Wie kann ich profitabler werden?
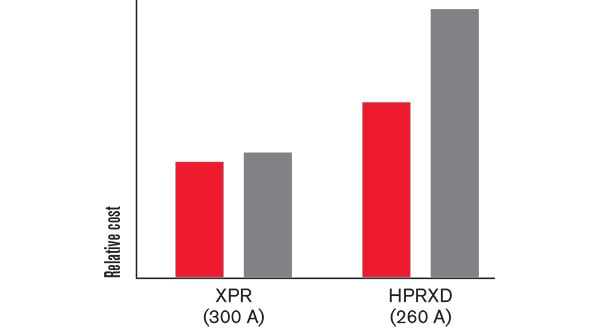
Wie ein roter Faden zieht sich die kontinuierliche Senkung der Kosten pro Meter geschnittenen Metalls durch den technischen Fortschritt beim Plasmaschneiden. Dieses Phänomen, das mit der XPR300 noch einmal deutlich Fahrt aufgenommen hat, steht hauptsächlich hinter der gestiegenen Rentabilität für den Anwender. Die enorme Verringerung der Betriebskosten beim Einsatz einer XPR300 hat mit mehreren Faktoren zu tun, darunter Schnittgeschwindigkeit, Standzeit der Verschleißteile und Schnittqualität.
Der erste Faktor hängt mit der Schnittgeschwindigkeit zusammen. Die XPR300 schneidet bei den häufigsten Materialstärken 10 bis 20 Prozent schneller als ihr Vorgängermodell und fast 50 Prozent schneller bei Materialstärken über 50 mm.
Thickness | XPR300 | HPR260XD | HPR400XD |
XPR300 |
HPR400XD versus XPR300 % |
|
15 mm | 3440 | 3130 | 3950 | 10% | 15% | |
20 mm | 2550 | 2170 | 2805 | 18% | 10% | |
25 mm | 1950 | 1685 | 2210 | 16% | 13% | |
30 mm | 1530 | 1290 | 1790 | 19% | 17% | |
40 mm | 940 | 790 | 1160 | 19% | 23% | |
50 mm | 560 | 405 | 795 | 38% | 42% | |
60 mm | 385 | 258 | 580 | 49% | 51% | |
70 mm | 250 | N/A | 380 | N/A | 52% |
Cut speed (mm/min)
Dabei muss erwähnt werden, dass die XPR300 noch effizienter arbeitet – sie benötigt für die gleiche Leistung des Vorgängermodells weniger Ampere. Wie im untenstehenden Diagramm zu sehen ist, erreicht die XPR bei 170 Ampere die gleiche Schnittgeschwindigkeit wie die HPR bei 200 Ampere Ausgangsstrom.
Ein zweiter Schlüsselfaktor für die Betriebskosten ist die Standzeit der Verschleißteile. In Labortests konnten Hypertherm-Techniker fast 50 Prozent mehr Schnitte durchführen als vorher möglich war. Während bisher mit einem Satz Verschleißteile knapp 1.000 Schnitte möglich waren, erreichen XPR-Verschleißteile bei ¾ Zoll unlegiertem Stahl fast 1.400 20-Sekunden-Schnitte. Ein Grund für diese längere Standzeit der Verschleißteile hat mit der ausgeklügelten Konstruktion der XPR zu tun. Die Stromquelle der Anlage verfügt über die sogenannte „Arc Response Technology“, die automatisch eingreift und Vorfälle verhindert, die die Anlage beschädigen oder die Standzeit der Verschleißteile beeinträchtigen könnten.
Betrachten wir zum Beispiel Fehler beim Herunterfahren. Diese Fehler, bei denen ein Lichtbogen auf unkontrollierte Weise abreißt, weil er von der Platte herunterläuft, oder weil ein inneres Merkmal (wie ein Loch oder ein Schlitz) abfällt, richten großen Schaden bei Verschleißteilen an. Das liegt daran, dass der Hafnium-Emitter an der Spitze aller Elektroden sich nicht wieder verfestigen kann, wenn ein Lichtbogen plötzlich abreißt. Dementsprechend wird jedes Mal beim Herunterfahren ein wenig Hafnium von der Elektrode abgestoßen, was die Abnutzung der Verschleißteile erhöht.
Die XPR300-Stromquelle packt dieses Problem an: Sie besitzt eine raffinierte, automatische Erkennungsfunktion. Das System erkennt, wenn ein Fehler beim Herunterfahren kurz bevorsteht und bricht den Lichtbogen auf kontrollierte Weise ab, was die Standzeit von Elektrode und Düse deutlich verlängert. Während bei den meisten Plasmaanlagen die Standzeit der Verschleißteile durch Fehler beim Herunterfahren um etwa 50 Prozent reduziert wird, beträgt diese Rate bei der XPR300 nicht einmal 10 Prozent. Das heißt, der Vorteil bei der Standzeit der Verschleißteile ist fast dreimal so hoch als üblich.
Ein weiterer wichtiger Faktor, den es zu bedenken gilt, ist die Schnittqualität. Die XPR300 eröffnet eine ganz neue Dimension des Schneidens – die X-Definition. Fortgeschrittene Technologien wie Cool nozzle™, Advanced Arc Stability, erweitertes HyDefinition-Schneiden auf Nicht-Eisenmetallen, Vented Water Injection (VWI), diskrete Gasmischung (H2, Ar, N2), Vent-to-shield und Plasma dampening, bei dem eine Kammer in der Düse Fluktuationen bei Druck und Durchfluss absorbiert, haben zu einer außergewöhnlich einheitlichen Schnittqualität über einen sehr langen Zeitraum geführt.
Während die HyPerformance-HPR-Anlagen durchgehend eine Schnittqualität im ISO-Bereich 4 bei den Teilen erreichten, kommt die XPR300 durchgehend auf ISO-Bereich 3 und bei dünneren Materialien sogar auf ISO-Bereich 2.
Hierdurch wurde die Schnittqualität bei unlegiertem Stahl deutlich verbessert, bei legiertem Stahl und Aluminium noch deutlicher. Hersteller können dadurch manche Schneidvorgänge, die bisher an externe Laser- und andere spezialisierte Schneidzentren vergeben wurden, im eigenen Haus durchführen. Dies kann erhebliche Kosteneinsparungen mit sich bringen, sowie eine verbesserte Lieferkette (mit der Möglichkeit der Just-in-time-Produktion), schnellere Auftragsabwicklung und höhere Gesamtrentabilität.
Aluminium-Kantenqualität mit
dem zum Patent angemeldeten
VWI-Verfahren, das auf der XPR300 verfügbar ist
Kantenqualität bei legiertem Stahl durch die einzigartige Fähigkeit der XPR300, H2-Ar-N2 als Plasmagas
in der OptiMix-Konsole zu mischen
Zusammengefasst führt die Kombination höherer Schnittgeschwindigkeiten, längerer Standzeit der Verschleißteile durch Schutz vor Fehlern beim Herunterfahren, verbesserte Schnittqualität und größere Einheitlichkeit beim Schneiden direkt zu geringeren Betriebskosten und höherer Rentabilität. Tatsächlich kann die XPR300 bei 300 Ampere Ausgangsleistung die relativen Kosten pro Meter Schneiden um mehr als 50 Prozent senken.