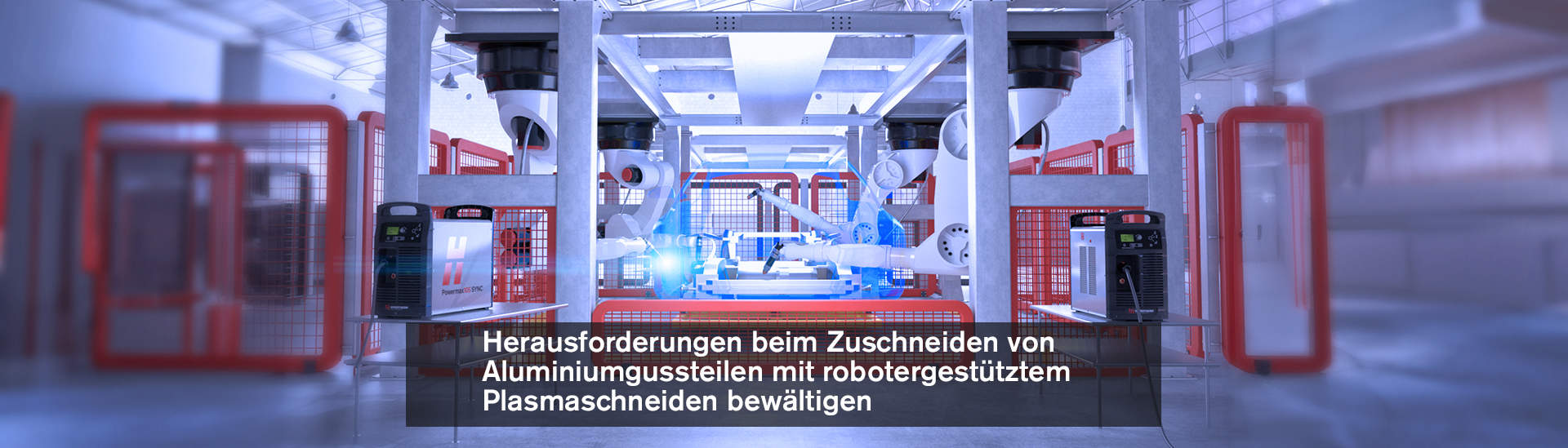
Automobilhersteller müssen bezüglich Qualität, Effizienz und Kostenreduzierung herausragend sein, um wettbewerbsfähig zu bleiben. Die Rentabilität hängt davon ab, ob Chancen zur Verbesserung der Effizienz identifiziert werden können. Deshalb setzen die globalen Automobilhersteller zunehmend auf Giga-Gussverfahren – großflächige Rahmen aus einem Guss –, wodurch die Notwendigkeit entfällt, Dutzende von Karosserieteilen miteinander zu verschweißen. Weniger Teile bedeutet ein geringeres Fahrzeuggewicht, eine Erhöhung der Kraftstoffeffizienz und die Berücksichtigung der wachsenden Nachfrage nach batteriebetriebenen Fahrzeugen und Fahrzeugen mit effizienteren Verbrennungsmotoren.
Überschüssiges Material aus der Form muss entfernt werden, sobald das Gussteil aus der Presse entnommen wird. Die Technologie des robotergestützten Plasmaschneidens hilft hier, die Automobilproduktion zu revolutionieren.
REUTERS
„Automobilhersteller, die Aluminium-Gussmaschinen einsetzen, behaupten, dass sie die Investitionen für den Bau von Fahrgestellen – der zweitteuersten Komponente eines Fahrzeugs nach dem Motor – um 40 % reduzieren können.“
Riccardo Ferrario,
General Manager, IDRA Group
Herausforderungen für Automobilhersteller
-
Herkömmliche Verfahren zur Materialentfernung, wie z. B. Zuschneidpressen, schränken das Produktdesign oft ein, verursachen hohe Investitionskosten, lange Rüstzeiten und führen aufgrund von Variationen bei den Teilen zu höheren Ausschussraten
-
Fachkräftemangel erhöht die Kosten und verringert die Produktivität, insbesondere hinsichtlich der Qualität der Materialentfernung
-
Formenwechsel führen zu kostspieligen Werkzeugmodifikationen
-
Zeitaufwändige Methoden zur Flash-/Materialentfernung wirken sich auf die Zykluszeit aus
-
Manuelle und halbautomatische Verfahren erzeugen Metallabspäne, die zu erhöhten Ausfallzeiten führen und die Unversehrtheit des Endgusses negativ beeinflussen können
-
Manuelle Arbeit erhöht das Risiko von Arbeitsunfällen
Herausforderungen von Zuschneidpressen und robotergestützten Plasmaschneidlösungen
Herausforderungen | Lösungen |
---|---|
Variationen beim Gießen von Teilen können dazu führen, dass das Teil in der Zuschneidpresse stecken bleibt. | Mit kleinen Werkzeugänderungen kann ein neuer Roboterpfad programmiert werden, um beliebige Teile zuzuschneiden |
Keine schnelle Anpassung an verschiedene Teile/Geometrieformen, die von der Druckgussmaschine verarbeitet werden | Robotergestütztes Plasmaschneiden kann schnell programmiert werden, um neue Teile und Formen zu schneiden, dabei kann eine flexible Zuschneidzelle mehrere Gussdesigns aufnehmen |
Enge Toleranzen führen zu dimensionslosem Materialabfall | Beim Plasmaschneiden dient ein größerer Abstand zwischen Werkzeug und Werkstück (Stand-off) der Kollisionsvermeidung |
Massive Zuschneidpressen nehmen wertvollen Platz in der Fertigungshalle ein | Plasmaschneider benötigen nur minimalen Platz, lassen sich einfach in Roboter integrieren, erfordern wenig Wartung und haben eine lange Lebensdauer |
Automobilhersteller vertrauen auf Plasmaschneidsysteme von Hypertherm
Die Powermax SYNC®-Systeme sind so konzipiert, dass sie sich problemlos zum Schneiden von Metallgussteilen in Roboterzellen integrieren lassen, wodurch im Vergleich zu alternativen Technologien der erforderliche Zeit- und Arbeitsaufwand sowie die Betriebskosten erheblich gesenkt werden. Powermax weist entscheidende Unterschiede zu Konkurrenzsystemen und anderen Technologien auf, die es zur bevorzugten Wahl für führende Automobilhersteller – und Elektrofahrzeuge auf den Straßen von heute – machen.
