Automated plasma cutting tips and techniques
Proper piercing technique leads to lower operation costs and improves productivity
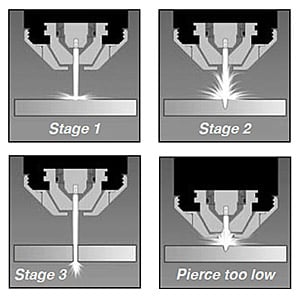
Here is a pop quiz for the plasma cutting supervisor, industrial engineer, purchasing agent, or maintenance man: What is the number one cause of premature parts failure in plasma torches?
a) Inadequate plasma gas flow
b) Inadequate coolant flow (water or gas)
c) Plasma cutting machine malfunction
d) Improper piercing technique
If you answered a), b), or c), you get partial credit. If you answered d), you are correct and you are on your way to saving money and decreasing downtime on the plasma cutting machine.
Piercing too close to the material is the most common cause of premature consumable parts failure. This assertion is based on years of direct communication with end-users and analysis of failed consumable parts. The problem sounds simple enough to correct, yet it persists in most cutting operations. One reason is the lack of good technical training for plasma cutting machine operators. An operator needs to know both the theory and the technique – the "why" and the "how to" – in order to improve his operation. Armed with a fundamental understanding of the process and a couple of simple tips and techniques, he will spend more time cutting parts and less time changing consumables.
What happens during a pierce?
When the torch fires, a high-voltage spark, combined with a limited amount of DC current, produces a pilot arc at the torch. This pilot arc projects from the end of the torch in a steady, white-blue arc about ½-1-inch in length. The pilot arc forms an electrical pathway from the cathode (the electrode in the torch), to the anode, (the conductive material being cut). If the torch is within transfer distance, the arc will transfer to the metal and begin to pierce. Every torch has a maximum transfer distance that is also its maximum pierce height. If the torch is higher than this distance it will pilot in the air; if it is lower, it will transfer and begin to pierce.
Stages of a pierce
Stage 1. The transferred arc instantly heats the metal to its melting point and begins blowing the molten material away. In the initial stage of the piercing operation, the molten metal sprays out axially from the pierce point over the top of the plate in a shower of sparks.
Stage 2. As the plasma jet penetrates deeper into the material, a round-bottomed hole forms. This hole begins to direct the molten spray upward toward the torch. (This is analogous to what happens when you hold a shot-glass under a stream of water from a faucet).
Stage 3. Once the arc breaks through the bottom of the plate, the sparks and molten material are ejected out the pierced hole. When the pierce is completed and the arc has grown to its full strength, the machine begins to move and the torch starts cutting. If the torch moves too soon, the arc may not fully penetrate the material. If the torch delays too long, the arc will continue to remove material enlarging the hole until it extinguishes. See illustration below.
Piercing problems:
The most common piercing problems - double arcing, bridging, and snuffing - occur during the second stage of piercing when a fountain of 1500° C molten metal is sprayed back up at the torch. Under normal conditions, the arc column is controlled and focused by a swirling vortex of gas as it passes from the electrode, through the nozzle, to the plate. This boundary layer of gas prevents the arc from contacting the copper nozzle. If the arc does contact the nozzle it will cut it as it does to any conductive metal.
Double arcing is a term for any arcing that occurs secondarily to the main cutting/piercing arc. Double arcing occurs when current flows through the nozzle or through another conductive path to the plate other than directly through the arc column. This can occur due to low plasma gas flow, excessive amperage or a serious disturbance in the plasma jet. Such a disturbance happens when the torch is piercing too close to the plate. The spray of electrically conductive metal disturbs the plasma gas jet by disrupting the electric field surrounding the arc and causing the arc column to grow. It is theorized that multiple arc paths develop through these tiny bits of metal, pulling the arc out of its axial-symmetric path. If the arc is pulled into the sidewall of the nozzle it causes a gouge, nick or sometimes a symmetrical chamfer along the exit orifice (flowering). Damage to the nozzle leads to serious cut quality problems such as excess bevel angle, dross, failure to penetrate the material etc.
Bridging is a more extreme form of double arcing. It occurs if the molten material builds up in a puddle that contacts both torch and plate. Since this puddle is electrically conductive, it provides a short circuit to the workpiece. The arc sees a path of lower resistance, to the plate and takes it. This usually causes a catastrophic failure of the shield and damage to the nozzle. Even the state-of-the-art electrically isolated copper shields of today's plasma torches are not immune from this type of failure. Once the shield is in contact with a ball of molten material it is at the same potential as the plate, therefore the arc will conduct through the shield causing it to fail.
Plasma gas snuffing is the most extreme form of double arcing. Snuffing occurs when the torch begins to pierce with the torch nozzle or shield pressed against the plate. For example, if the automatic torch height control finds its initial height by pushing against the plate, and the plate is bowed or thin enough to be pushed down, then the retraction of the torch will not set the correct initial height. The torch will fail to "clear the plate" because the plate follows the torch back up to its initial height setting. This often occurs in underwater cutting applications when the operator can not see the front end of the torch. Snuffing of the plasma gas leads to uncontrolled double-arcing in the plasma chamber. This causes catastrophic failure of the electrode, nozzle, and shield.
Tips and techniques:
- Pierce high and cut low: The rule of thumb is to pierce at 1.5-2X the cut height or at the maximum transfer distance. Piercing high prevents double arcing, bridging, and snuffing.
- Use a creeping pierce: If your CNC is capable, use a creeping pierce. This feature slowly moves the torch during the pierce operation causing the "rooster tail of molten material to miss the front end of the torch. (Think of the shot glass with the water streaming into one side rather than the middle).
- Don't eyeball the pierce height: Use the initial height sensing if it is available. Manual piercing is usually not recommended. Even experienced operators don't have a perfectly calibrated eye.
- Don't pierce beyond system limits: Pierce rating is typically 1/2 the cut rating
- Avoid piercing: Whenever possible use chain cutting or edge starting (for example off the edge of a punched hole) to reduce the number of pierces.
Special techniques:
Experienced operators sometimes use two special tricks for getting through thick plate.
WARNING: Do not try these techniques unless you are an experienced plasma operator and are familiar with safe operation of the plasma system.
Double shot: This technique involves "blowing" through the plate in two or more successive pierces rather than one. The first pierce establishes a round-bottomed hole about halfway through the plate. The operator then manually moves the torch over slightly toward the edge of the hole and pierces again. The second shot blows through the material. The rooster tail of molten metal is deflected away from the torch.
Rising pierce: This technique is a manual piercing operation in which the torch is brought down to the plate with the pilot arc on. As soon as transfer occurs, the operator raises the torch (stretching the arc) to as high as 1" above the plate. Then as the plasma jet blows through the plate, the operator brings the torch down to normal cutting height. This is used to protect the torch and shield. It is not good for electrode or nozzle life.