Torch height control for plasma cutting
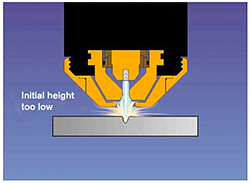
The automatic torch height control (THC), typically part of a CNC plasma table is one of the most important elements of the mechanized shape cutter. But it is also the piece of equipment on the CNC plasma cutter most likely to be misused, nonfunctional, or even missing. In many fabrication shops you might see the table operator manually driving the torch up and down while cutting—his eye on the torch and his thumb on a toggle switch. This is the manual method. The plasma THC is either not working properly or the operator has not been trained on how to use the equipment. In either case the shop is not getting the most out of its cutting operation.
There are a variety of torch height control systems, or “standoff controls,” on the market that can be used with a variety of CNC machines. Each of these automatic THCs has a variety of functions and features, but all use the same basic motion control elements to control the position of the torch relative to the material being cut. This "torch to work" distance or "standoff" is critical to both cut quality and consumable life.
Elements of plasma torch height control
-
Motor-driven torch positioner. This device moves the torch up and down in response to signals from the control console. Screw drive, rack and pinion, and belt driven mechanisms are used to translate motion.
-
Control console. This is the brain of the system. It receives input commands from the remote control, sends output commands to the torch positioner, and monitors position feedback and voltage signals in real-time.
-
Plasma system interface. This device usually consists of a voltage divider card that is mounted inside the plasma power supply. The voltage divider card monitors power supply voltage during cutting. It "divides" the voltage signal and sends a smaller plasma voltage signal to the control console.
-
Remote control. The remote control is the HMI, or human machine interface. This is where the operator sets two critical cutting parameters: initial height and arc voltage. It may be located inside the CNC control or in a separate remote box.
The difference between IHS (initial height sensing) and voltage setting is very important to understand and is often confused.
IHS is an adjustable parameter that determines the height at which the torch will fire and begin piercing through the plate. In order to set the initial height (also called retract distance) the THC must first find the position of the plate. A variety of schemes are used for sensing the plate from simple mechanical devices, to motor stall technology, proximity sensors, and electrical circuits that sense nozzle or shield contact. Regardless of the method used, the most important thing is that the torch finds the plate and accurately retracts to the proper pierce height, whether on thick plate or thin, rusty plate or clean, above water or below.
![]() |
Figure 1 |
Correct pierce height is essential. If the torch pierces too low the consumable parts will be damaged. This is the number one cause of premature parts and torch failures (see Fig. 1). If it attempts to pierce too high, the plasma arc will not transfer, causing a misfire. The rule of thumb is to pierce at 150-200 percent of the cut height. Pierce high; cut low.
Torch to work distance
Torch to work distance distance, or standoff, during the cutting process is adjusted by monitoring and controlling the arc voltage. Note that arc voltage is the same thing as power supply output voltage. Plasma power supplies are a current source—they generate a very steady operating current when the torch is cutting.Voltage, on the other hand, varies depending on the distance between the cathode (the electrode in the torch) and the anode (the material being cut). Voltage is directly proportional to resistance (Ohms Law states that V=I*R). The resistance in the arc is a function of the distance. When the torch to work distance increases the voltage goes up; when the torch-to-work decreases the voltage goes down.
The torch height control uses arc voltage to maintain a consistent distance from the plate while the torch is cutting. This allows the system to maintain proper torch height regardless of variations in the material, or flatness of the cutting bed. The operator sets the arc voltage on the remote control according to the cut charts in the plasma system's operations manual. This voltage setting is usually between 100 and 200 VDC.
After the torch height control has completed initial height sensing and the torch has pierced the plate, motion of the plasma cutting machine is enabled and the torch begins to move. Once the cutting begins, the THC starts sampling arc voltage from the power supply and comparing it to the target voltage set by the operator. It adjusts the torch up or down to maintain that target voltage.
Each voltage setting corresponds to a specific height that optimizes the arc characteristics for a clean, straight cut. Torch height has the greatest effect on bevel angle of the plasma cut part. Setting the voltage too high results in more material being removed from the top of the kerf than the bottom. This causes excessive top rounding and positive bevel (see Fig. 2). Setting the voltage too low results in too much material being removed from the bottom of the plate. This causes undercutting or negative bevel (see Fig. 3).
![]() |
![]() |
Figure 2 | Figure 3 |
Today's torch height controls have many features and capabilities. But the two most important to understand are initial height sensing and arc voltage control. Piercing at the right height will save you money on parts. Cutting at the right height will ensure good cut quality and minimize expensive rework operations. When properly used a torch height control pays for itself in a short time.
3 recommendations for torch height controls:
-
If your THC is broken, fix it; if it is ancient, retrofit to a new one
-
If you don't have a THC on your plasma profiling machine get one.
-
If you are buying a new machine, get the best THC you can afford. To get the most out of your investment train your operators to use all of the THC functions.
A good THC with a well-trained operator at the controls will pay for itself in improved parts life, enhanced cut quality, and decreased downtime.