Die ProNest-Software unterstützt die Einsatzbereitschaft der Craig-Fertigung, jede Herausforderung zu meistern
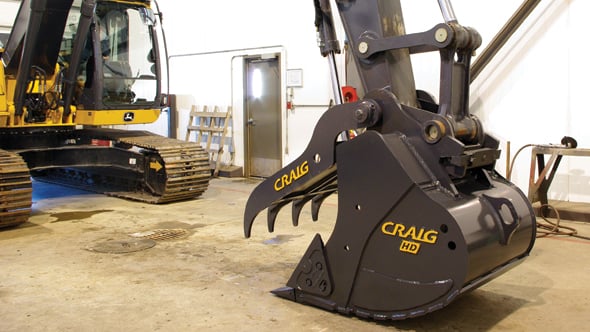
Die Firma und ihre Produkte
Craig Manufacturing in Hartland, New Brunswick, Kanada, ist der größte Hersteller von Anbaugeräten in Nordamerika, der sich in privater Hand befindet. Das Unternehmen verfügt über ein hochmodernes, 71.000 Quadratfuß großes Werk in Hartland und hat in Cambridge, Ontario, ein 15.000 Quadratfuß großes Werk für Vertrieb und Spezialfertigung hinzugefügt.
Das Problem
Mit zunehmendem Geschäft bei der Craig-Fertigung entstand der Bedarf für zusätzliche Schneidkapazität. „Unser vorhandenes Verschachtelungsprogramm hatte seine Einschränkungen. Das Erstellen von Verschachtelungen war oft ein zeitraubender Prozess. Jede Stunde, die für die Verschachtelung aufgewendet wurde, entsprach etwa einer Stunde Schneiden. „Die Software hatte keine großen Automatisierungsfunktionen, so dass wir gleich zu Beginn des Prozesses einen Engpass hatten“, sagte Operations Manager Colden Wetmore.
Die Lösung
Das Entscheidungsteam untersuchte die neuesten Hypertherm-Lösungen, einschließlich ProNest® CAD/CAM-Software. Sie waren insbesondere daran interessiert, wie ProNest mit ihrem SOLIDWORKS® 3D CAD verbunden werden konnte und wie es in ihren spezifischen Workflow passen würde. Sie wollten auch die Lochqualität verbessern, und da ProNest die True Hole® -Technologie von Hypertherm unterstützt, war dies ein zusätzlicher Bonus.
Es hat nicht lange gedauert, bis der neue EBF-Plasmatisch von Craig Manufacturing ankam. Ausgestattet mit einer HPR400XD, EDGE® Pro CNC, ArcGlide® THC und von ProNest programmiert.
„Mit unserer früheren Software haben wir sechs Jahre lang an den Schneidparametern gearbeitet und nie die richtigen erreicht“, sagte Wetmore, „und dann kommt ProNest bereits mit allen Parametern integriert auf den Markt.“
Vorteile
Statt einer Stunde Schneiden für jede Stunde Verschachtelung erhält das Unternehmen jetzt 19 Stunden – eine 19-fache Produktivitätssteigerung! Durch die verbesserte Lochgenauigkeit und -qualität der True Hole-Technologie konnten die sekundären Schleifarbeiten erheblich reduziert werden.
Wetmore fügt hinzu: „Seit wir den neuen Tisch installiert haben, der die Rapid Part™-Technologie beinhaltet, konnte selbst unser sehr erfahrener Bediener nicht mit den erhöhten Anforderungen an das Laden und Entladen der Platten mithalten. Wir mussten dafür erst unseren Ablauf ändern.“Sie erlebten auch eine verbesserte Materialnutzung. „Wir haben unseren Rohmaterialbestand um die Hälfte reduziert. Heute ist unser Management dank ProNest zufriedener, da das in Platten gebundene Geld reduziert wurde, ohne die Lieferung zu beeinträchtigen.“