cut aluminum. Though some people think laser is a better and more cost-effective method of cutting aluminum, the reality is quite the opposite. The reflective, soft, and thermally conductive nature of this metal makes the use of both fiber and CO2 lasers challenging and expensive. When using laser, cutting speeds are often slower and operating costs higher because of the volume of gas needed.
In this article, we’ll explore more of these misconceptions. In addition, we’ll also cover gas selection when plasma cutting aluminum, and discuss another common concern when working with aluminum, underwater cutting.
What kind of cut quality should I expect when plasma cutting aluminum?
Some people believe it is not a good idea to cut aluminum with plasma systems because its melting point is too low, making it difficult to get a nice, clean edge. While it is true that the melting point of aluminum is lower than most other metals, if you choose the correct gases and follow the parameters in your owner’s manual, you can get a very nice edge with tight tolerances (i.e., little angle variation) on both thick and thin aluminum. In addition, you should see very little dross.
.
How can I achieve the best cut quality on aluminum?
No matter what material or thickness you’re cutting, our advice is always the same: Use the settings in the owner’s manual that came with your system. All of our manuals contain very detailed cut charts, including plasma cut charts for aluminum. Always start with the settings found in those charts. You can always make slight adjustments later if needed.
Can you plasma cut aluminum with a water table?
You should never plasma cut aluminum under water when using an H-35 or H-2 gas mixture.
However, you can cut underwater when using the other mixtures mentioned in this article, provided you can prevent the accumulation of hydrogen gas. This is very important, so please read on as we explain why this is needed and how..
People who own or operate a CNC plasma table know that there are two ways of controlling fumes. You can either use a downdraft fume extraction system or a water table. Of these two options, water tables are often preferred, as the water helps to absorb the sound, extra dust, and ultraviolet light created during the aluminum cutting process. You need to be careful however, as the combination of aluminum and water have the potential to create an explosion. During cutting, small particles of aluminum and aluminum oxide form. These particles cool as they hit the water and then sink to the bottom of your water table. Once at the bottom, the aluminum oxide absorbs the oxygen in the water, leaving only hydrogen behind, since water is composed of hydrogen and oxygen. Much of this hydrogen will rise to the surface as little bubbles before popping and dispersing into the air. These bubbles aren’t the problem. The problem is the bubbles that do not rise and disperse into the air. Some CNC plasma tables are designed in a way that can trap these hydrogen bubbles, causing them to sit and multiply at the bottom of the table for days or weeks. Over time, a relatively large bubble of hydrogen could form, potentially resulting in an explosion.
To avoid a scenario like this, you want to work with companies who have experience designing water tables specifically for plasma cutting aluminum. These companies have a number of ways of preventing a build-up of hydrogen.
Can you plasma cut aluminum using a water shield if you don’t have a water table?
Since we are on the subject of water tables, let’s address another question we often get, can you use water as your shield gas if you have a downdraft table instead of a water table. The short answer is yes. You do not necessarily need a water table to use water as your shield gas. This is because the amount of water used is relatively low and mostly evaporates when cutting thicker materials. Although most of the water will evaporate, a little bit of moisture could still reach your cutting table. For this reason, we highly recommend contacting your table manufacturer first, before introducing water as your shield, as they may recommend the use of different filters designed to handle extra moisture.
What type of gas should I use when cutting aluminum?
The type of gas you use will depend on the type of plasma cutter you have. Before we explain which gas to use, let’s start with a quick overview of the different gases most often used when plasma cutting.
Plasma cutting gas types explained
You actually need two gases: a plasma gas – the gas that actually does the cutting – and a shield or secondary gas. The shield gas is the gas that swirls around your torch and consumables to keep everything from overheating. The most popular plasma gases in use today are:
- Air
- Nitrogen
- Oxygen
- H-35, a mixture of 35 percent hydrogen and 65 percent argon
- F5, a mixture of 5 percent hydrogen and 95 percent nitrogen
In addition, Hypertherm’s X-Definition class systems, our XPR170™ and XPR300™, can use a gas mixture called H-2. H-2 is a combination of hydrogen, argon, and nitrogen, mixed at different percentages depending on the thickness you are cutting and the desired cut quality outcome.
For your shield gas, you can use air or nitrogen or one of two additional gases not listed above, water and carbon dioxide.
Gas selection when using air plasma to cut aluminum
If you have an air plasma cutter like a Powermax®, you’ll need to use air as both your plasma gas and your shield gas. Fortunately, air is a very versatile plasma gas and will produce good cut quality on aluminum. Air is also the most inexpensive option because you don’t have to buy separate gas canisters. The one drawback to air is that the cut surface can oxidize leaving you with porous welds and the need to rework parts before welding. When cutting aluminum, the surface finish will tend to be rough and require some rework if aesthetics are important to you.
Gas selection when using multi-gas systems
If you have a high-definition or X-Definition plasma system, you can also use air, however, we do not recommend it. You will wind up with a rough and heavily oxidized black surface along with heavy dross.
Instead, we recommend the use of nitrogen for your plasma gas and nitrogen or water for your shield gas. Your choice of gas will depend on four things: the thickness of the aluminum you plan to cut along with your desired cut quality, cut speed, and operating cost.
Aluminum less than 5 mm (0.188″) in thickness
When plasma cutting aluminum less than 5 mm (0.188″) in thickness, you will get the best cut quality if you use nitrogen as both the plasma and shield gas. Air is generally considered a good shield gas option because it provides adequate cut quality and a low operating cost.
To recap, when cutting aluminum less than 5 mm (0.188″) in thickness, we recommend using nitrogen as both your plasma and shield gas, referred to as an N2/N2 process.
Aluminum greater than 6 mm (1/4″) in thickness
When working with aluminum thicker than 6 mm (1/4″), we recommend using nitrogen as your plasma gas and water as your shield gas, so a nitrogen/water process. This combination provides excellent cut quality with a smooth surface finish, very good cut speeds, and the lowest operating cost.
If you need to cut aluminum that is thicker than 12 mm (1/2″), you can alternatively use H-35 or an H-2 mix as your plasma gas and nitrogen as the shield gas. These gases work especially well on material in excess of 20 mm (3/4″) where more energy is required.
You might have noticed that two common plasma gases – oxygen and F5 – are not mentioned as an option. Although oxygen is a good choice for mild steel and F5 for stainless steel, neither is recommended with aluminum because you will not get good cut quality or a nice surface finish.
What else do I need to know about plasma cutting aluminum?
Although plasma cutting is one of the best ways to cut aluminum, its soft nature and lower melting point does make it different than the plasma cutting process for mild steel and other electrically conductive materials. Here are some final thoughts to keep in mind:
- Follow the cut charts in your owner’s manual for the thickness of aluminum you need to cut. This will ensure you set your system at the correct amperage and move your torch at the correct speed.
- Use one of the plasma / shield gas combinations outlined above.
- Move your torch in one direction for the smoothest cuts.
- Do not drag-cut. Ensure your torch is a set distance from the workpiece. Your owner’s manual will provide you with the exact distance.
- If using a water table, work with an authorized Hypertherm OEM to ensure your table is designed for cutting aluminum.
Thanks for reading our post on plasma cutting aluminum! If you are curious about plasma cutting stainless steel, view our post here.