X-Definition-Plasma löst häufig auftretende Probleme bei der Fertigung von Baustahl
Neuseeländischer Hersteller findet den Weg zum Erfolg über eine Drei-Wege-Partnerschaft
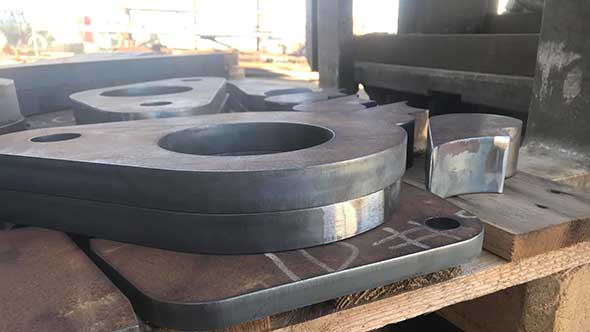
Baustahl ist einer der am häufigsten verwendeten Baustoffe des Jahrhunderts und wird oft als einer der wichtigsten Komponenten der modernen Architektur betrachtet. Da diese Komponenten einen direkten Einfluss auf die Standsicherheit von Gebäuden haben, wurden die gesetzlichen Bestimmungen von den zuständigen Aufsichtsbehörden im Laufe der Jahre angepasst, um die Sicherheit der Bewohner gewährleisten. In manchen Ländern sind größere, stärkere und schwerere Baustahlteile jetzt die Norm. Das bedeutet wiederum, dass die Verarbeiter die richtige Schneidausrüstung für die Handhabung dieser Materialien benötigen.
Der neuseeländische Metallverarbeiter GH Engineering hatte erkannt, dass Schnittqualität und Produktivität wichtige Faktoren waren, die beim langfristigen Erfolg des Unternehmens eine wesentliche Rolle spielten. Das in Palmerston North ansässige Unternehmen verfügt über mehr als zehn Jahre Erfahrung bei der Fertigung von Baustahl und Metallteilen für das Baugewerbe und beliefert die Baustahl- und Baubranche mit Komponenten.
Änderungsbedarf erkennen
Mit der zunehmenden Nachfrage nach Baustahlteilen verzeichnete GH Engineering auch einen entsprechenden Anstieg bei Aufträgen für größere, schwere Metallplatten. Das Unternehmen hatte zwar bereits ein Hypertherm Powermax105®-Plasmagerät von Hypertherm Associates auf einem Schneidtisch für leichte industrielle Anwendungen, doch diese Ausrüstung konnte seine Anforderungen jetzt nicht mehr erfüllen. Er war einfach zu klein. Das Unternehmen musste deshalb einige seiner größeren 2D-Teile auf einer für 3D-Teile ausgelegten Bohranlage für Träger schneiden, und den Rest auslagern. Neben den zusätzlichen Kosten hatte das Team durch die Auslagerung auch weniger Kontrolle über die Produktion, was sich stets auf die Projektzeitpläne auswirkte.
Aus diesen Gründen kam GH Engineering zu dem Schluss, dass eine Investition in einen neuen Plasmaschneidtisch seine Probleme lösen würde. Das Team erstellte dann eine Vorauswahl der verschiedenen Möglichkeiten, mit denen es seine Kapazität im eigenen Haus erweitern und gleichzeitig die Arbeitsabläufe verbessern konnte.
Die Lösung: moderne Plasmaschneidtechnologie
Bei der Beurteilung der verschiedenen Möglichkeiten musste GH Engineering mehrere wesentliche Faktoren berücksichtigen, die in der Baustahlbranche und im Baugewerbe die wichtigste Rolle spielten. Zu den wichtigsten Faktoren zählten die Schneidtoleranzen innerhalb akzeptabler Bereiche, eine beständige Schnittqualität, die Laufzeit der Produktion und die Kapitalrendite.
GH Engineering wandte sich an Plazmax® Technologies – einem Hersteller von CNC-Lösungen für das Profilschneiden, der ausschließlich Hardware und Software von Hypertherm anbietet – um sich einige seiner modernen automatisierten Lösungen anzusehen.
Plazmax erkannte die Anforderungen von GH Engineering sofort und gab eine radikale Empfehlung ab. Sein Vorschlag lautete, dass das Unternehmen eine Hypertherm X-Definition Plasmaanlage – ebenfalls von Hypertherm Associates – in Erwägung zieht, da diese das Geschäft des Metallverarbeiters zukunftssicher gestalten würde. GH Engineering befolgte den Rat und investierte schließlich in das Plazmax CutPro HS-System, in das die folgenden Produkte von Hypertherm Associates integriert sind: die Plasmaanlage X-Definition XPR300®, das EDGE® Connect CNC-System und die ProNest®-CAD/CAM-Software. Mit dieser integrierten Lösung konnte der Metallverarbeiter seine Kapazität und Leistungsfähigkeit sowie die Dienstleistungen, die er seinen Kunden anbieten konnte, wesentlich erweitern.
