Die 10 häufigsten Fehler beim Plasmaschneiden
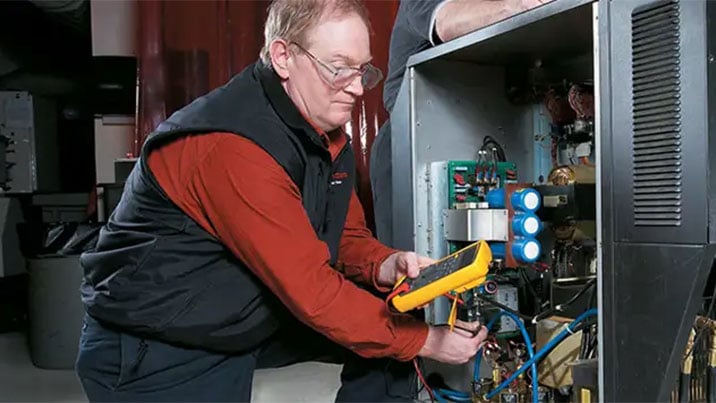
Erfahrene Bediener mit gepflegtem Pilotlichtbogen-Steuerungs-Zubehör können einem Betrieb viele Ausfallstunden und tausende US-Dollar an Betriebskosten einsparen. Diese Ersparnisse führen zu höheren Gewinnen bei Ihren Schneidprozessen und für Ihr Unternehmen. Vermeiden Sie die folgenden typischen Fehler:
- Einsatz der Verschleißteile bis zum Ausfall
Wenn Sie sich Ihre gebrauchten Teile ansehen, dann sind vermutlich einige darunter, die bis zum Ausfall eingesetzt wurden. Der Einsatz stark abgenutzter Verschleißteile kann nicht nur ein gutes Metallwerkstück beschädigen, sondern auch teure Brennerausfälle und unnötige Ausfallzeiten verursachen. Die Teile bis zur vollständigen Abnutzung einzusetzen, ist ein Fehler, der sich leicht vermeiden lässt. Es gibt verschiedene Anzeichen für abgenutzte Verschleißteile; erfahrene Benutzer können häufig schon anhand der Farbe oder Geräusche des Lichtbogens einen Verschleiß der Teile erkennen. Ein weniger auffälliges Anzeichen ist eine Veränderung der Brennerhöhe. Am besten lässt sich der Zustand der Brennerteile jedoch durch eine regelmäßige Überprüfung der Schnittkantenqualität am Metallwerkstück sowie der Brennerteile, sobald der Schnitt schlechter wird, beurteilen. Protokollieren Sie die durchschnittliche Standzeit der Verschleißteile im Laufe der Zeit (Anzahl der Starts oder die Lichtbogennutzungszeit) und entwickeln Sie einen Leitfaden für die erwartete Standzeit nach Stromstärke, Material und Materialstärke. Der Bediener kann anhand der durchschnittlichen Standzeit die Teile rechtzeitig überprüfen und austauschen und so einen Ausfall verhindern. - Zu früher Austausch von Verschleißteilen
Am entgegengesetzten Ende des Spektrums steht der Fall, dass Verschleißteile zu früh ausgewechselt werden. Statt Verschleißteile nach einer festen Anzahl von Stunden auszutauschen, sollte der Bediener sich ansehen, wie stark abgenutzt die Verschleißteile sind. Gibt es Rillen an der Innen- oder Außenseite der Düse? Ist die Öffnung nicht mehr rund? Wenn ja, muss sie ausgetauscht werden. Wenn nicht, kann sie wahrscheinlich weiterverwendet werden. Um festzustellen, ob eine Elektrode verschlissen ist, sehen Sie sich das Hafnium-Loch in der Mitte an und tauschen Sie sie aus, wenn das Loch zu tief ist. Gaswirbelringe sollten nur dann ausgetauscht werden, wenn bei näherer Betrachtung Schmutz oder Schmiermittel in den Öffnungen, Risse, Lichtbogeneinbrände oder übermäßige Abnutzung festgestellt werden. Das Gleiche gilt für Schutzschilde, die nur dann ausgewechselt werden sollten, wenn Anzeichen einer Beschädigung sichtbar sind. Schutzschilde können oft von Metallspritzern gereinigt und dann wiederverwendet werden. - Einsetzen der falschen Parameter und Teile für den Auftrag
Die Auswahl der Verschleißteile hängt vom Material und der Materialstärke, der Stromstärke, dem eingesetzten Plasmagas und anderen Schneidparametern ab. Die geeigneten Verschleißteile für verschiedene Schneidarbeiten können Sie der Bedienungsanleitung entnehmen. Die Verwendung falscher Verschleißteile kann eine verkürzte Standzeit und schlechtere Schnittqualität zur Folge haben.
