Overcoming labor shortages by going digital
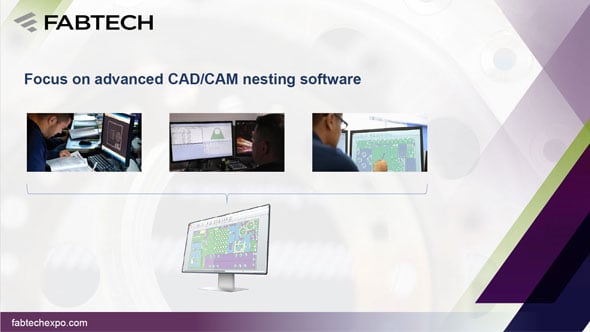
The current skilled labor shortage was a frequent topic of conversation at FABTECH 2022. A lack of skilled workers has affected nearly every sector of the economy, including industrial fabrication. Sadly, it doesn’t look like things are going to get better anytime soon.
Thankfully, we can rely on automation and digital technologies to ease the pressure. Here are three takeaways from a presentation I gave at FABTECH that might help you ease the labor constraints in your own cutting operation.
Take advantage of the powerful but simple software features available today
Adding software and digital solutions is not a new concept. In fact, with the introduction of the Internet of Things (IoT) and Industry 4.0, many fabricators have implemented multiple technologies into everyday processes. Unfortunately, the vast majority of those fabricators aren’t fully utilizing their software technology. If you have not yet implemented advanced CAD/CAM nesting software for your cutting processes yet, then that’s a great place to start. If you have, are you using it to its full potential? Take advantage of the low-hanging fruit to make big strides in your operational efficiency.
Here are just a few examples showing how the standard features in an advanced CAD/CAM nesting software solution like ProNest®, a part of the Hypertherm Associates Software Group, can result in significant time savings for your operation.
-
Automatically prepare the geometry for cutting.
The old saying goes, “measure twice and cut once”. An advanced level nesting software will take the burden of measuring twice. It will automatically apply the correct leads, the correct kerf width, and the correct cut sequence. Reducing this pressure allows the operator to be more confident and accurate in the cutting process. Fortunately, nesting software is not just restricted to large industrial processes. This is an easy enough investment that small metal art designers can use for the creative processes as well.
-
Use automatic nesting algorithms.
A job with 500 parts can take up to 5 hours to nest manually. With an automatic nesting program, this job can take 30 seconds. With features like true shape nesting and high-yield material utilization, you can not only save time but also money on raw materials.
-
Implement a single software solution.
Make things easier by using just one software program for all of your operations. ProNest software can work with virtually any cutting machine brand or model and can support plasma, waterjet, laser, and oxyfuel processes. Consolidating your program into a single software solution is ideal for large metal service companies that may be dealing with multiple brands of equipment. A single software solution also makes training easier!
Better NC Code
Another advantage of CAD/CAM nesting software programs is the ability to improve the cut quality or cutting outcomes. The software does this by embedding the right process parameters directly into the code. Perhaps in the past, businesses could depend on skilled machine operators and skilled programmers with decades of experience to produce the best results, such as sharper corners, cleaner edges, and better hole quality. But those operators are retiring and finding new operators with the same amount of knowledge is tough, if not impossible. By embedding that expertise directly into the software, fabricators can still produce good outcomes.
Here are some examples to illustrate how better NC code can reduce your secondary operations.
-
Produce better hole quality on the plasma table.
Hypertherm Associates was the first to revolutionize hole quality in plasma cutting when it introduced True Hole® technology more than a decade ago. True Hole continues to be an important technology today because it allows you to cut bolt-ready holes right on your plasma table. This in turn can eliminate the need for secondary machine processing like drilling. True Hole is applied automatically by the CAD/CAM nesting software which makes precise adjustments to the code, optimizing parameters like process, gas type, gas flow, amperage, and piercing methodology, just to name a few. The result is that you can virtually eliminate hole taper, reduce dings and divots, and achieve true bolt-hole quality without a skilled operator.
-
Produce better bevel cutting on the plasma table.
The software can make it easier to achieve better, more accurate, and consistent beveled edges. This is done using our True Bevel®, technology which can pre-determine the correct bevel compensations and embed those cut charts into the software. So, when it comes time to setting up bevel cuts, it’s a much easier process. You can save a lot of time and avoid that second step of grinding to achieve a perfect fit.
Advanced software options
This may be the right time to assess your software requirements if your operation has complicated workflows, uses multiple equipment brands, and constantly involves people from different departments. Industrial automation technology has made great strides and is still evolving to meet industry demands. Here are some of the distinct benefits you can enjoy by integrating your ERP/MRP systems with advanced CAD/CAM software.
-
-
Increased inventory turnover
-
Decreased delivery times
-
Better delivery-to-promise rate
-
Reduction in people working to expedite orders
-
ProNest nesting software offers advanced Enterprise modules for ERP/MRP integration. Installing the Data Sync module is the first step in creating the foundation for information interchange between ProNest software and your ERP/MRP software. Once this foundation is in place, you can add other modules such as:
-
-
To store, track, and use all of your available inventory, digital plate inventory management builds a database. It enables you to maintain a record of all plates, remnants, and skeletons so that you always know what is available for nesting. For those with Nesting System Optimization, it can also scan the inventory to suggest the ideal plate for the task. By doing away with the need to physically check for plates, measure plates, and produce remnants, inventory can turn over more quickly. With ERP/MRP integration, the reordering operation can stay ahead of schedule, particularly during severe supply chain challenges.
-
Reduce paper trails and manual work order entry. With digital work order processing, you can handle work orders right from the nesting screen. Real-time data can be automatically imported from your ERP system. To improve efficiency, you can quickly and easily sort the necessary work in the program and merge related work orders into a single job. With ERP/MRP integration, you can always import the most recent work orders first, giving priority to "hot" tasks that must be completed right away, and knowing when work orders have been designated as complete.
-
Track the status of the job at the cutting machine, receive stoppage alerts, and gather insightful data on your overall cutting performance. The Production Manager can establish a direct connection with the CNC machine, even remotely, to check on the machine's status and/or make quick adjustments. The machine operator, shop floor manager, sales, and customer service team members can all see the development in real-time.
-
By relying on automation and digital technologies, you can better manage the skilled labor shortage, save money on raw materials, and increase profits. To learn more about ProNest visit www.hypertherm.com/cam.