„Wir haben uns auf ein Wagnis eingelassen und uns für die Investition in den größeren Plazmax CutPro HS-Schneidtisch mit der XPR300-Plasmaanlage entschieden“, erläuterte Gary Hobbs, Geschäftsführer von GH Engineering. „Anfangs dachten wir zwar nicht, dass wir eine so große Anlage brauchen. Wir waren im Endeffekt aber froh, weil wir damit nicht nur unsere aktuellen Aufträge abwickeln können, sondern langfristig auch für schnellere, größere und längere Schneidaufträge ausgestattet sind.“
Seit der Einführung der neuen Plasmaschneidanlage kann GH Engineering jetzt alle Aufträge im eigenen Haus ausführen und dabei die strengen Anforderungen der Kunden erfüllen. Das Produktionsteam spart jetzt die Zeit und den Aufwand für den Transport von 15 bis 40 Tonnen Material zum und vom Standort der externen Vertragsfirma und kann seine ältere Bohranlage für Träger jetzt für die Verarbeitung von 3D-Teilen verwenden, für die sie ausgelegt ist.
.
Befriedigende und gewinnbringende Ergebnisse
Das Unternehmen kann jetzt stärkere Metallplatten handhaben und Platten aus unlegiertem Stahl mit einer Stärke von 50 bis 60 mm mit einer gleichbleibend guten Schnittqualität liefern. GH Engineering nutzt das in die ProNest-Software integrierte Vorlochstech-Verfahren von Plazmax, um die ursprüngliche 50-mm-Lochstechkapazität der XPR300 zu erweitern. GH Engineering kann jetzt sogar hervorragende Ergebnisse beim Lochstechen von Löchern bis zu 70 mm erzielen.
Der neue Schneidtisch ist auch mit einer Reihe von Technologien ausgestattet, die unter der Bezeichnung SureCut™ zusammengefasst werden. Darin sind die besten Funktionen von Hypertherm Associates und Plazmax integriert und es wird damit eine Synergie geschaffen, die die Schneidergebnisse optimiert. In der Maschine wurden der spezielle Fasenkopf von Plazmax und die True Bevel®-Technologie von Hypertherm kombiniert, sodass das Produktionsteam jetzt die zeitaufwändige Eingabe von Fasenschneid-Parametern überspringen und genaue und einheitliche abgefaste Kanten in einem einzigen Schritt erstellen kann. Dazu ist die Maschine mit Hypertherm True Hole®-Technologie ausgestattet, die ein besseres Lochschneiden von Schraubenlöchern ermöglicht. Außer den zusätzlichen Schneidparametern von Plazmax kann GH Engineering jetzt auch Löcher mit einer Stärke von bis zu 50 mm in unlegiertem Stahl schneiden.
Zusätzlich zu den Verbesserungen bei der Hardware stellt Plazmax jetzt auch sein im eigenen Haus entwickeltes Bedienfeld Soft OpCon (Operators Console – Bedienerkonsole) für die EDGE Connect CNC-Software bereit. Dieses ermöglicht eine einfache Positionierung der Maschine, die Fernanzeige des Schneidvorgangs durch den Bediener und eine Ferndiagnose durch Plazmax.
Wirkungsvolle Partnerschaft soll erweitert werden
GH Engineering konnte seine Produktionszeit erheblich verkürzen, den Durchsatz erhöhen und seine Rentabilität steigern.
Brad Johnston, Product Development Manager bei Plazmax Technologies, beschrieb die Ergebnisse der Partnerschaft wie folgt: „Durch das gute Zusammenspiel der einzelnen Technologien wurde die Kapazität und Leistungsfähigkeit von GH Engineering erweitert. Bei der längeren Standzeit der Verschleißteile ist es kein Wunder, dass die Maschine länger in Betrieb bleiben kann und Aufträge dadurch viel schneller erledigt werden können.“
Brad Johnston, Product Development Manager
Plazmax Technologies
Die neue Kapazität und Leistungsfähigkeit von GH Engineering hat sich aufgrund der ausgezeichneten Qualität und der höheren Produktivität sowohl im privaten als auch im öffentlichen Sektor herumgesprochen. Das Unternehmen hat sein Geschäftsmodell jetzt auch durch Schneidarbeiten für andere Baustahlfirmen auf der Nordinsel Neuseelands erweitert. Dazu haben alle der oben aufgeführten Vorteile eine hervorragende Kapitalrendite erzielt, sodass sich die Investition in die Maschine innerhalb eines Jahres amortisiert hat.
Das Unternehmen hat auch eine gute Beziehung mit den Mitarbeitern von Plazmax und Hypertherm Associates aufgebaut. Diese Drei-Wege-Partnerschaft soll im Rahmen der Zusammenarbeit noch weiter vertieft werden, um das Anwendererlebnis zu verbessern und weitere Geschäftsziele für GH Engineering zu erreichen.
Über GH Engineering Ltd
GH Engineering ist ein metallverarbeitendes Unternehmen mit Sitz in Palmerstone North in Neuseeland. Es wurde im August 2007 gegründet, ist hauptsächlich im Baugewerbe und in der Baustahlbranche tätig und liefert hochwertige Baustahlkomponenten mit anspruchsvollen Toleranzen, die die Normen des Landes für Anwendungen im Baugewerbe erfüllen.
Über Plazmax Technologies
Plazmax Technologies wurde ursprünglich unter dem Namen „CNC Engineering Solutions“ gegründet und ist seit 2011 im Bereich CNC tätig. Am Anfang wurde ein Service für die Konstruktion von Maschinen und Teilen sowie die Fertigung mit CNC-Fräsmaschinen angeboten. Die Geschäftsplanung sah jedoch immer vor, einen Bedarf im Markt zu ermitteln und ein Produkt unter unserer eigenen Marke herzustellen. Unsere Kriterien lauteten, dass das Produkt technische Elemente aufweisen musste, die unsere bestehenden Kompetenzen nutzen und herausfordern würden. Weitere Informationen finden Sie unter www.plazmax.com.au.