Investieren Sie in die Schnittqualität: Hypertherm Powermax
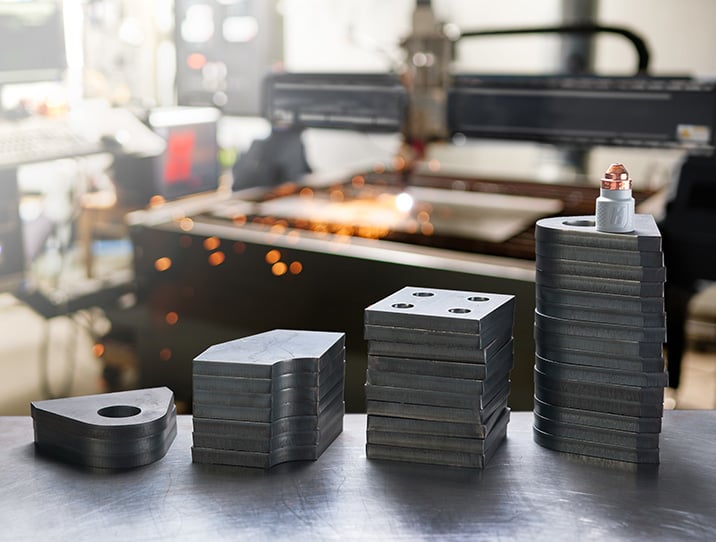
Es gibt viele Gründe, warum Kunden sich für die Investition in einen Powermax®-Plasmaschneider entscheiden, aber einer der wichtigsten ist die konstante Schnittqualität, die er liefert. Ganz egal, ob die Schnitte mit einem Handplasmabrenner, einem CNC-Maschinenbrenner oder einem Robotikbrenner durchgeführt werden – die Schnittqualität einer Powermax ist deutlich besser als bei Konkurrenzprodukten, und zwar nicht nur, wenn die Brenner-Verschleißteile oder der Einsatz neu sind, sondern auch noch nach stundenlangem Einsatz! Diese gleichbleibend hohe Schnittqualität hat enorme Auswirkungen auf die Verringerung oder den Wegfall von Nachbearbeitungen, wie z. B. Schleifen, was wiederum die Betriebskosten des Kunden senkt und seine Produktivität erhöht. Das Erreichen dieses Leistungsniveaus mit einer Powermax beginnt mit der Entwicklung und Prüfung von Verschleißteilen und Einsätzen, die für die Schneidanwendung des Kunden optimiert sind.
Schneidleistungsmetriken
Die Schnittqualität bezieht sich auf die Winkligkeit der Schnittkanten, die Kantenbeschaffenheit oder -rauhigkeit und den anhaftenden Bart. Neben der Schnittgeschwindigkeit, der Schnitthöhe und der Gasart haben viele Aspekte der Plasmaschneidanlage Einfluss auf die resultierende Schnittqualität. Die Brenner-Verschleißteile oder die Einsatz-Konstruktion und deren Betrieb spielen eine entscheidende Rolle bei der Bestimmung der Schnittqualität.
Das Engagement von Hypertherm Associates für Schneidinnovationen ermöglicht eine kontinuierliche Verbesserung der Schnittqualität. Unser Forschungs- und Entwicklungsteam bewertet die Schnittqualität mit neuen und gebrauchten Verschleißteilen. Wir haben Testverfahren entwickelt, mit denen sich die Schnittqualität quantifizieren und nachverfolgen lässt, während sich die Verschleißteile mit der Zeit abnutzen.
Messung der Powermax-Plasmaschnittqualität
Die Schnittqualität von Powermax-Plasmageräten wird mit modernsten Messgeräten wie Koordinatenmessgeräten (CMM) und Oberflächenrauhigkeitsmessgeräten (Profilometern) sowie mit statistischen Werkzeugen und ISO-Normen bewertet. Zur Messung der Qualität der Schnittfläche werden Koordinatenmessgeräte eingesetzt.
Zur Messung der Qualität der Schnittfläche werden Koordinatenmessgeräte eingesetzt.
Robustheit der Schnittqualität und Entwicklung der Verschleißteile
Während der Entwicklung wird die anfängliche Schnittqualität bewertet, indem mehrere 7,6 x 7,6 cm große Stahltestplatten geschnitten, die Schnittqualität gemessen und mit strengen Qualitätsstandards verglichen werden. Die primären Kantenmerkmale, die bewertet werden, sind der Kantenwinkel, die Geradheit der Schnittkanten und die Rundheit der Oberkante – Abweichungen von Seite zu Seite – sowie die Oberflächengüte. Wir befolgen die Normen der ISO 9013 für modernste Qualitätsbestimmung.
Ein wichtiger Aspekt bei der Entwicklung von Verschleißteilen und Einsätzen ist die Robustheit der Schnittqualität, da sich die Verschleißteile im Laufe ihrer Lebensdauer abnutzen. Diese Kennzahl für die Entwicklung von Verschleißteilen und Einsätzen wird als „Schnittqualität während der gesamten Lebensdauer“ bezeichnet. Ingenieure bewerten die Schnittqualität, indem sie alle 30 Minuten (Plasmalichtbogenzeit) Stahltestplatten schneiden, bis das Verschleißteil aufgebraucht ist.
