Wie kann ich produktiver werden?
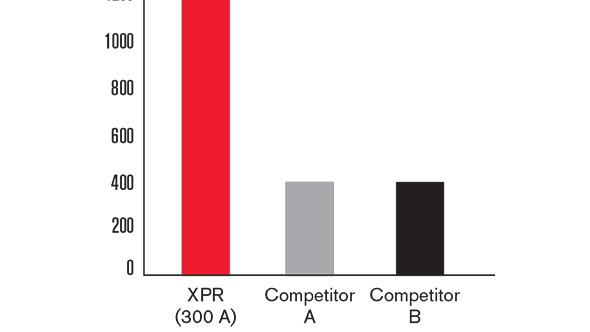
Wenn es um industrielles Schneiden geht, dann kommt es bei der Produktivität auf drei Dinge an: Schnittgeschwindigkeit, Schnittqualität und Anlagenlaufzeit. Die neue XPR300™ von Hypertherm ist bei allen drei Produktivitätsaspekten überlegen. Diese Anlage schneidet schneller, schneidet besser, sodass Nachbesserungen verringert werden (oftmals sogar eliminiert), und steigert die Anlagen-Betriebszeit durch Einsatz „intelligenter“ Technologie und zeitsparender Schritte.
Schnittgeschwindigkeit
Allein dadurch, dass sie 300 Ampere und 63 Kilowatt Leistung mitbringt, verglichen mit den 260 Ampere ihres Vorgängermodells, schneidet die XPR300 schneller. Die tatsächliche Geschwindigkeitssteigerung hängt zwar von der geschnittenen Materialstärke ab, aber im Allgemeinen können Sie bei Materialstärken von 15 bis 40 mm um 10 bis 20 Prozent schneller schneiden, beim Schneiden von 50 mm starkem Material um 38 Prozent schneller und beim Schneiden von 60 mm starkem Material um fast 50 Prozent schneller.
Thickness | XPR300 | HPR260XD | HPR400XD |
XPR300 |
HPR400XD versus XPR300 % |
|
15 mm | 3440 | 3130 | 3950 | 10% | 15% | |
20 mm | 2550 | 2170 | 2805 | 18% | 10% | |
25 mm | 1950 | 1685 | 2210 | 16% | 13% | |
30 mm | 1530 | 1290 | 1790 | 19% | 17% | |
40 mm | 940 | 790 | 1160 | 19% | 23% | |
50 mm | 560 | 405 | 795 | 38% | 42% | |
60 mm | 385 | 258 | 580 | 49% | 51% | |
70 mm | 250 | N/A | 380 | N/A | 52% |
Cut speed (mm/min)
Die XPR schneidet aber nicht nur schneller, sie arbeitet auch effizienter als die HPR260XD®. Wie im untenstehenden Diagramm zu sehen, braucht die XPR300 nur 170 Ampere für eine Schnittgeschwindigkeit, die eine HPR260XD erst bei 200 Ampere erreicht. Sie schneiden also nicht nur schneller, Sie verbrauchen dabei auch weniger Energie.
Schnittqualität
Was die Schnittqualität betrifft, eröffnet die XPR300 eine ganz neue Dimension des Schneidens – die sogenannte X-Definition™. Diese Schneidklasse verbessert die Schnittqualität gemäß der ISO 9013, einer internationalen Norm zur Definition der Schnittqualität thermisch geschnittener Teile. Diese Norm verwendet eine Skala von 1 bis 5, wobei ein Schnitt im Bereich 1 als der beste gilt. Die neue XPR bietet fast während der gesamten Standzeit der Verschleißteile eine Schnittqualität im ISO-Bereich 3. Zum Vergleich: Die HPRXD-Anlagen von Hypertherm hatten eher eine Schnittqualität im Bereich 4, wie unten dargestellt.
Auch wenn im Diagramm oben die Ergebnisse beim Schneiden von 12 mm unlegiertem Stahl wiedergegeben werden, zeigen Labortests eine Schnittqualität im ISO-Bereich 2 bei dünnerem unlegiertem Stahl und niedrigeren Stromstärken. Zusätzlich zur verbesserten Schnittqualität ist auch die Gleichmäßigkeit des Schnitts hervorzuheben. Im Diagramm ist zu sehen, dass bei Labortests mit Hunderten von 20-Sekunden-Schnitten die Schnittqualität bemerkenswert einheitlich war. Ein mit brandneuen Verschleißteilen geschnittenes Teil war optisch kaum zu unterscheiden von einem Teil, das mit Verschleißteilen geschnitten wurde, die mehr als 1.000 Starts hinter sich hatten.
