Plasma cutter gouging techniques
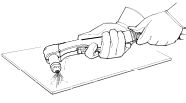
Plasma gouging is used to remove metal from a workpiece without piercing or severing it. A plasma arc between the torch and the workpiece melts the surface metal, and a gas jet blows the molten metal away from the workpiece. Gouging is frequently used to remove unwanted metal in preparation for welding and casting. With practice, operators can achieve smooth, clean, and consistent gouges with plasma.
Benefits of gouging with plasma
Plasma gouging has many advantages over oxyfuel and carbon arc gouging methods. It works on any conductive metal, including mild steel, stainless steel, aluminum, and copper. Plasma gouging is faster than oxyfuel and carbon arc gouging, delivering increased productivity. It provides more consistent and repeatable gouge profiles, requiring less secondary work. Plasma gouges are free of carbon contaminates, ensuring workpieces meet contamination requirements.
Plasma gouging is also better for operators. It requires less training time and has a shorter learning curve, enabling new operators to quickly become proficient. Plasma gouging has improved worker safety over oxyfuel and carbon arc gouging, with lower noise and debris levels to meet regulatory and workplace safety requirements.
Preparing to gouge
Plasma cutter operators use a variety of techniques to achieve different gouge profiles and sizes, whether gouging by hand or using a mechanized method like a track cutter. When gouging by hand, it is important to first ensure the plasma cutting system is properly set up.
To begin, make sure the torch, work cable, and input gas supply are properly connected and the ground clamp is attached to the workpiece or table ground. Remember to always wear the appropriate personal protective equipment when operating a plasma cutting system, including gloves, eye protection, and protective clothing.
Next, install the appropriate gouging consumables onto the torch based on the type of gouge you want to produce. Plasma systems like the Hypertherm Powermax® use gouging consumables designed to optimize gouging performance.
-
Maximum control consumables are designed for more precise metal removal, light material washing, and for when a shallow gouge is desired. If you are learning to gouge, you may want to start with maximum control consumables to prevent any workpiece damage.
-
Maximum removal consumables are designed for aggressive metal removal applications, deep gouge profiles, and extreme metal washing. Faster gouging speeds are recommended to control the concentrated plasma arc.
-
Precision gouging consumables are designed for removing small amounts of metal or weld at very low output current.
-
Extended cutting and gouging consumables allow for easier access when gouging in hard-to-reach or confined work spaces.
Many plasma cutters have a dedicated operating mode for gouging that adjusts the amount of pressure traveling to the torch. If your plasma cutting system has a dedicated operating mode for gouging, make sure you set your system to gouging mode to begin.
Gouging a workpiece
The most common gouging technique involves positioning the torch at a 40-degree angle to the workpiece while the pilot arc is formed and transferred to the plate. Once contact is made, the operator simply aims or feeds the arc in the direction they want to gouge.
Hold the plasma cutter torch so that the nozzle is within 1.5 mm (1/16") from the workpiece before firing the torch.
- Hold the torch at a 40 angle to the workpiece with a small gap between the torch tip and the workpiece. Press the trigger to obtain a pilot arc. Transfer the arc to the workpiece.
Maintain an approximately 40-degree angle to the workpiece as you feed into the gouge, pushing the plasma arc in the direction of the gouge you want to create. Changing the torch angle changes the dimensions of the gouge. Keep a small distance between the torch tip and the molten metal to avoid reducing consumable life or damaging the torch.
Variations to the angle of the torch, the speed of travel, arc stretch, and amperage adjustments will control the depth of a gouge.
Changing the gouge profile
The gouge profile is the shape left after removing metal from the workpiece. There are several techniques you can use to change the gouge profile to fit your needs. You can use these techniques to make small adjustments or significant changes to the gouging outcome.
-
Changing the speed of the torch movement will change the gouge profile. Increase the speed of the torch movement to make the gouge narrower and shallower. Decrease the speed of the torch movement to make the gouge wider and deeper.
-
Changing the angle of the torch to the workpiece will change the width and depth of the gouge profile. Put the torch in a more upright position to make the gouge narrower and deeper. Tilt the torch down with a lower torch angle (so the torch body is closer to the workpiece) to make the gouge wider and shallower.
-
You can vary the torch-to-work standoff distance to produce a different gouging profile. Move the torch away from the workpiece to make the gouge wider, shallower, and smoother on the bottom. Move the torch closer to the workpiece to make the gouge narrower and deeper.
-
Adjusting the output current of the power supply changes the gouge profile. Decrease the amperage to make the gouge narrower and shallower or increase the amperage to make the gouge wider and deeper.
Impact to gouge profile parameters
For more detailed information on achieving specific gouge profiles, refer to your system’s operator manual. For tips on how to improve gouging outcomes, visit Hypertherm’s extensive documents library and video library.
To learn how to maximize gouging performance with the Powermax plasma cutting system, contact a Hypertherm product expert.