Revolutionizing plasma cutting technology with the Hypertherm XPR460
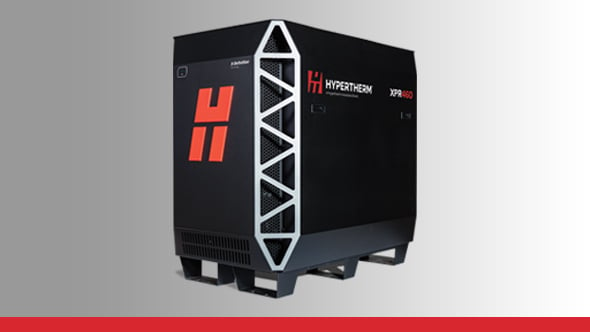
The XPR460 powers your profitability and pays you back with maximum versatility, productivity, and precision
When it comes to industrial manufacturing, the precision and efficiency of cutting tools like CNC and CNC plasma systems can significantly impact productivity and overall quality. One of the most advanced solutions available for high-definition plasma cutting is the new Hypertherm XPR460®. Designed to deliver unparalleled performance, the XPR460 redefines what professionals can expect from plasma-cutting technology.
With its argon-assist technology and gas-connect features, this plasma cutter enhances cutting speeds and edge quality, achieving a precise 45-degree bevel cut with consistent edge-starting.
The XPR460 offers excellent part-to-part consistency and reduces the need for secondary operations. Additionally, its innovative design minimizes ramp-down errors and ensures reliable operation even at higher amps.
This blog post reviews the features, benefits, and cutting-edge applications of the XPR460 and why it stands out in the crowded plasma-cutting system market.
Hypertherm XPR460 overview
The XPR460 is a high-definition plasma-cutting system that utilizes advanced technologies to deliver unmatched cut quality, speed, and operational efficiency. XPR® X-Definition® technology produces superior-quality edges on various materials, including mild steel, stainless steel, and aluminum.
The XPR460 is designed for heavy industrial use, making it ideal for the automotive, aerospace, shipbuilding, civil construction, and metal fabrication industries.
Hypertherm XPR460 key features
Advanced cutting technology
One of the standout features of the XPR460 is its patented X-Definition® plasma technology. This technology increases cutting accuracy while maintaining consistent arc stability, which minimizes taper and slag. As a result, users can achieve smoother, more precise cuts with less need for post-processing. Unparalleled cutting quality
Unparalleled cutting quality
The XPR460 offers exceptional cut quality across a wide range of thicknesses. It can produce sharp edges with minimal angularity, which is essential for applications that require high precision. The system's advanced torch design and innovative nozzle technology work together to ensure that every cut is executed with superior precision.
Power your profitability
Increased productivity
The XPR460 is designed to maximize plasma-cutting productivity. Its high-speed cutting capabilities significantly reduce cutting times, allowing operators to complete more jobs in less time. Additionally, the system's automated features, such as True Hole® technology and Rapid Part™ technology, simplify operations, reducing setup times and increasing overall throughput.
Economic operations
One of the XPR460's key benefits is its ability to reduce overall operating costs. The system's efficiency and speed translate into lower energy consumption and labor costs. Plus, extended consumable life means fewer replacements and lower maintenance expenses.
Greater reliability and longevity
Reliability is a key consideration in industrial environments and the XPR460 does not disappoint. The industrial plasma cutting system is built with rugged components designed to withstand the rigors of heavy use. Its advanced cooling system and protective measures help extend the life of consumables, thus reducing operating costs.
Versatility, the benefits of using the Hypertherm XPR460
Versatility in applications
The XPR460's versatility makes it suitable for a wide variety of applications. Whether you are working with thin materials or thick sheets, the system delivers consistent, high-quality results. Its ability to handle various metals, including mild steel, stainless steel, and aluminum, further increases its applicability across different industries.
Enhanced security
Safety is paramount in any industrial environment and the XPR460 incorporates several features to increase operator safety. Its automated processes reduce the need for manual intervention, thus reducing the risk of accidents.
Improved accuracy and consistency
The accuracy and consistency offered by the XPR460 are crucial for industries where they’re non-negotiable. With features like True Hole® technology, which ensures perfectly round holes with minimal taper and arc stability that produces uniform cuts, the XPR460 helps maintain rigorous quality standards. This consistency is particularly beneficial for repeatable tasks, ensuring that each part meets exact specifications without requiring additional rework.
User-friendly interface
Despite its advanced features, the XPR460 was designed with ease of use in mind. The system has an intuitive control interface that simplifies operation and allows for easy adjustments. Operators can quickly navigate settings and parameters to optimize performance for specific cutting tasks.
Productivity and Precision, real-world applications for the newest in plasma cutting technology
The versatility and high performance of the Hypertherm XPR460 make it an asset for plasma cutting across various industries. Below are some real-world applications where the XPR460 shines:
The auto industry and plasma cutting
Precision and speed are critical in the automotive industry. The XPR460's ability to produce clean cuts in various metals, including high-strength steels, makes it ideal for manufacturing automotive components. From chassis parts to exhaust systems, the XPR460 ensures each part fits perfectly, which is essential to vehicle safety and performance.
