Precision metal marking with the Powermax45 XP plasma system
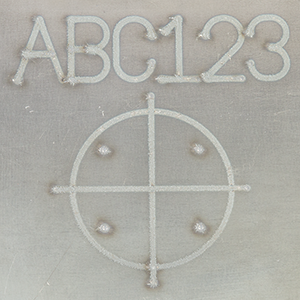
The Powermax45® XP plasma system is an ideal tool for many widely used metal marking applications, including:
-
Part identification numbers
-
Score lines for weld or bend placement
-
Dimples for drilling applications
Specifically designed to provide a stable, low-current plasma arc using the precision gouging nozzle and marking shield, the Powermax45 XP can make high-quality marks using a handheld or machine torch with either air or argon as a gas source.
Metal marking with plasma
Fabricators and manufacturers routinely mark metal to indicate bend or score lines or to add precise technical information – such as part numbers and barcodes – to parts. This work is often performed using a hammer and punch, powder or ink, soapstone, or handheld engraving machines, but marking can also be done using a handheld plasma cutter or as a process step on a mechanized plasma cutting table.
Choosing to mark metal with plasma – whether by hand or as part of an automated process – has several advantages. Marking with plasma is more permanent than using soapstone or ink, and plasma can be used on wet or oily plate. It eliminates the clogging problems and humidity concerns associated with powder marking, and marking with plasma is safer, faster, and more accurate than marking with ink or with a hammer and punch.
The precise nature of marking done during the CNC cutting process yields more accurate and legible marks than can be accomplished with handheld marking. The depth of marks can be precisely controlled to determine whether marks remain visible after coatings are applied.
The versatility of the portable Powermax45 XP plasma system makes it ideal for both handheld and mechanized marking applications and for making temporary or permanent marks on metal surfaces such as mild steel, stainless steel, and aluminum.
The Powermax45 XP
The Powermax45 XP plasma cutter provides a recommended cut capacity up to 16 mm (5/8 inch) as well as fast cut speeds and automatic gas adjustment for quick, simple setup and operation. Duramax® Lock torches support handheld and mechanized cutting of a wider range of metal thicknesses, along with precision gouging such as spot weld removal, and marking capabilities.
The Powermax45 XP is easy to use. Smart Sense™ technology ensures the air pressure is always correctly set and patented drag-cutting technology lets operators drag their torch right on the metal when cutting. Drag cutting is easier than holding a standoff because the operator does not have to hold a steady hand and maintain the same distance from the workpiece while cutting. It usually produces a more accurately cut piece as a result. Drag cutting also helps increase consumable life, since spatter and blowback aren’t as much of a problem.
The Powermax45 XP has a wide range of torches and consumables to choose from for both handheld and mechanized processes. It has an extensive array of application capabilities via specialty consumables, including fine feature cutting, extended reach cutting, gouging, precision gouging, and marking.
Operators gain efficiency with the Powermax45 XP. Superior cut and gouge quality reduces the time required for secondary operations like grinding and edge preparation. The torch disable switch enables faster, easier changeout of consumables, decreasing downtime and increasing overall productivity.
The Powermax45 XP is rugged and reliable. Duramax Lock torches are designed for high impact and heat resistance, and SpringStart™ technology ensures consistent starting and optimum torch performance.
Light score and heavy score mark profiles
There are primarily two different types of mark profiles: light score and heavy score. Usually, the choice depends on whether the mark will be seen on the final product. If the mark needs to be visible after painting, for example, a heavy score is preferable. For temporary part identifiers that won’t be needed after final assembly, a light score is probably a better choice, as it can be easily removed with a grinder or covered with a layer of paint.
A number of parameters of the Powermax45 XP system can be easily adjusted to achieve different mark depths, widths, and appearances on various types of metal.
-
A low output current of 10 amps will produce a light score.
-
A higher output current of 15 to 25 amps will provide a heavier score.
-
Slower torch motion speeds combined with a low torch-to-work distance will increase the width and depth of the mark.
-
Faster torch motion speeds with a higher torch-to-work distance will decrease the width and depth of the mark.
![]() |
![]() |
Metal marking using light air |
Metal marking using heavy air |
When to use air or argon
The choice of air or argon will also impact the mark width and appearance on different types of metals. Argon will give you shallower, narrower marks, and a cleaner final product. Air will oxidize the metal surface, producing small amounts of dross and a somewhat coarser mark than argon. It will also leave a dark layer of oxidized metal on the metal surface.
Air does offer one big advantage: its relatively low cost. The electrical cost to produce compressed air is a fraction of the price of bottled argon.
Where argon is required, automatic gas detection technology in the Powermax45 XP helps reduce gas consumption in gouging/marking mode, providing significant cost savings compared to other plasma marking systems.
Conclusion: The Powermax45 XP is ideal for metal marking applications
The Powermax45 XP plasma system’s stable, low-current plasma arc, precision gouging nozzle, and marking shield produce high-quality marks with both handheld and machine torches. It can be easily adjusted to achieve different mark depths, widths, and appearances on various types of metal – ensuring users achieve exactly the marks they need.
Learn how the Powermax45 XP can help you improve metal marking. Click the button below, fill out the form, and a Hypertherm product expert will contact you.