Besonders wichtig ist es, die Teile mit der korrekten Stromstärke zu betreiben. Die beste Schnittqualität und Standzeit wird gewöhnlich erreicht, wenn die Stromstärke auf 95 % der Düseneinstellungen eingestellt wird. Ist die Stromstärke zu niedrig, dann wird der Schnitt unsauber; ist sie zu hoch, dann verkürzt sich die Düsenlebensdauer. - Falscher Zusammenbau des Brenners
Beim Zusammenbauen des Brenners müssen die Teile korrekt ausgerichtet sein und zusammengefügt werden. So wird ein guter elektrischer Kontakt und korrekter Gas- und Kühlmitteldurchfluss durch den Brenner sichergestellt. Legen Sie beim Auswechseln die Verschleißteile auf ein sauberes Tuch, damit der Brenner nicht durch Schmutz oder Metallstaub verunreinigt wird. Saubere Bedingungen während der Montage des Brenners sind äußerst wichtig und werden häufig vernachlässigt. Verwenden Sie beim Auftragen des Schmiermittels auf den O-Ring gerade so viel, dass dieser etwas Glanz erhält. Zu viel Schmiermittel kann zu einer Verstopfung des Gaswirbelelements und Verunreinigung des Brenners durch Metallstaub führen. Dies kann eine unkontrollierte Lichtbogenbildung in der Plasmakammer und schließlich den Ausfall des Brenners zur Folge haben. Schmiermittel sollte niemals auf den Brenner aufgetragen werden – es kann eine schädliche Lichtbogenbildung und Einbrand im Brenner verursachen. - Vernachlässigung der routinemäßigen Wartung
Mit der richtigen Pflege können Brenner monatelang oder sogar mehrere Jahre halten. Die Brennergewinde müssen sauber gehalten und die Anschlussstellen sollten auf Verunreinigung oder mechanische Schäden überprüft werden. Schmutz, Metallstaub oder überschüssiges Schmiermittel am O-Ring sollte vom Brenner entfernt werden. Um den Brenner zu reinigen, verwenden Sie ein Wattestäbchen und ein Reinigungsmittel für elektrische Kontakte oder Wasserstoffperoxid. - Keine Überprüfung des Gas- und Kühlmitteldurchflusses
Gas- und Kühlmitteldurchfluss sowie -druck sollten täglich überprüft werden. Wenn der Durchfluss unzureichend ist, werden die Verschleißteile nicht richtig gekühlt und es verkürzt sich die Standzeit. Ein unzureichender Kühlwasserdurchfluss aufgrund von abgenutzten Pumpen, verstopften Filtern, niedrigen Kühlmittel-Füllständen usw. ist eine häufige Ursache für einen Brennerausfall. Ein konstanter Gasdruck ist wichtig, um einen Schneidlichtbogen aufrechtzuerhalten. Ein übermäßiger Gasdruck ist eine häufige Ursache für Schwierigkeiten beim Starten, d. h. das Zünden eines Lichtbogens im Brenner schlägt fehl, obwohl alle anderen Bedingungen für einen normalen Betrieb gegeben sind. Ein zu hoher Gasdruck verursacht außerdem einen schnellen Verschleiß der Elektroden. Außerdem muss Plasmagas sauber gehalten werden, um eine kurze Standzeit der Verschleißteile und des Brenners zu vermeiden. Druckluftanlagen sind besonders anfällig für eine Verunreinigung durch Öl, Feuchtigkeit und Schmutzpartikel. - Lochstechen bei zu geringer Höhe
Der Abstand zwischen der Brennerspitze und dem Werkstück ist ein kritischer Faktor für die Schnittqualität und Standzeit. Selbst leichte Abweichungen bei der Brennerhöhe können die Winkelstellung der geschnittenen Oberfläche beeinflussen. Die Höhe des Brenners während des Lochstechens ist besonders wichtig. Ein häufiger Fehler ist das Lochstechen bei zu geringer Höhe. Dadurch spritzt geschmolzenes Metall auf die Vorderseite der Düse und den Schutzschild, wodurch die Teile beschädigt werden und Schnittqualitätsprobleme auftreten. Der Lichtbogen kann sogar beim Lochstechen oder Schneiden, d. h. während der Brenner das Metall berührt oder entlang der Metalloberfläche fährt, erlöschen. Wenn der Lichtbogen erlöscht, dann fällt die Elektrode, die Düse, das Gaswirbelelement und manchmal sogar der Brenner aus. Beim Lochstechen mit einer Höhe von 1,5–2X schützt die empfohlene Schneidhöhe den Brenner und die Teile vor Beschädigung. - Zu schnelles oder langsames Schneiden