Der signifikante Fortschritt in der Schnittqualität gilt für Schneiden unlegierten Stahls ebenso wie für legierten Stahl und Aluminium. Es ist das Resultat mehrerer neuer, zum Patent angemeldeter Technologien. Bei einem dieser Verfahren, „Vented Water Injection“, wird ein Stickstoff-Plasmagas mit einem Wasserschild kombiniert, um den Plasmalichtbogen besser auszurichten und zu fokussieren. Bei einem zweiten Verfahren namens „Vent-to-shield“ wird Wasserstoff aus dem belüfteten Plasmagas zurückgewonnen und mit dem Sekundärgas gemischt. Das Ergebnis dieser beiden Technologien sind rechtwinkligere Schnittkanten, geringere Winkligkeit und eine verbesserte Oberflächengüte, verglichen mit der HPR. Die XPR setzt außerdem ein Verfahren namens „Advanced Arc Stability“ ein, um den Plasmalichtbogen zu stabilisieren, sowie neue Lichtbogen-Segmentierungsprotokolle für Löcher, die die Qualität von Hypertherms bereits marktführendem True-Hole-Verfahren noch übertreffen.
Anlagen-Betriebszeit
Trotz der enormen Technologie, die in der XPR steckt, ist die Anlage tatsächlich weniger komplex. Sensoren in der Stromquelle liefern Diagnosecodes und deutlich verbesserte Systemüberwachungsdaten. Dies reduziert Fehlerbeseitigungszeiten und liefert proaktive Anlagen-Wartungsdaten für bessere Systemoptimierung.
Außerdem wurde die Anlage mit weniger Konsolen und Anschlüssen entwickelt, so dass die Bediener weniger Zeit mit Einrichtung und mehr Zeit mit Schneiden verbringen können. Hierbei helfen zum Beispiel Merkmale wie eine Anschlussvorrichtung namens EasyConnect™, mit der ein Bediener den Brenner schnell in die Brennerkonsole stecken kann, ohne dass dafür Werkzeuge benötigt werden. Die zum Patent angemeldete QuickLock™-Elektrode lässt sich mit einer einfachen Vierteldrehung festziehen, was die Zeit für die Auftragseinrichtung weiter reduziert, und durch die neue Konstruktion kann ein Bediener einen Brenner sehr schnell mit nur einer Hand austauschen. Alle Konsolen bieten erweiterte Autogasfähigkeit, wodurch die Bediener alle Schneidaufträge direkt an der CNC oder WiFi in der Stromquelle auswählen und implementieren können, um die Anlage (oder mehrere Anlagen) fernüberwachen zu können.
Die Betriebsdauer der Anlage und natürlich auch die Gesamtbetriebskosten werden außerdem durch Verbesserungen der Standzeit der Verschleißteile beeinflusst. Ein zum Patent angemeldetes Feature namens Cool nozzle™ bietet Flüssigkeitskühlung direkt an der Düse, was die Standzeit der Verschleißteile um 40 % verlängert. Die patentierte PowerPierce®-Technologie leistet für den Schutzschild im Wesentlichen dasselbe. Sie versieht den Schutzschild mit Flüssigkeitskühlung, wodurch er beim Lochstechen tatsächlich geschmolzenes Metall abweisen kann. Dies verhindert Schäden am Schutzschild. Ein Ventil in der Brenneranschlussbuchse bringt schnellere und genauere Steuerung der Gasdurchflüsse für deutlich längere Lebensdauer von Sauerstoffverfahren und viel schnelleres Herunterfahren. Indem Fehler beim Herunterfahren bei den meisten Anwendungen eliminiert werden, erreichen wir eine fast dreimal längere Standzeit der Verschleißteile als jede andere Anlage, wie unten gezeigt. Weniger Zeit für das Auswechseln von Verschleißteilen bedeutet mehr Zeit zum Schneiden und für andere Wertschöpfungsaktivitäten.
Da haben Sie es also. Die Kombination aus höheren Schnittgeschwindigkeiten, besserer Schnittqualität und längerer Betriebszeit der Anlage führt zur höheren Produktivität der XPR300.
Wie kann ich produktiver werden?