Plasmaschneiden vs. Faserlaserschneiden
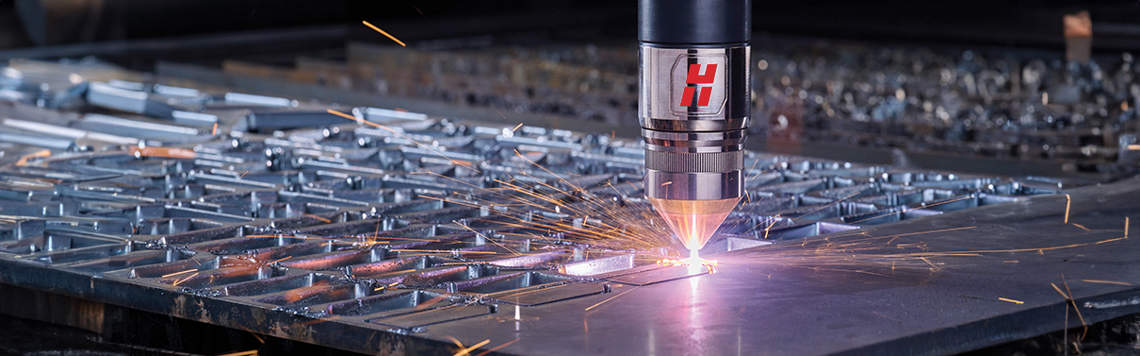
Beim Vergleich von Plasma und Laser schneidet Plasma in der Regel besser, wenn es um das Schneiden von Metall mit einer Stärke zwischen 6 mm und 50 mm geht, da es schneller ist, weniger kostet, sowohl in der Anschaffung als auch im Betrieb, und bei der Arbeit mit unvollkommenem oder reflektierendem Metall zuverlässiger ist. Darüber hinaus können mit Plasma Fasen geschnitten werden, ohne dass Nachbesserungsbedarf besteht.
Vorteile einer Wahl von Plasmaschneiden gegenüber Laserschneiden
Plasma und Faserlaser sind produktive industrielle Schneidtechniken mit Vor- und Nachteilen. Die Wahl der Technik hängt von der jeweiligen Aufgabe und den Schneidergebnissen ab, die Ihren Anforderungen am besten entsprechen. Da es sich um eine neuere Technik handelt, wird der Faserlaser manchmal als überlegen und moderner angesehen. Während Faserlaser jedoch erst seit Kurzem zum Schneiden von Metallen mit einer Stärke über Blechstärke eingesetzt werden, wurde Plasma in den letzten Jahrzehnten perfektioniert, um qualitativ hochwertige Schneidergebnisse mit geringen Anfangsinvestitionen und Betriebskosten zu erzielen. Bevor Sie auswählen, welche Technik für Ihren Betrieb geeignet ist, sollten Sie vor allem Folgendes berücksichtigen:
-
Materialstärke
-
Schnittqualität
-
Schnittgeschwindigkeiten
-
Betriebskosten
-
Anfangsinvestition
-
Zustand des Werkstücks
-
Wartung
Plasma erzeugt hervorragende Schnittqualität
Der Unterschied in der Schnittqualität zwischen X-Definition®-Plasmatechnik und Laser ist gering. Hypertherm XPR170®- und XPR300®-X-Definition-Plasma liefern bei Stärken über 16 mm eine Oberfläche, die im Allgemeinen glatter ist als bei Faserlaser und über die gesamte Lebensdauer eines Verschleißteilsatzes eine gleichbleibende Kantenqualität aufweist. In Kombination kann mit X-Definition-Plasma eine Schnittqualität erreicht werden, die mit Laser bei unlegiertem Stahl, legiertem Stahl und Aluminium durchaus mithalten kann.
Eine hilfreiche Referenz für den Vergleich der Schnittqualität der beiden Techniken ist ISO 9013, eine internationale Norm zur Klassifizierung der Qualität von Teilen, die mit einem thermischen Verfahren geschnitten wurden. Die ISO 9013 klassifiziert die Winkligkeit eines Verfahrens – ein Maß für die Abweichung von der Senkrechten – in Bereichen von 1 (geringste Abweichung) bis 5 (größte Abweichung). Mit einer Schneidmaschine, die überragende Bewegungsmöglichkeiten bietet, liefert X-Definition Plasma Schnitte nach ISO Bereich 2 bei Material mit einer Stärke von weniger als 10 mm bzw. Schnittqualität nach Bereich 3 bei dickerem Material.
