How to Choose Between Laser and Plasma Cutting: Chart
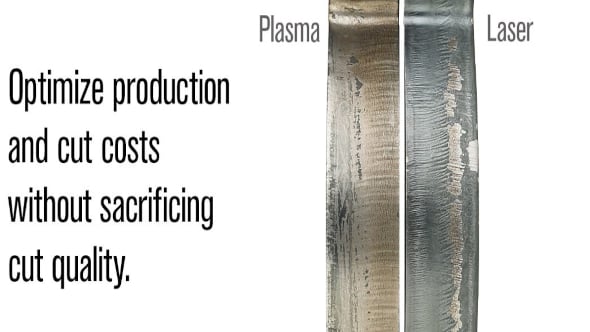
There are many considerations when choosing between a plasma cutting system and a laser cutting system. While the two technologies were explored in depth in this blog, today, we want to focus on seven key differentiators: cut quality, versatility, cost, safety, time savings/automation, durability, and situations where each technology is ideal. Plasma cutting and laser cutting each offer advantages, so choosing the right one for your business depends on your cutting needs – specifically, the type of material you will be cutting, material thickness, cut complexity, and customer requirements for cut quality.
What is plasma cutting?
Plasma cutting is a thermal cutting process that uses a high-velocity jet of plasma to cut through electrically conductive materials like steel, aluminum, and other metals. It is commonly used for metal fabrication in the manufacturing, construction, and automotive industries because of its speed and accuracy.
What is laser cutting?
Fiber laser cutting is a high-precision and versatile technology that uses a focused beam of light to cut, engrave, or mark various materials. It is widely used in industrial, commercial, and hobbyist settings for applications ranging from cutting metal and plastics to etching intricate designs on wood or ceramics.
Cut Quality
Both plasma and laser have good cut quality, with fiber delivering better results on thinner metals and plasma delivering cleaner results on thicker metals. While laser cut quality is generally better, plasma cut quality exceeds most customer requirements. Therefore, the higher cut quality laser delivers may provide no real benefit to users or their customers.
Plasma
-
Cut quality in ISO 9013 range 2–4
-
Cut quality rivals fiber laser cut quality, exceeds most customer requirements
-
Minimal secondary operations required for weld preparation
-
Cut edges are smooth and straight
-
Plasma yields minimal oxide layers and dross
Laser
-
Cut quality in ISO 9013 range 1–2
-
Thinner kerf size and low angularity benefits
-
High precision and accuracy
-
Excellent cut quality on thin metals
-
As thickness increases over 12–16 mm, rougher surface finish and more dross
Cutting Versatility
Both plasma cutting and laser cutting are quite versatile, with the ability to cut complex shapes, engrave, and mark. Laser can cut more materials, but it needs cleaner materials – sometimes requiring cleaning or precut vaporization, reducing productivity. Plasma can cut imperfect, uncleaned metals, but can’t cut plastic. Therefore, which one you choose depends on your business needs.
Plasma
-
Greater standoff distance means less interference with the cutting process
-
Cuts straight lines, bevels, holes, and complex shapes
-
Cuts stainless steel, mild steel, aluminum, copper, brass, and other metals
-
Cuts material that is imperfect and painted, rusty, or coated
Laser
-
Can cut, engrave, and mark
-
Can cut complex and intricate shapes
-
Cuts steel, aluminum, copper, plastics, and composites
-
Requires specialty-grade materials, manual cleaning, or a pre-cut vaporization
-
process, reducing productivity
Cutting Costs
Laser cutting systems are generally two to five times more expensive than plasma cutting systems; however, laser systems use fewer consumables and minimize material waste. Which system is more expensive over time depends on how the system is being used. Plasma typically has lower operating costs when cutting materials thicker than 12 mm, and laser has lower operating costs when cutting thinner materials.
Plasma
-
Often has ROI of 2 years or less
-
More affordable consumables
-
Minimal post processing
-
Typically, lower operating costs than fiber laser when cutting materials thicker than 12 mm
Laser
-
Cutting systems are 2x–5x the cost of plasma
-
Fewer consumables used
-
Minimizes material waste
-
Typically, lower operating costs than plasma when cutting materials thinner than 12 mm
-
High gas and electricity costs when cutting thicker materials
Safety
Plasma cutting is safer than laser cutting. Plasma cutting only requires eye protection for extended viewing of the plasma arc. Laser cutting requires enclosures and material handling for safety concerns.
Time savings and automation
Plasma
-
Excellent choice for high-volume production and high cut speeds
-
Can be easily integrated with CNC systems for automated cutting and cutting complex shapes and patterns
-
Great for high-volume production or customized components
-
Great option for robotic cutting
Laser
-
On thicker plates, parts can be difficult to remove from the skeleton, needing to be hammered out
-
Can be integrated with CNC systems for automated, repeatable, high-volume production
-
Faster cut speeds for thinner material
Cutting Machine Durability
Plasma systems require simple in-house maintenance. Laser systems are more sensitive to dirty environments and require regular cleaning and highly technical maintenance that may require an authorized service center.
Applications that plasma and laser are most ideal for
Plasma cutting systems are ideal for thicker materials over 12 mm – 16 mm and applications that require faster cut speeds. Laser cutting systems are ideal for cutting materials thinner than 12 mm – 16 mm that require high precision, excellent edge quality, and intricate cuts.
Conclusion: The best choice depends on your application
Plasma cutting and fiber laser cutting both offer advantages, so choosing the right one depends on what you do with the system. Plasma requires a smaller initial investment and is easier to maintain and safer to use. It outperforms laser on thicker metal and rivals laser on thinner metal.
The question comes down to the thickness of the metal you are cutting, how precise your cutting needs to be, and how much you are willing to pay for that higher level of precision – and if your customers demand it.
Check out this comparison chart below.
View comparison chart
Read our blog, “Plasma cutting vs. laser cutting: a guide” for a more in-depth comparison of laser and plasma cutting.