Unterscheidungsmerkmale der Powermax SYNC-Lösung
Der schnelle Werkstückwechsel spart Zeit und Arbeit
Unabhängig von der Variation des Gussteils oder einer abweichenden Teilegeometrie kann ein neuer Roboterpfad programmiert werden, um beliebige Werkstücke und Stile in der Roboter-Zuschneidzelle zuzuschneiden.
Der größere Abstand zwischen Werkzeug und Werkstück vereinfacht die Roboterprogrammierung
Durch größere Abstände zwischen Werkzeug und Werkstück im Vergleich zum Faserlaser eignet sich Plasma besser für Roboteranwendungen, bei denen Teilevariationen zu erwarten sind. So werden kostspielige Ausfallzeiten durch Kollisionen zwischen Werkzeug und Werkstück verhindert.
DIE WAHL IST KLAR
Führende Automobilhersteller testeten Technologien, mit denen sie stärker vertraut waren, einschließlich Faserlaser, und haben festgestellt, dass Powermax-Plasma für das Zuschneiden von Aluminiumguss die beste Lösung ist.
Patentiertes einteiliges Einsatz-Verschleißteil mit Datenfähigkeit verhindert Bedienerfehler
Mit der integrierten intelligenten RFID-Funktion und einem revolutionären einteiligen Einsatz-Verschleißteil mit fortschrittlicher SmartSYNC-Brennerkommunikation können Sie die Leistung für Starts, Übertragungen und Lichtbogen-Einschaltzeiten analysieren.
-
Unsere patentierte Technologie ermöglicht einen schnellen Werkzeugwechsel und eliminiert nahezu alle Stillstandzeiten
-
Intelligentes, einteiliges Verschleißteil signalisiert die Stromquelle des Einsatz-Typs am Brenner
-
Die Schneidanlage stellt automatisch den richtigen Strom und das richtige Gas ein, um die Schnitte zu optimieren und die Beteiligung des Bedieners zu eliminieren
-
Einteiliges Einsatz-Verschleißteil – kosteneffizient und recycelbar
Ein einzigartiger einteiliger Einsatz mit integrierter Intelligenz
Mit integrierter Intelligenz und einem revolutionären einteiligen Einsatz-Verschleißteil mit fortschrittlicher Brennerkommunikation verbessert die Powermax SYNC-Konnektivität die Effizienz, vereinfacht das Bestandsmanagement und minimiert Ausfallzeiten. Anhand der Leistungsdaten der Einsatz-App, der Benutzeroberfläche des Systems und einer kompatiblen CNC treffen Sie fundierte Entscheidungen zur Verbesserung Ihres Schneidbetriebs.
Warum Hypertherm Associates?
Bei allem, was wir tun, glauben wir daran, das Unmögliche herauszufordern. Durch die gemeinsame Belebung – sowohl Ihrer als auch unserer – Vorstellungskraft gestalten wir Produkte, die das globale Umfeld inspirieren sowie benutzer- und umweltfreundlich sind. Unsere bewährten Technologien für das Schneiden und Formen tragen dazu bei, eine stärker vernetzte und interessantere Welt zu schaffen.
Besprechen Sie mit uns Ihre Anforderungen an das Zuschneiden von Gussteilen
Unser Follow-up-Prozess:
Ihr Ansprechpartner wird sich mit Ihnen in Verbindung setzen, um Ihr Projekt und Ihre Herausforderungen besser verstehen zu können und ein Follow-up zu organisieren, einschließlich des direkten Zugangs zu unserem Ingenieurteam, das sich auf Anwendungen zum Zuschneiden von Gussteilen spezialisiert hat.
Die nächsten Schritte können Folgendes beinhalten:
-
Produkttests
-
Tests der Verfahrensnachweise
-
Zusammenarbeit zwischen Automobilherstellern und bevorzugten Partnern