The aerospace industry and plasma cutting
The aerospace industry demands the highest levels of precision and quality due to the safety implications involved. The XPR460 meets these demands by providing perfect cuts in materials such as aluminum and titanium, which are commonly used in aircraft manufacturing. Its advanced technology ensures minimal defects, improving the reliability and performance of aerospace components.
Shipbuilding and plasma cutting
Shipbuilding involves working with large, thick metal plates that require powerful and precise cutting capabilities. The XPR460's robust performance and ability to handle thick materials make it an excellent choice for this industry. Whether cutting hull plates or complex internal components, the XPR460 ensures every cut is precise, contributing to the structural integrity of the ship.
Metal fabrication shops and plasma cutting
Flexibility and precision are crucial for metal fabrication shops handling a wide range of projects. The versatility of the XPR460 allows you to easily switch between different materials and thicknesses, making it a valuable tool for custom manufacturing. From architectural elements to industrial machine parts, the XPR460 delivers the quality and efficiency needed in plasma cutting to meet tight deadlines and customer specifications.
Environmental considerations for plasma cutting
In today's world, sustainability and environmental impact are important considerations for any industrial operation. The Hypertherm XPR460 is designed with several eco-friendly features that help minimize your environmental footprint.
Energy efficiency and plasma cutting
The XPR460's advanced technology and efficient design result in lower energy consumption than traditional cutting methods. This reduces operating costs and environmental impact, making it a more sustainable option for manufacturers.
Future trends in plasma cutting
As technology continues to evolve, the future of plasma cutting presents exciting possibilities. The Hypertherm XPR460 is already at the forefront of these advancements, but several trends to watch could further revolutionize the industry.
Plasma cutting integration with IoT and Industry 4.0
Integrating the Internet of Things (IoT) and Industry 4.0 principles into plasma cutting systems will enable real-time monitoring and analysis. This can lead to predictive maintenance, where potential issues are identified and resolved before they cause downtime, further increasing operational efficiency.
Plasma cutting with automation and robotics
The trend toward increased automation and the use of robotics in manufacturing has extended to plasma-cutting systems, enabling fully automated cutting cells. This reduces the need for manual intervention and increases production speed and consistency.
Advances in materials science
As new materials are developed, plasma-cutting systems like the XPR460 must be adapted to handle them precisely. Advances in nozzle design, arc stability, and cutting algorithms will continue to improve the versatility and performance of plasma cutting technology.
The future of Hypertherm XPR460: innovation and commitment
The Hypertherm XPR460 is more than just a plasma cutter; it represents a commitment to innovation, quality, and customer satisfaction in CNC plasma technology. With its advanced cutting speeds, ability to achieve precise 45-degree bevel cuts, and the use of argon-assist technology, the XPR460 sets a new standard. As Hypertherm Associates continues to invest in research and development, we can expect even more advanced features and capabilities, such as improvements in edge quality, edge-starting, and excellent part-to-part consistency to be integrated into future iterations of the XPR® series.
Research and development
Hypertherm Associate’s R&D team continually explores new technologies and methods to push the boundaries of what plasma cutting systems can achieve. This includes:
-
New materials: Developing cutting techniques for emerging materials that are increasingly used in industries such as aerospace and automotive.
-
Software innovations: Enhancing software capabilities to improve ease of use, automation, and integration with other manufacturing systems.
-
Sustainability initiatives: Reducing the environmental impact of plasma-cutting systems through energy-efficient designs and better waste management.
Customer feedback
Customer feedback plays a crucial role in Hypertherm Associate’s development process. By listening to users' needs and experiences, we can tailor our innovations to address real-world challenges and improve overall user satisfaction.
Conclusion: The Hypertherm XPR460 is the best in new plasma technology
The Hypertherm XPR460 is a game-changer in the world of plasma cutting, offering unmatched precision, versatility, and productivity. Its advanced features, robust build, and user-friendly design make it an invaluable asset for industries ranging from automotive and aerospace to shipbuilding and metal fabrication.
By investing in the XPR460, companies can expect not only to improve their cutting operations but also to achieve significant cost savings, enhanced safety, and a reduced environmental footprint. With ongoing support from Hypertherm Associates and a commitment to continuous improvement from both the company and its users, the XPR460 is poised to remain at the forefront of plasma-cutting technology for years to come. Whether you're looking to streamline production, reduce costs, or improve cut quality, the Hypertherm XPR460 offers a comprehensive solution that meets and exceeds the demands of modern manufacturing.
Getting started with the Hypertherm XPR460: assess your needs
Before making a purchase, it is important to evaluate your specific cutting requirements. Consider factors such as the types of materials you work with, the thickness ranges you need to cut, and the required precision level. This will help you determine if the XPR460 is the right fit for your operations.
Need more information? Talk to our experts.