X-Definition plasma delivers big improvements in hole quality and expanded non-ferrous cutting
- Part 3 -
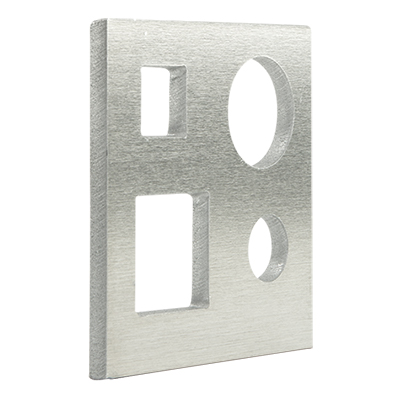
Editor’s note: This is the final article in a three part series. Read Part 1 and Part 2.
Hole quality
Beyond edge angularity, XPR® and X-Definition® attacked the issue of hole quality. Whereas, older plasma systems delivered holes with tapered sides and protrusions inside the hole, True Hole® using an X-Definition plasma process on XPR is capable of delivering bolt quality holes on mild steel with diameter to thickness ratios ranging from 2:1 to 1:1. Compared with earlier non-X-Definition True Hole, full cylindricity measurements and bottom-of-hole roundness have been improved.
True Hole on XPR delivers superior plasma cut holes from a thickness to diameter range of 2:1 to 1:1, as depicted here. Cylindricity and bottom hole roundness have been improved over non-X-Definition True Hole.
Big gains with non-ferrous cutting
X-Definition plasma also broke new ground with non-ferrous cutting by introducing a wide range of new process technologies to optimize results on different thicknesses of stainless steel and aluminum. In fact, it is probably non-ferrous cutting where people are most surprised by the new capabilities associated with X-Definition. For thinner stainless steels, up to about 10 mm (3/8”), enhanced HyDefinition® Inox (HDi) processes using either N2 for the plasma and shield gas or a combination of an F5 plasma and N2 shield gas deliver excellent edge quality. You will get parts with a smooth surface finish, a neutral/shiny color finish, and essentially no dross. ISO ranges for these cuts is typically 2 or 3.
60 amp N2/N2 HDi on 3 - 10mm (10ga - 3/8”) delivers square, smooth dross free cuts. Especially below 10 mm (3/8”) edge is shiny and neutral in color.
Example of 80 amp F5/N2 HDi on 10 mm (3/8”). Edges are sharp, with minimal angle, very smooth and shiny, with no dross.
On thicker stainless steel, when using discretely mixed H2-Ar-N2 as the plasma gas and an N2 shield, X-Definition plasma processes will produce stainless steel cuts that are typically in ISO range 3 or 4, typified by bright, smooth edge finishes, no dross and good perpendicularity. The X-Definition discrete gas mixing capability also allows the user to modify the gas mix to optimize results for different grades of stainless steel.
Discrete 3-plasma gas mix (H2-Ar-N2) with an N2 shield provide excellent cuts on thicker stainless steel, 12 mm (1/2”) and thicker. Edges are smooth, shiny and either neutral in color or slightly gold-toned (higher mix of Ar). Cuts are essentially dross free and perpendicularity typically ranges from ISO range 3 to 4.
And finally, using a new X-Definition N2/H2O (nitrogen plasma and water shield) process called Vented Water Injection™ (VWI), the XPR300 can generate results on aluminum that are truly remarkable compared to earlier generation plasma cutting.
The aluminum stack shows X-Definition’s VWI process delivering exceptionally smooth cut surfaces, with low angularity (ISO range 3 to 4) with no dross across a variety of thicknesses.
These two samples show its ability to deliver fine features, including interior slots and holes, on thinner aluminum.
The purpose of these articles are not to assert that the XPR and X-Definition plasma is the solution of choice for all metal cutting applications. Rather, it is to suggest that if you are a fabricator thinking of purchasing a laser cutting system and have not seen what X-Definition plasma on XPR can do, you may be in jeopardy of spending substantially more on your cutting system – many times more, in fact – than necessary given your specific applications. While there are some things that laser is uniquely able to do – extreme fine feature cutting and extreme tight tolerance capability, for example – in terms of perimeter edge squareness and smoothness, hole capability, some level of fine feature capability, down-stream weldability and non-ferrous cutting, X-Definition class plasma may well be the more cost-effective approach. If this article has met its objective, we would be pleased to take the next step with you to determine which technology would provide the most cost-effective solution for your specific cutting needs.
Are you ready to see what today’s X-Definition plasma can do? If so, contact us today.