Laser tolerances: Don’t get trapped in the tighter is better mindset when it comes to tolerances
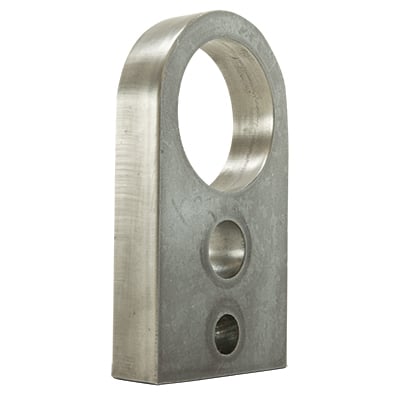
Though laser and plasma both cut metal using a thermal process, they work in very different ways. Regardless of type — CO2 or fiber — laser uses an intense, coherent beam of monochromatic light created by a stimulated emission of electromagnetic radiation. One of the advantages of a focused beam of light is that it can cut to extremely tight tolerances. There is less variability in the process. Generally, a laser can hold cut part dimensional tolerances of under 0.01" (0.25 mm).* Plasma on the other hand, uses a gas energized to the point of ionization to create a super concentrated arc that focusses energy at an extraordinarily high temperature. This results in cut part dimensional tolerances of roughly 0.02" (0.5 mm),* if using an X-Definition® capable plasma system.
There are tradeoffs to consider in part tolerancing and manufacturing process specifications and one of them is the cost driven by unnecessarily stringent requirements – the differences between laser and plasma tolerances as described above is only about the thickness of a common business card! So, before asking for “laser quality” or lobbying for laser equipment and facilities upgrades to accommodate the new equipment, you should ask yourself: “Do I really need these very tight tolerances on this part?”
Hidden costs of tighter tolerancing
As a general rule, tighter dimensional tolerances create added cost in your manufacturing operation and product. If the form, fit or function of the part truly doesn’t demand tight tolerancing, these tighter specs are burdening your operation with unnecessary costs, costs that may reduce profits or put the firm at a disadvantage against the competition, or both!
Asking for tighter than necessary tolerances can cost your operation money in the following ways:
-
The upfront cost of the machine tool that is required to deliver the tolerances. In the case of a laser versus an X-Definition, XPR®, plasma system, the differential investment cost can be many hundreds of thousands of dollars. Significant investments impact a company’s balance sheet and depreciation expenses.
-
The cost of inspection equipment. Tighter tolerances generally correlate with higher inspection equipment costs. If your tolerances can be measured with a tape measure or other low tech equipment, your inspection equipment cost is minimal. If, on the other hand, your tolerances require a more sophisticated measurement tool, for example, a CMM (Coordinate Measurement Machine) your investment cost could be as high as $120K. Even worse, if you specify tolerances that you aren’t able to measure accurately, you may be spending money on something you aren’t actually getting.
-
Frequency of measurement and training required to implement the measurement regimen. Generally, the tighter the tolerances, the more frequent the measurement requirement and the more training is required to use the measurement equipment. Using the earlier example, the training and pay level required for an employee to measure tolerances using a tape measure are very different from an employee using a CMM.
-
Scrap. Another cost increase relates to scrap. The process used to cut must have proven capability to meet the tolerances specified. If the capability is marginal, or if capability can degrade over time, a higher rate of scrap is likely.
-
Supply chain issues. Defining tighter tolerances may also limit your ability to outsource or to find capable suppliers. Competition among suppliers may be reduced, which, in turn, may result in a higher price to you.
-
Reduced throughput. A requirement for tighter tolerances may come at the cost of reduced cutting speed and throughput. Depending on the material type and thickness, the results could be substantially higher operating costs and fewer parts produced in each period.
To optimize profits, consider implementing a rigorous DFM (Design for Manufacturability) process with engineering and operations, so that parts are properly dimensioned and specified for the functions they provide.
If a part is going from the cutting table to the welding bay, for example, where the weld tolerance may greatly exceed the dimensional tolerance allowed by the part specification, the tight tolerances specified in the part design may be meaningless.
Don’t get trapped in the tighter is better mindset when it comes to tolerances. Part specifications should be considered with an eye for part cost and functional tradeoffs to avoid unnecessary manufacturing investment and costs.
*Dimensional tolerances may vary according to the thickness of the metal being cut.
Learn more about X-Definition® capable plasma systems.