Invest in cut quality: Hypertherm Powermax
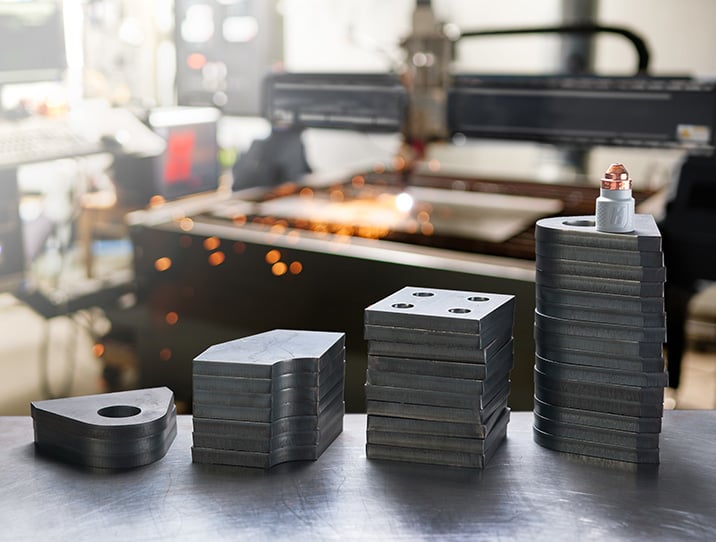
There are many reasons why customers choose to invest in a Powermax® plasma cutter, but one of the most important is the consistent cut quality it delivers. Whether the cuts are made with a handheld plasma torch, a CNC machine torch, or a robotic torch, cut quality from a Powermax is noticeably better than competitive products, not just when the torch consumables or cartridge is new but even after hours of use. This consistent, high-cut quality difference tremendously impacts the reduction or elimination of secondary operations such as grinding, which in turn lowers the customer's cost of operation and increases their productivity. Achieving this level of performance with a Powermax begins with designing and testing consumables and cartridges optimized for the customer’s cutting application.
Cutting performance metrics
Cutting quality refers to cut edge angularity, edge finish or roughness, and attached dross. Many aspects of the plasma cutting system impact the resulting cut quality other than cut speed, cut height, and gas type. The torch consumables or cartridge design and their operation play a key role in determining cutting quality.
Hypertherm Associates’ commitment to cutting innovation enables continued improvement in cut quality. The R&D team evaluates cut quality with new and used consumables. We’ve developed test procedures that quantify and track cut quality as parts wear with usage.
Measuring Powermax plasma cut quality
The cut quality from Powermax plasma systems is evaluated using state-of-the-art measurement equipment such as coordinate measuring machines (CMM) and surface roughness measurement (profilometers), along with statistical tools and ISO standards. Coordinate measuring machines are used to measure the cut quality of the cut surface.
Coordinate measuring machines are used to measure the cut quality of the cut surface.
Cut quality robustness and consumable development
During development, initial cut quality is evaluated by cutting several 3” x 3” (7.6 x 7.6 cm) steel test plates, measuring and comparing the cut quality to strict quality standards. The primary edge features evaluated are edge angle, cut edge straightness, and top edge roundness―side-to-side variations and surface finish. We follow ISO 9013 standards for cut-edge quality determination.
A key consideration for consumable and cartridge development is cut quality robustness as the consumables wear over the life of parts. This consumable and cartridge development metric is termed “cut quality over life.” Engineers assess the cut quality by cutting steel test plates every 30 minutes (plasma arc time) of consumable wear until the consumable blows out.
Pierce robustness and rating
Plasma-cutting consumables and cartridges are designed to pierce (cut through) up to a certain thickness. Designing consumables and cartridges that can pierce thick material a few times is straightforward. However, our pierce protocol requires piercing the rated thickness 300 times on a cut table. Our engineers design consumable and cartridge parts and gas flow to support this lofty design specification.
Example of one of the piercing test plates.
Transfer height and arc stretch analysis
Powermax plasma systems are widely used in many applications, including those requiring high transfer and arc stretch heights (such as gouging, cutting in areas with limited access, and flush cut applications).
We place strict requirements to deliver high transfer height and allow large arc stretch. The Powermax power supply architecture, control schemes, consumables, and cartridges must be concurrently developed to provide industry-leading performance.
We primarily develop the cut quality for mild steel, stainless steel, and aluminum. However, our customers use our cutting equipment to shape various metals and alloys depending on the workpiece.
The Powermax cartridge advantage
The Powermax SYNC® cartridge consumable platform introduced a single-piece cartridge that delivers industry-leading cutting performance. This is achievable because Hypertherm engineers customized the individual parts of the cartridge (such as electrodes, swirl rings, nozzles, and shields) to meet and exceed the cutting expectations set by users. Each cartridge was meticulously designed by assessing the initial cut quality, quality over life, pierce rating, longer consumable life, and other design requirements.
Every time a user installs a Powermax cartridge, the components are new. Unlike competitive products, Powermax cartridges ensure high-quality cuts from the start and maintain cut quality robustness throughout most of the cartridge life.
Powermax SYNC with a cartridge enables consumable optimization that delivers superior edge features.
The Powermax line of products is widely used in a variety of applications. Hence, the product is expected to deliver the best-in-class arc stability, transfer height, and arc stretch. This is achieved by concurrent development of consumables and power supply architecture.
Get the most from your Powermax plasma cutter
To realize the cut quality benefits from Hypertherm consumable and cartridge designs, customers need to do their part by perfecting their cutting processes. When handheld cutting, operators must use proper cutting techniques. These include maintaining a consistent torch angle to reduce cut angularity, identifying the ideal torch travel speed for dross reduction (both high-speed dross and low-speed dross), serration reduction, and, when piercing, using the best method to prevent damage to the consumables or cartridge. In addition, operators using CNC plasma cutting on a plasma table or robotic torches need to set the correct torch height, arc voltage, travel speed, and pierce height and delay. The choice of the proper amperage consumables or cartridges is vital, as well as the best plasma gas (air, nitrogen, argon, or F5) and gas pressure for the metal type being cut.
Stainless steel cut with air (left) and with F5 gas. The 95% nitrogen / 5% hydrogen gas blend gives cuts a silver-color edge, a good angle, and a sharp edge. The blend is recommended for stainless steel only.