Zu schnelles oder langsames Schneiden verursacht Schnittqualitätsprobleme. Ist die Geschwindigkeit zu langsam, dann tritt am Werkstück eine „Bartbildung wegen zu langsamer Geschwindigkeit“, d. h. eine große blasige Ansammlung von Bart entlang der Unterkante, auf. Langsame Schnittgeschwindigkeiten können zudem zu einer breiteren Schnittfuge und übermäßigen Menge von Metallspritzern führen. Wird zu schnell geschnitten, dann hinkt der Lichtbogen in der Fuge hinterher und verursacht eine gefaste Kante, eine schmale Fuge und eine kleine, harte Bartwulst entlang der Unterkante des geschnittenen Teils. Ein Bart, der durch schnelle Schnittgeschwindigkeiten entsteht, ist schwer zu entfernen. Bei korrekter Schnittgeschwindigkeit bleibt die Bartbildung minimal – das Ergebnis ist eine saubere Kante, die nur wenige Nachbesserungen vor dem nächsten Schritt im Herstellungsprozesses erfordert. - Längenzunahme des Lichtbogens
Eine Längenzunahme des Lichtbogens kann am Anfang und Ende des Schnitts vorkommen, wenn sich der Lichtbogen „strecken“ (von einem geraden, senkrechten Pfad abweichen) muss, um das Metall zu erreichen. Eine Längenzunahme des Lichtbogens kann dazu führen, dass der Lichtbogen in die Seitenwand der Düse schneidet. Bei einem Kantenstart sollte der Plasmalichtbogen mit der Düsenöffnung mittig über der Kante des Werkstücks gestartet werden. Es ist wichtig, dies bei Stanz-Plasmaarbeiten zu beachten. Eine Längenzunahme des Lichtbogens kann dazu führen, dass der Lichtbogen in die Seitenwand der Düse schneidet. Bei einem Kantenstart sollte der Plasmalichtbogen mit der Düsenöffnung mittig über der Kante des Werkstücks gestartet werden. Es ist wichtig, dies bei Stanz-Plasmaarbeiten zu beachten. Hier wird der Lichtbogen an einem gestanzten Loch gestartet. Bei dieser Anwendung sollte der Lichtbogen an der Kante und nicht an der Mitte des gestanzten Lochs gestartet werden. Zur Längenzunahme des Lichtbogens kann es auch am Ende des Schnitts kommen, wenn der Brenner laut Programm bei eingeschaltetem Lichtbogen über die Platte hinausfahren oder die Ausfahrt der Fuge des zuvor geschnittenen Metalls folgen soll. Dieser Effekt kann durch den Zeitpunkt des Signals zum Ausschalten des Lichtbogens und die Programmierung der Ausfahrt minimiert werden. - Beschädigung des Brenners wird durch Aufprall
Ihr Brenner kann durch Kippen und Aufpralle irreparabel beschädigt werden. Brennerkollisionen mit dem Werkstück können vermieden werden, indem die Formschneidanlage darauf programmiert wird, um Werkstücke herumzufahren (statt darüber). Brennerhöhensensoren schützen ebenfalls vor Brennerkollisionen, indem sie Abweichungen beim Material ausgleichen. Spannungsgesteuerte Höhensteuerungen können den Brenner jedoch nicht immer schützen. Ein häufiges Problem ist das so genannte „Eintauchen“, das am Ende eines Schnitts auftreten kann, wenn der Brenner der Fuge zu lange folgt. (Die Brennerhöhensteuerung „taucht in die Platte ein“, um die erhöhte Spannung beim Strecken des Lichtbogens auszugleichen.) Dieser Effekt kann durch eine sorgfältige Programmierung der Ausfahrt und die Brennerhöhensteuerungsfunktion minimiert werden. Schließlich können Schäden am Brenner im Falle einer Kollision durch Brennermontagevorrichtungen mit Abschaltmechanismus verhindert werden.