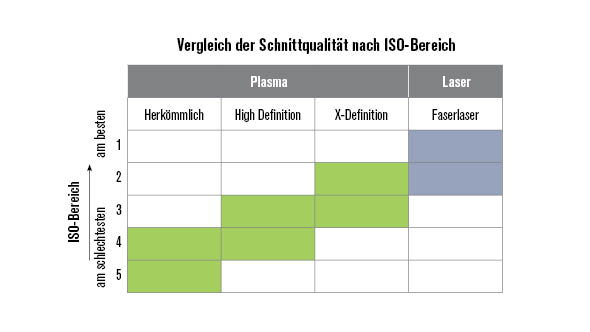
Plasma schneidet schraubenfertige Löcher und schweißfertige Fasen
In Verbindung mit einer CAD/CAM-Software wie ProNest® können die Arbeitskosten und nachgelagerten Engpässe drastisch reduziert werden. Anwendungen der SureCut™-Technik sorgen durch die Einbettung von Plasmawissen und Prozessparametern für hochwertige Schneidergebnisse – und verringern gleichzeitig den Konfigurations- und Testaufwand. Dies reduziert die komplexe Programmierung, das Ausprobieren und das Eingreifen des Bedieners.
Hier erfahren Sie, wie SureCut-Prozesse zur Maximierung der Hypertherm-Plasmaleistung beitragen:
-
True Hole® erzeugt detailliertere und definiertere Löcher mit weniger Abschrägungen und minimalen Ein- und Ausfahrtspuren. True Hole erstellt schraubenfertige Löcher direkt auf dem Plasmatisch, wodurch das Bohren von Löchern in einem separaten Schritt überflüssig wird.
-
True Bevel™ wendet automatisch die richtigen Schneidparameter an, sodass Bediener abgeschrägte Kanten in einem Durchgang schneiden können, ohne dass ein zweiter Schritt erforderlich ist – was bei den Techniken der Mitbewerber oft der Fall ist. Die Schweißer müssen die gefasten Kanten nicht mehr manuell auf einen bestimmten Winkel schneiden oder schleifen.
-
Rapid Part™ zielt auf Prozessschritte ab, die als nicht wertschöpfend gelten, und optimiert diese. Dazu gehört auch die Zeit, die der Plasmabrenner für den Rückzug und die Positionierung benötigt, sowie weitere Schritte wie die Gasvorströmung. Durch die Verkürzung oder das Wegfallen der Nebenzeiten können die Bediener mehr Teile in der gleichen Zeit schneiden – in manchen Fällen sogar doppelt so viele!
-
Plate Saver™ kombiniert die XPR®-Lichtbogenstabilität und spezielle Softwareparameter zur deutlichen Steigerung der Materialausnutzung.
Lasertoleranzen gehen mit Kostenkompromissen einher
Der Unterschied zwischen Plasma- und Lasertoleranzen ist geringer als Sie vielleicht denken – er beträgt nämlich etwa 0,25 mm, das ist etwa die Stärke einer Visitenkarte. Wie in diesem Artikel über Lasertoleranzen beschrieben, sind zusätzliche Toleranzen oft mit Kostenkompromissen verbunden. Die Schnittfugenbreite eines Faserlasers ist zwar vorteilhaft, kann sich aber beim Schneiden dickerer Metalle negativ auf den Produktionsfluss auswirken. Eine dünne Schnittfuge kann nämlich dazu führen, dass sich Teile leicht verklemmen und sich nicht vom Skelett lösen, was Ihren Produktionsfluss verlangsamt und ein Eingreifen des Bedieners erfordert.
Plasma ist schnell
Insbesondere beim Schneiden von Metallen über 16 mm Stärke schneidet Plasma schneller als Faserlaser. Dies führt zu höherer Produktivität, weniger Engpässen, besserer Termintreue und somit zu höherem Cashflow und Potenzial für Unternehmenswachstum.
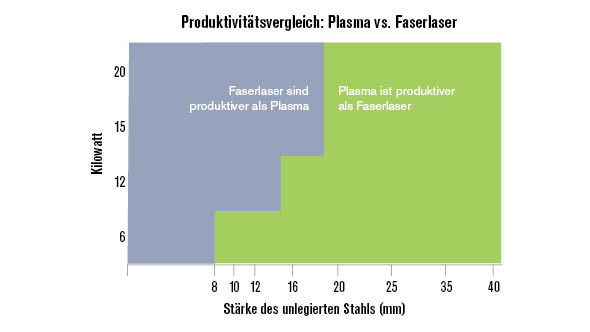
Geringere Kosten mit Plasma
Die Kosten für Ihre Schneidarbeiten hängen von vielen Faktoren ab, z. B. von Gas, Strom, Verschleißteilen, Wartung, Arbeit, Ausschuss sowie den Anfangsinvestitionen für die Maschinen. Im Idealfall liefert Ihre Schneidanlage gleichbleibende Ergebnisse über die gesamte Lebensdauer der Verschleißteile hinweg und ermöglicht somit eine geringe Abweichung von Teil zu Teil bei einer Reihe von Metallarten und -stärken, wodurch der Ausschuss und die Kosten der Fertigteile verringert werden.
