Wie Powermax SYNC® die Art und Weise, wie Sie arbeiten, verändern wird
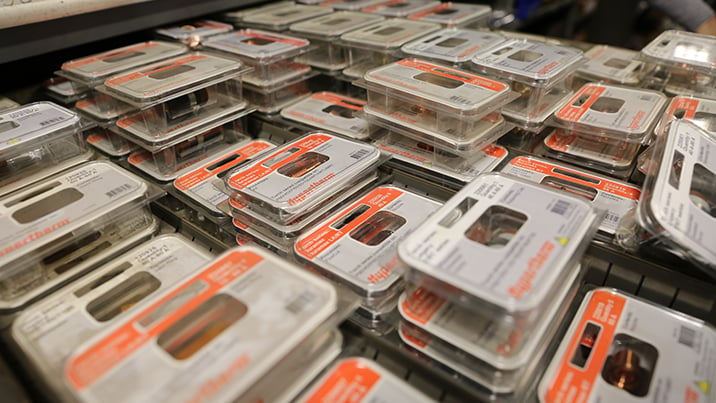
Kürzlich haben wir erörtert, welche Vorteile patronenbasierte Verschleißteile für den Endverbraucher haben, da sie einen einfacheren, sichereren und leichter zu handhabenden Austausch von Verschleißteilen ermöglichen.
Innovative Verschleißteile sind jedoch nur ein wichtiges Element der neuen Powermax SYNC®-Serie. Als wir anfingen, über die Zukunft von Powermax Plasma nachzudenken, wollten wir unsere Geräte komplett neu konzipieren, um die häufigsten Probleme unserer Kunden zu lösen. In Gesprächen mit unseren Kunden kristallisierten sich drei Themen heraus:
-
Sowohl große als auch kleine Unternehmen haben Schwierigkeiten, Arbeitskräfte zu finden, geschweige denn Fachkräfte, die wissen, wie man mit Plasma schneidet.
-
Unternehmen stehen unter starkem Druck, ihre Kosten zu senken und die Produktivität zu steigern.
-
Unternehmen brauchen eine Möglichkeit, die laufenden Arbeiten zu überwachen, damit sie Probleme schnell erkennen und beheben können, bevor sie eskalieren und die Kosten nach oben treiben.
Die brandneue Powermax SYNC®-Serie von Hypertherm wurde entwickelt, um alle drei dieser Probleme zu lösen.
Problem 1: Es ist unmöglich, qualifizierte Arbeitskräfte zu finden.
Lösung: Entwicklung eines Plasmaschneidergeräts, das so einfach zu bedienen ist, dass keine Schulung erforderlich ist.
Wie wir in unserem letzten Blog beschrieben haben, ist der Powermax SYNC® unglaublich intuitiv und einfach zu bedienen. Anstelle von fünf separaten Verschleißteilen benötigen diese Geräte nur eines: ein einteiliges Einsatz-Verschleißteil, das in weniger als 10 Sekunden zu installieren ist. Die Unternehmen müssen keine Zeit damit verbringen, neuen Mitarbeitern beizubringen, wie sie die richtigen Verschleißteile identifizieren, in der richtigen Reihenfolge zusammenbauen und ordnungsgemäß am Brenner installieren.
Das neue einteilige Einsatz-Verschleißteil von Hypertherm ist farbcodiert, so dass die Bediener schnell die richtige Kartusche für die anstehende Arbeit auswählen können. Insgesamt gibt es vier Farben: gelb für handgeführtes Schneiden, grau für mechanisiertes Schneiden, grün für Fugenhobeln und schwarz für Spezialanwendungen wie Bündigschneiden und Schneiden mit großer Reichweite.
Ein weiterer Vorteil der Einsatz-Verschleißteil-Plattform ist die Verschleißrate. Die Komponenten eines herkömmlichen fünfteiligen Stapels verschleißen nicht gleichmäßig. Elektrode und Düse nutzen sich am schnellsten ab, die Brennerkappe am langsamsten. Dies erhöht die Komplexität und den Schulungsaufwand, da die Unternehmen neuen Bedienern beibringen müssen, wie sie verschlissene Verschleißteile überprüfen und austauschen können. Das neue Einsatz-Verschleißteil von Hypertherm ist speziell für eine gleichmäßige Abnutzung der Komponenten ausgelegt, wodurch Schulungen, Abfall und Ausfallzeiten weiter reduziert werden.
Darüber hinaus ist in dem Einsatz ein RFID-Chip integriert. Dieser Chip kommuniziert mit dem Brenner und der Stromversorgung, um sicherzustellen, dass die Geräteeinstellungen mit dem Einsatz übereinstimmen. Wenn Sie einen 65-Ampere-Schneideinsatz installieren, ändert das Gerät die Stromstärke auf 65 Ampere, stellt automatisch den Luftdruck ein und geht in den Schneidmodus über. Dies verringert nicht nur den Schulungsaufwand, sondern schließt auch Bedienungsfehler aus.
Als Bediener brauchen Sie sich keine Gedanken darüber zu machen, ob Sie das falsche Teil greifen, die Verschleißteile in der richtigen Reihenfolge einsetzen oder den Brenner richtig montieren. Als Unternehmer müssen Sie nicht viel Zeit aufwenden, um neue Mitarbeiter zu schulen – etwa um zu erklären, was die Verschleißteile sind, wie man die richtigen auswählt, wie man sie in die richtige Reihenfolge bringt und korrekt auf den Brenner schraubt.