Lochstech-Robustheit und Bewertung
Verschleißteile und Einsätze für das Plasmaschneiden sind für das Lochstechen (Durchschneiden) bis zu einer bestimmten Stärke ausgelegt. Die Entwicklung von Verschleißteilen und Einsätze, die mehrere Male dickes Material lochstechen können, ist einfach. Unser Lochstechprotokoll erfordert jedoch das 300-malige Lochstechen der Nennstärke auf einem Schneidtisch. Unsere Ingenieure konzipieren Verschleißteile und Einsatzteile sowie den Gasfluss, um diese anspruchsvollen Designspezifikationen zu unterstützen.
Beispiel einer der Lochstech-Testplatten.
Analyse der Übertragungshöhe und der Längenzunahme des Lichtbogens
Powermax-Plasmageräte werden in vielen verschiedenen Anwendungen eingesetzt, einschließlich solcher, die große Übertragungs- und Lichtbogendehnungshöhen erfordern (z. B. Fugenhobeln, Schneiden in Bereichen mit eingeschränktem Zugang und Anwendungen mit bündigen Schnitten).
Wir stellen strenge Anforderungen, um eine große Übertragungshöhe und Längenzunahme des Lichtbogens zu erreichen. Die Powermax-Stromquellenarchitektur, Steuerungsschemata, Verschleißteile und Einsätze müssen gemeinsam entwickelt werden, um branchenführende Leistung zu bieten.
Wir entwickeln die Schnittqualität hauptsächlich für unlegierten Stahl, legierten Stahl und Aluminium. Unsere Kunden nutzen jedoch unsere Schneidgeräte, um je nach Werkstück unterschiedliche Metalle und Legierungen zu formen.
Der Vorteil des Powermax-Einsatzes
Der Powermax SYNC®-Einsatz-Verschleißteil-Plattform präsentierte einen einteiligen Einsatz, der branchenführende Schneidleistung bietet. Dies ist möglich, weil die Hypertherm-Ingenieure die einzelnen Teile des Einsatzes (z. B. Elektroden, Wirbelringe, Düsen und Schutzschilde) so angepasst haben, dass sie die von den Benutzern gestellten Schneiderwartungen erfüllen und sogar übertreffen. Jeder Einsatz wurde sorgfältig entworfen, indem die anfängliche Schnittqualität, die Qualität über die Lebensdauer, die Lochstech-Bewertung, die längere Lebensdauer der Verschleißteile und andere Anforderungen an die Konstruktion bewertet wurden.
Jedes Mal, wenn ein Benutzer einen Powermax-Einsatz montiert, sind die Komponenten neu. Im Gegensatz zu Konkurrenzprodukten garantieren Powermax-Einsätze von Anfang an hochwertige Schnitte und behalten die Robustheit der Schnittqualität über den größten Teil der Lebensdauer des Einsatzes bei.
Powermax SYNC mit einem Einsatz ermöglicht die Optimierung der Verschleißteile, die hervorragende Kanteneigenschaften liefern.
Die Powermax-Produktlinie wird in einer Vielzahl verschiedener Anwendungen eingesetzt. Daher wird erwartet, dass das Produkt die beste Lichtbogenstabilität, Übertragungshöhe und Lichtbogen-Längenzunahme seiner Klasse bietet. Dies wird durch die gleichzeitige Entwicklung von Verschleißteilen und Stromquellenarchitektur erreicht.
Holen Sie das Beste aus Ihrem Powermax-Plasmaschneider heraus
Um die Schnittqualitätsvorteile der Hypertherm-Verschleißteile und Einsatzkonstruktionen nutzen zu können, müssen die Kunden auch ihren Teil dazu beitragen, indem sie ihre Schneidprozesse perfektionieren. Beim handgeführten Schneiden müssen die Bediener die richtige Schneidtechnik anwenden. Dazu gehören die Aufrechterhaltung eines konstanten Brennerwinkels, um die Schnittwinkligkeit zu verringern, die Ermittlung der idealen Brennerbewegungsgeschwindigkeit zur Verringerung der Bartbildung (sowohl bei hoher als auch bei niedriger Geschwindigkeit), die Verringerung der Zacken am Rand und beim Lochstechen die Verwendung der besten Methode zur Verhinderung von Schäden an Verschleißteilen oder Einsatz. Darüber hinaus müssen Bediener, die das CNC-Plasmaschneiden auf einem Plasmatisch oder mit Robotikbrennern durchführen, die richtige Brennerhöhe, Lichtbogenspannung, Vorschubgeschwindigkeit sowie Lochstechhöhe und -verzögerung einstellen. Die Wahl der richtigen Stromstärke der Verschleißteile oder Einsätze sowie des besten Plasmagases (Luft, Stickstoff, Argon oder F5) und Gasdrucks für das zu schneidende Metall ist von entscheidender Bedeutung.
Schneiden von legiertem Stahl mit Luft (links) und mit F5-Gas. Die Gasmischung aus 95 % Stickstoff und 5 % Wasserstoff verleiht den Schnitten eine silberfarbene Kante, einen guten Winkel und eine scharfe Kante. Diese Mischung wird nur für legierten Stahl empfohlen.