Betrachtet man die direkten Betriebskosten eines Schneidvorgangs, so kostet Plasma bei dickeren Metallen aufgrund verfeinerter Prozesse und eines geringeren Gasverbrauchs oft weniger pro Meter. Auch wenn die direkten Betriebskosten des Faserlasers niedriger sind, wie z. B. bei dünnen Metallen, sollten Sie unbedingt den Stromverbrauch und den Gasverbrauch des Faserlasersystems berechnen. Die Kunden sind oft schockiert über den hohen Energieverbrauch und die Notwendigkeit, Massengasspeicher zu installieren oder Stickstofferzeugungsanlagen zu erwerben.
Die Anfangsinvestition in eine Plasmaschneidmaschine ist in der Regel zwei- bis fünfmal geringer als bei einer Faserlaser-Schneidanlage. Das mag zwar wie eine einmalige Ausgabe erscheinen, aber die Abschreibungskosten in der Gewinn- und Verlustrechnung Ihres Unternehmens werden die Gesamtbetriebskosten (TCO) Ihres Faserlasersystems in den nachfolgenden Jahren erheblich erhöhen. Sofern Ihre Faserlasermaschine nicht bei hoher Auslastung schneidet, ist es unwahrscheinlich, dass sich Ihre Investition amortisiert.
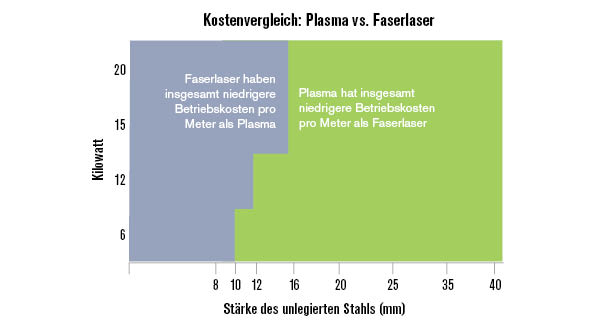
Plasma ist vielseitig
Plasma ist sehr unempfindlich gegenüber dem Zustand des zu schneidenden Metalls. Unabhängig davon, ob das Metall oxidiert oder lackiert ist oder je nach Schnittart eine variable Stärke aufweist, führt Plasma den Schnitt zuverlässig aus. Bisher war es für das Schneiden mit dem Laser erforderlich, dass die Platte eine bestimmte Qualität aufweist, im Inneren gelagert wurde und/oder vor dem Schneidvorgang gereinigt wird. Die Fähigkeit des Lasers, mit diesen ungünstigen Materialbedingungen umzugehen, wird zwar immer besser, erfordert aber in der Regel zusätzliche Bearbeitungsschritte, wie z. B. eine Breitstrahlverdampfung, wodurch sich die Prozesszykluszeiten verlängern.
Plasma ist robust und zuverlässig
Immer wieder berichten Kunden, dass die wichtigsten Eigenschaften von Plasma seine Einfachheit, Robustheit und Zuverlässigkeit sind. Die Wartung ist unkompliziert, und in der Regel können die internen Wartungsabteilungen alle Vorgänge bis auf die komplexesten problemlos bewältigen. In der Vergangenheit galten CO2-Laser als empfindlich. Sie waren nicht zuverlässig, und die Wartungskosten waren hoch. Faserlaser sind mit weniger Stromquellenkomponenten deutlich zuverlässiger als ältere Lasertechniken. Dennoch ist die Wartung dieser Maschinen von entscheidender Bedeutung und erfordert eine regelmäßige Inspektion, Einstellung und Wartung des Systems durch spezialisierte Techniker. Da einige Komponenten, wie z. B. ein Laserschneidkopf, mehrere zehntausend Euro kosten können, werden diese Einheiten oft ausgetauscht und zur Reparatur in einen Reinraum gebracht.
In letzter Zeit sind in vielen Regionen kostengünstige Lasersysteme auf den Markt gekommen, die das Beste aus beiden Welten versprechen: Gute Schnittqualität und geringe Anfangsinvestition. Wenn etwas zu schön klingt, um wahr zu sein, ist es das wahrscheinlich auch. Informieren Sie sich auf jeden Fall über die Kosten für den Besitz eines dieser Lasersysteme! Schlechter Service, mangelnde Zuverlässigkeit, lange Lieferzeiten für Ersatzteile und ein nicht vorhandener Kundendienst können der Preis sein, den Sie für das anscheinend so gute Geschäft zahlen.
Die oben genannten Schlüsselfaktoren sollten als "Faustregel" beim Vergleich von Plasma- mit Faserlaserschneidsystemen bis 20 kW verwendet werden. Wie bei jedem Vergleich sollten Sie vor dem Kauf die tatsächlichen Eingabedaten für die spezifische Ausrüstung, den Verwendungszweck und den Standort verwenden