Problem 2: Die Kosten steigen schneller als die Produktivität.
Lösung: Entwicklung eines effizienteren Plasmaschneidgeräts, das es den Bedienern ermöglicht, mehr Arbeit in kürzerer Zeit zu erledigen.
Ein geringerer Zeitaufwand für die Schulung neuer Mitarbeiter trägt sicherlich zur Produktivitätssteigerung bei, aber Powermax SYNC® fördert die Produktivität auch auf andere Weise.
Zum einen halten die Einsatz-Verschleißteile beim manuellen Schneiden bis zu doppelt so lange und sie bieten beim Einsatz eines Maschinenbrenners auch eine bessere Schnittqualität. Das bedeutet weniger Zeitaufwand für den Austausch von Verschleißteilen und die Nachbearbeitung von Teilen. Und denken Sie daran, wie viel einfacher das Bestell- und Bestandsmanagement sein wird, wenn Sie nur noch ein Teil – statt fünf – im Auge behalten müssen.
Der Wechsel Ihrer konventionellen Plasmaverschleißteile kann kostspielig und verwirrend sein, was zu erhöhten Lagerkosten und Bedienerfehlern führt.
Der automatische Einrichtungsprozess und der farbcodierte Einsatz tragen ebenfalls dazu bei, Fehler zu vermeiden, die oft zu schlecht geschnittenen Schneidteilen und mehr Nacharbeit führen. Da die Möglichkeit von Bedienerfehlern ausgeschlossen ist, wird die Produktivität bereits erheblich verbessert. Kurz gesagt, Powermax SYNC® verbessert die Produktivität, indem die nicht wertschöpfende Arbeit erheblich reduziert, wenn nicht sogar eliminiert, wird.
Powermax SYNC® hilft auch in anderer Hinsicht – der Brenner verfügt über eingebaute Bedienelemente, mit denen der Bediener beispielsweise die Stromstärke einstellen und den Brenner ein- und ausschalten kann, ohne zur Stromversorgung zurückzukehren. Dies ist ein weiteres Beispiel für die Beseitigung nicht wertschöpfender Zeit. Wenn Sie z. B. auf einer Leiter arbeiten oder Ihr Gerät unter einer Werkbank verstaut haben, können Sie Zeit sparen, indem Sie das Gerät direkt am Arbeitsplatz einstellen.
Problem 3: Probleme häufen sich schnell und sorgen so für vermeidbare Kosten.
Lösung: Entwicklung eines Plasmaschneidergeräts, das hilfreiche Daten liefert, damit die Bediener Probleme frühzeitig erkennen können.
Wie bereits erwähnt, ist der Powermax SYNC®-Einsatz mit einem RFID-Chip ausgestattet. Dieser Chip kommuniziert mit dem Brenner und der Stromversorgung, um automatisch sicherzustellen, dass die Geräteeinstellungen korrekt sind. Dieser Chip hat jedoch noch eine andere Aufgabe: die Erhebung von Nutzungsdaten.
Das Powermax SYNC®-Gerät erfasst Informationen wie Lichtbogeneinschaltzeit, Lichtbogenübertragungsrate, Luftdruck usw., während Sie es benutzen. Die Daten zur Einsatznutzung können mit dem speziellen Einsatzlesegerät und der App angezeigt und in ein Dashboard importiert werden, in dem die Benutzer alle Nutzungsmuster und -trends verwalten, vergleichen und erkennen können. Diese Daten können Ihnen helfen, Probleme frühzeitig zu erkennen, bevor die Lebensdauer der Verschleißteile beeinträchtigt wird. Wenn Sie etwa wissen, dass Ihre Lichtbogenübertragungsrate normalerweise 85 Prozent beträgt, diese dann aber abfällt oder Sie feststellen, dass Sie plötzlich weniger Starts haben, dann wissen Sie, dass etwas nicht stimmt.
Das haben wir bei unseren Feldversuchen immer wieder festgestellt. Wir hatten zum Beispiel einen Kunden, der bemerkte, dass die Lebensdauer des Einsatzes nachts kürzer war. Nach der Analyse der Daten fanden wir heraus, dass es daran lag, dass die Außentemperatur nachts niedriger war, was wiederum den Luftstrom zum Gerät beeinträchtigte. Dieser Kunde musste lediglich den Luftstrom leicht erhöhen, und die Lebensdauer des Einsatzes war wieder normal.
Derselbe Kunde entdeckte auch, dass einige Bediener häufiger als andere den Brenner zündeten, ohne den Lichtbogen zu übertragen. Das Programm war in der Lage, die Bediener zu coachen und die Lebensdauer der Verschleißteile zu beeinflussen. Vor Powermax SYNC® waren derartige Erkenntnisse nicht möglich.
Zusammenfassend lässt sich sagen, dass Powermax SYNC® Unternehmen durch seine Benutzerfreundlichkeit, die Reduzierung von Abfall und die intelligente Datenerfassung helfen kann, häufige Probleme zu lösen. Deshalb sind wir zuversichtlich, dass diese neue Serie und die Plattform für Verschleißteile nach jahrelanger Entwicklung einen Mehrwert bieten und Ihre Arbeitsweise verändern werden.