Understanding how machine motion impacts the performance of X-Definition class plasma
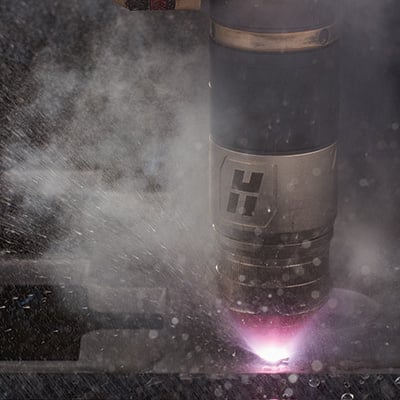
Hypertherm’s X-Definition® class plasma, currently available in our XPR™ systems, is a high-tech, highly advanced and sophisticated cutting process that reflects many years and countless thousands of hours in engineering development, validation and testing. However, in isolation, the XPR systems are nothing more than an extraordinarily well engineered assemblage of sheet metal, copper, electronics, wires, cables, hoses, valves and sundry components. In isolation, these systems are, in fact, useless. They can only create value and deliver benefits in the context of their integration into the complete cutting machine. The cutting machine and the quality of motion it delivers is critical to the ultimate performance of the XPR system that it is integrated into.
Here’s an analogy that may help bring home the importance of the relationship between machine motion and the plasma system. Say you have a Formula 1 racing engine in your garage; just the engine, sitting on concrete. You paid a lot for it, but it has no value because it is not mounted and integrated into an automotive frame, suspension, and transmission system. Now say you opt to mount that Formula 1 engine into a standard street car assembly. What would be the result? You have an engine capable of extreme performance mounted in the frame of an automobile that is not. The engine performance would make worse every deficiency of the automotive frame and suspension. The engine would push the frame and suspension, even if well-designed for its intended purpose, well beyond those design limits. The results would not be pretty. In fact, in this case, the street car frame and assembly would actually perform better with the 2.5 or 3.0 liter engine that was optimized for its use.
Integrating an XPR system into a cutting machine that is not delivering good motion, or which was designed for a lower-performance plasma system, is similar to the above example in that it would deliver suboptimal results and not provide the performance benefits the plasma system is designed to produce. In all likelihood, as with the car example above, you would get better cutting results by using a lower performance plasma system in such a cutting machine.
The X-Definition processes found in our XPR systems can deliver arc densities approaching 70,000 amps per square inch (110 amps per square millimeter). This high performing arc is much more likely to reveal motion issues than is a conventional plasma arc, which delivers lower arc densities. Our XPR systems are also designed to deliver high quality cuts at higher cutting speeds. Again, the faster the machine needs to track, the more it is likely to reveal machine motion issues.
What are some of the key motion requirements that need to be considered when buying an X-Definition class system? Here are a few key guidelines to consider when operating a machine at moderate cutting speeds of 1,270 mm/min (55 ipm).
- Rail and transverse axis velocity overshoot should be less than 10% to ensure optimal cut quality into and out of corners.
- Rail axis acceleration should be a minimum of 40 mG to handle all True Hole® processes. This higher acceleration will also reduce cycle time and ensure the arc arrives at its optimal travel speed more rapidly. Higher acceleration ratings generally translate into better motion.
- Rail and transverse axis following error should be no greater than 0.25 mm (0.010”) to ensure that the plasma start and stop timing is consistent with the machine motion for good cut quality and True Hole performance.
- Dual gantry following error should be less than 0.08 mm (0.003”) to ensure that rail 1 and 2 axes are not fighting each other and delivering consistent results.
- Maximum distance off path should be no greater than 0.05 mm (0.002”) on a 6 mm (0.25”) hole to ensure high table accuracy.
- Circularity should be less than .23 mm (.009”) to ensure good quality/round holes are produced.
- The cutting machine should be able to smoothly and accurately track at speeds of up to 6,350 mm/min (250 ipm) in order to take full advantage of all processes offered by the XPR300.
Summary
Operating an XPR plasma system on a cutting machine, even if equipped with the very best CNC and software, does not ensure optimal cutting results. The quality and capability of the cutting machine itself is critical. If you want to maximize the investment that you make in an XPR system, you need to also invest in a cutting machine that is designed to handle its performance. You need to ask questions about machine motion capability and provide your potential machine builder with part programs for the parts you will be cutting to ensure you get the results you are looking for. And, while superior motion will cost more, in concert with an XPR system, it will more than pay for itself with reduced secondary operations, greater operational flexibility, improved productivity and lower overall operating costs.